JungleJim
Established Member
I really want to have a go at making a Greg Klassen river style coffee table like these ones here http://gregklassen.com/collection/river/
when I was at Surrey Timbers yesterday, i picked up this piece of pippy oak. The plan is to cut in two flip it round for the two sides, It was going to knock up a jig and get both sides flat and parallel with a router. I was going to remove the bark but leave the interesting "knobbly" bits what do you think?. Is there a best way of sanding and finishing oak like this?
I haven't picked the wood for legs yet but was thinking of using 2x2 oak for the legs and 2x1 for the rails.
I've got a friendly glazier near me so will pop in Monday to see what he can supply in the way of tinted glass. I've never cut glass before so this will be a new one for me.
any tips and things that could catch me out would be greatly appreciated.
Thanks
James
when I was at Surrey Timbers yesterday, i picked up this piece of pippy oak. The plan is to cut in two flip it round for the two sides, It was going to knock up a jig and get both sides flat and parallel with a router. I was going to remove the bark but leave the interesting "knobbly" bits what do you think?. Is there a best way of sanding and finishing oak like this?
I haven't picked the wood for legs yet but was thinking of using 2x2 oak for the legs and 2x1 for the rails.
I've got a friendly glazier near me so will pop in Monday to see what he can supply in the way of tinted glass. I've never cut glass before so this will be a new one for me.
any tips and things that could catch me out would be greatly appreciated.
Thanks
James
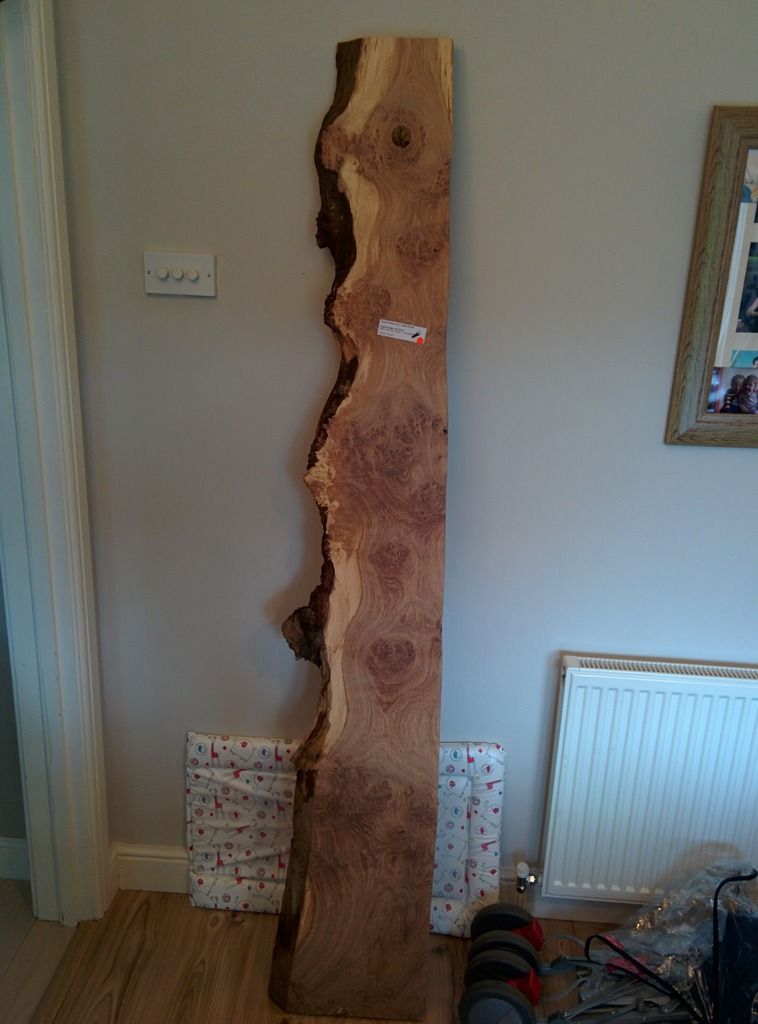
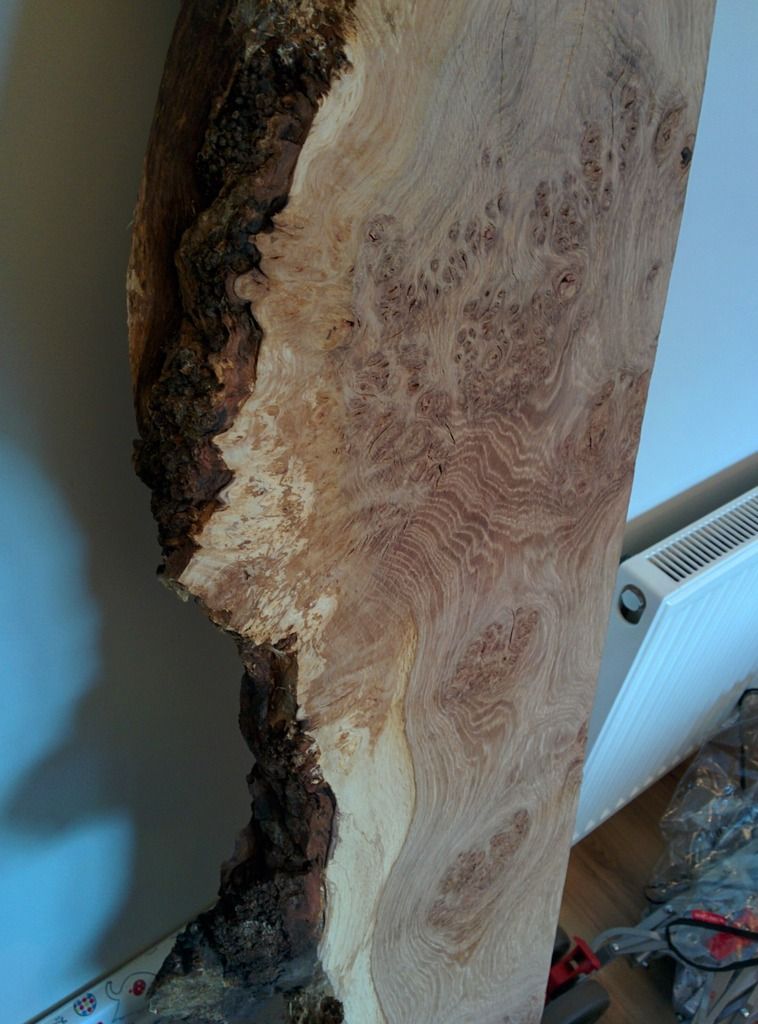