swagman
Established Member
A few weeks ago I ordered some 280grt Silicon Carbide Powder to flatten my hard Silicon Carbide Stones; the powder arrived a week ago. I also upgraded my old sheet of float glass to a 12mm (2x laminated); 1250mmL x 300mmD. http://www.glassforeurope.com/en/pro...s-of-glass.php
The stone chosen had a noticeable hollow down its full length; the surface of the glass was 1st sprayed with water, before applying 5 grams of powder within a localized area; its important to bear in mind that these Silicon Carbide Powder's itself break down in size the longer you work it; as a general rule of thumb- when you can no longer hear the sound of the grit working the surface of the stone its an indicator you need to add some additional fresh powder; over a 30 min period; 2 grams of additional powder was added every 10 min. To achieve a totally flat surface over the Silicon Carbide Stone took me 30 min of work; longer than I initially anticipated; most likely that's an indicator that the commensurate grit of 280 is not coarse enough. I have ordered 400g of the 150grt for the next trial.
Random spraying of water over the surface of the Silicon Carbide slurry is a requirement to prevent the effects of air drying. Not difficult to identify, as the drying slurry will start to impede the free movement of the stone across the glass surface.
I should make mention that I previously trialled a Course DMT Diamond Stone to flatten these hard Silicon Carbide Stone's; the diamond grit was non existent after about 10 min of work. imo ; its the bonding agent that adheres the diamond grit to the top surface of the plate that cannot withstand the hardness of these Silicon Carbide Stone's.
