Derek Cohen (Perth Oz)
Established Member
Ever since the 2007 tool competition at Wood Central, in which Kyle Barrett won very deservedly with his amazing bridle plough, I have wanted to build one. It was based on the Mathieson bridle plough, as is mine below.
This has to be my toughest plane build to date. The number of times I wished for a short cut, then stopped myself, or wondered whether the next saw stroke would destroy the many hours of work. That is partly the reason I built this plane - because I thought it too difficult.
There is a record of the build, with many pictures - many! - but thankfully little text, so you can skim through them if you desire: http://www.inthewoodshop.com/ShopMadeTo ... Build.html
The wood is West Australian She-oak, with Jarrah as a contrast. Most of the brass work is mine, although the depth stop came from a parts Mathieson wedged plough. Finish is Organoil buffing oil and wax.
Here are a few images ...
The bridle fence ...
The plough works very well ...
Nice square and clean grooves ...
There is a full set of 8 unused vintage irons ..
Regards from Perth
Derek
This has to be my toughest plane build to date. The number of times I wished for a short cut, then stopped myself, or wondered whether the next saw stroke would destroy the many hours of work. That is partly the reason I built this plane - because I thought it too difficult.
There is a record of the build, with many pictures - many! - but thankfully little text, so you can skim through them if you desire: http://www.inthewoodshop.com/ShopMadeTo ... Build.html
The wood is West Australian She-oak, with Jarrah as a contrast. Most of the brass work is mine, although the depth stop came from a parts Mathieson wedged plough. Finish is Organoil buffing oil and wax.
Here are a few images ...
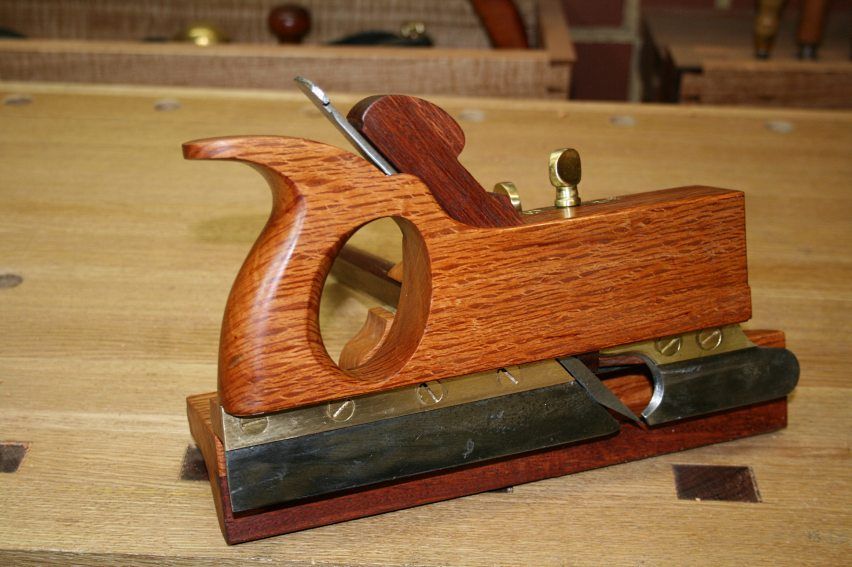
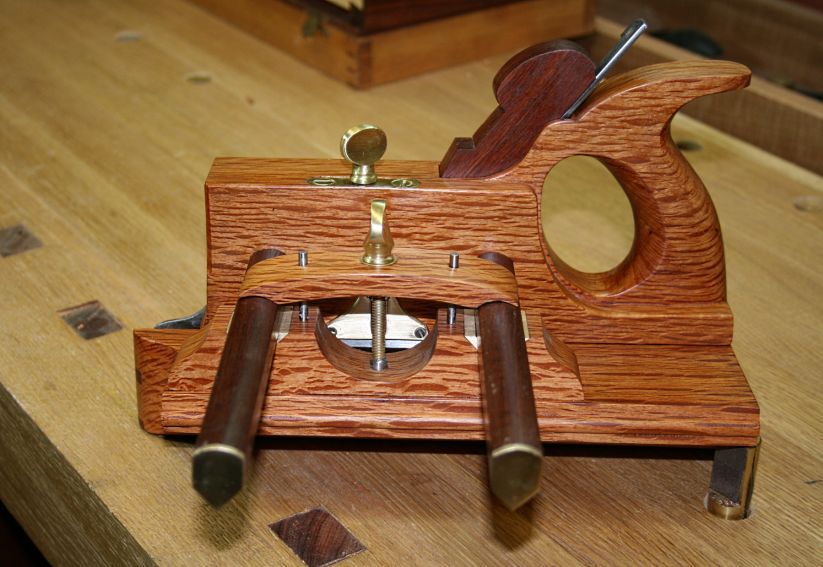
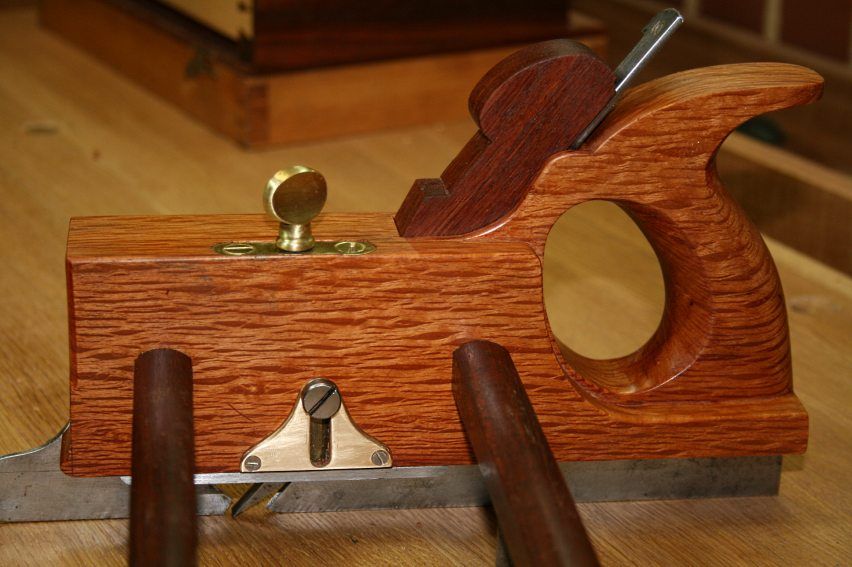
The bridle fence ...
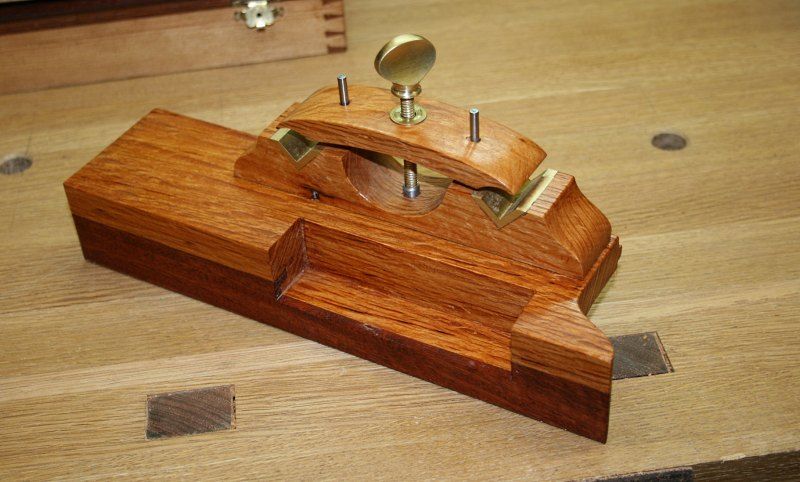
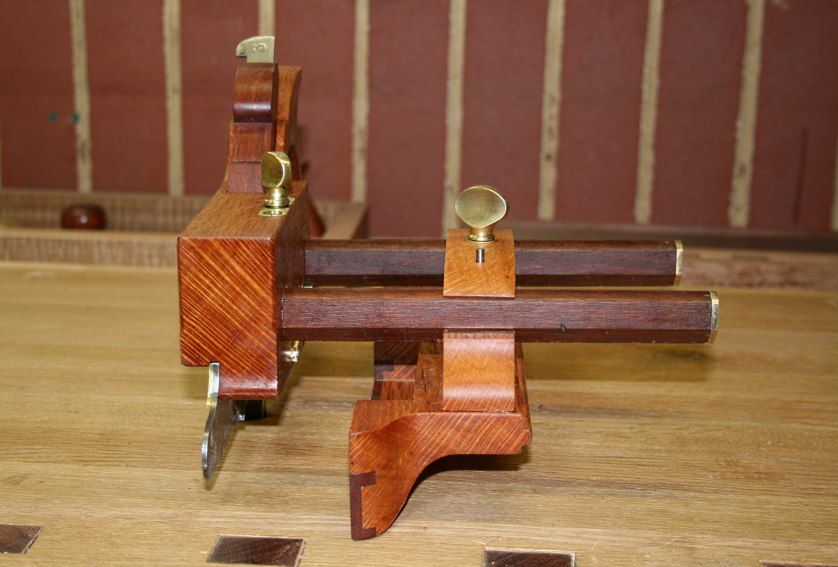
The plough works very well ...