Stewie;
The stone chosen had a noticeable hollow down its full length; the surface of the glass was 1st sprayed with water, before applying 5 grams of powder within a localized area; its important to bear in mind that these Silicon Carbide Powder's itself break down in size the longer you work it; as a general rule of thumb- when you can no longer hear the sound of the grit working the surface of the stone its an indicator you need to add some additional fresh powder; over a 30 min period; 2 grams of additional powder was added every 10 min. To achieve a totally flat surface over the Silicon Carbide Stone took me 30 min of work; longer than I initially anticipated; most likely that's an indicator that the commensurate grit of 280 is not coarse enough. I have ordered 400g of the 150grt for the next trial.
Random spraying of water over the surface of the Silicon Carbide slurry is a requirement to prevent the effects of air drying. Not difficult to identify, as the drying slurry will start to impede the free movement of the stone across the glass surface.
I should make mention that I previously trialled a Course DMT Diamond Stone to flatten these hard Silicon Carbide Stone's; the diamond grit was non existent after about 10 min of work. imo ; its the bonding agent that adheres the diamond grit to the top surface of the plate that cannot withstand the hardness of these Silicon Carbide Stone's.
Stewie;
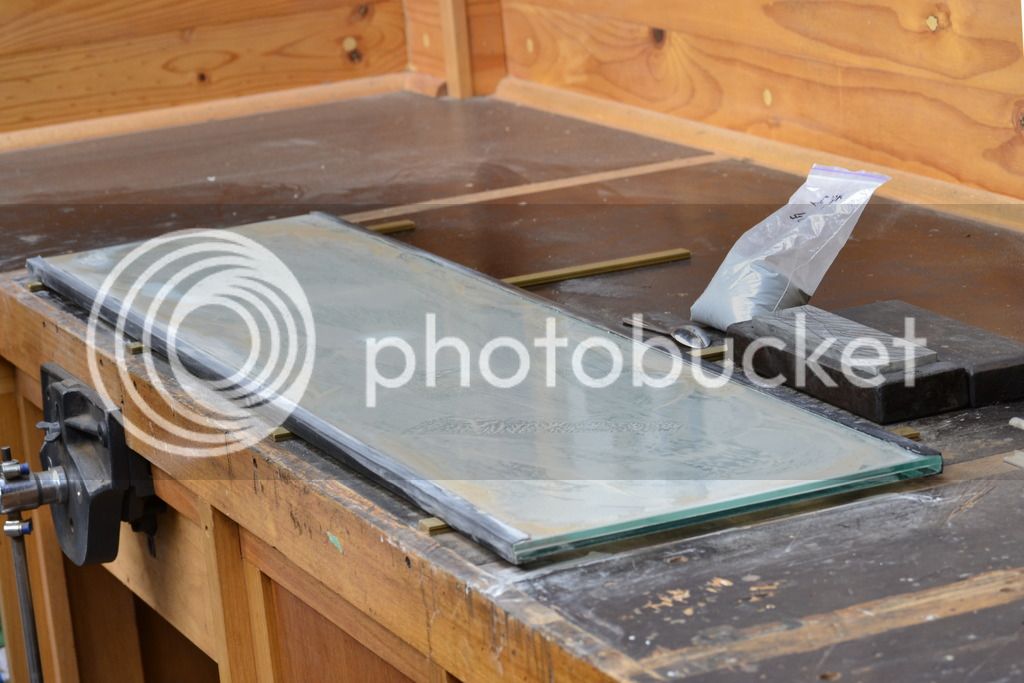
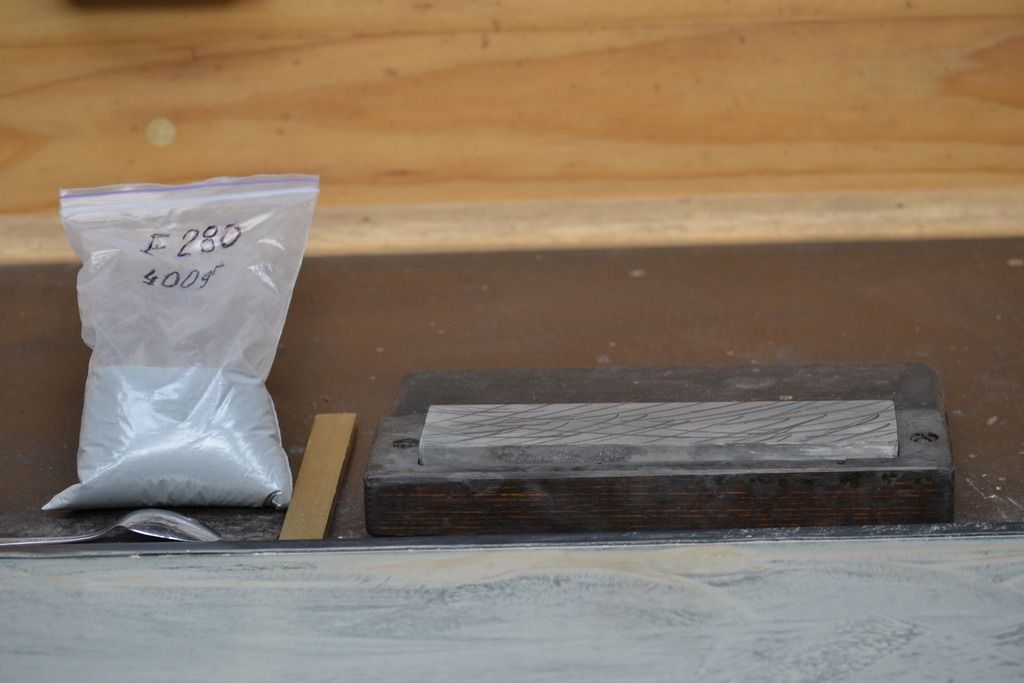
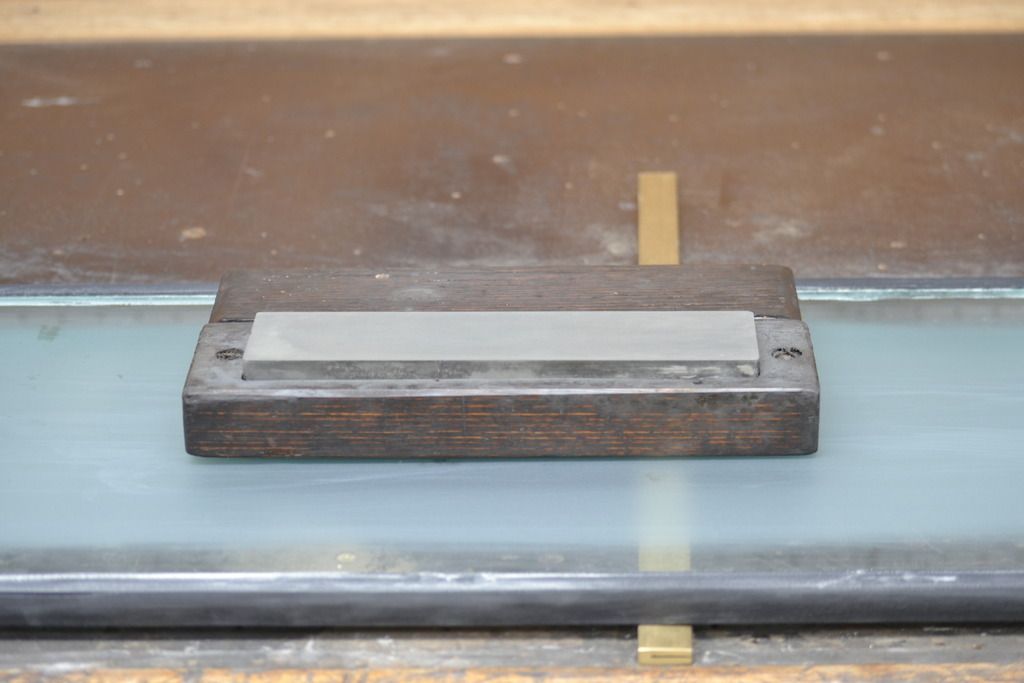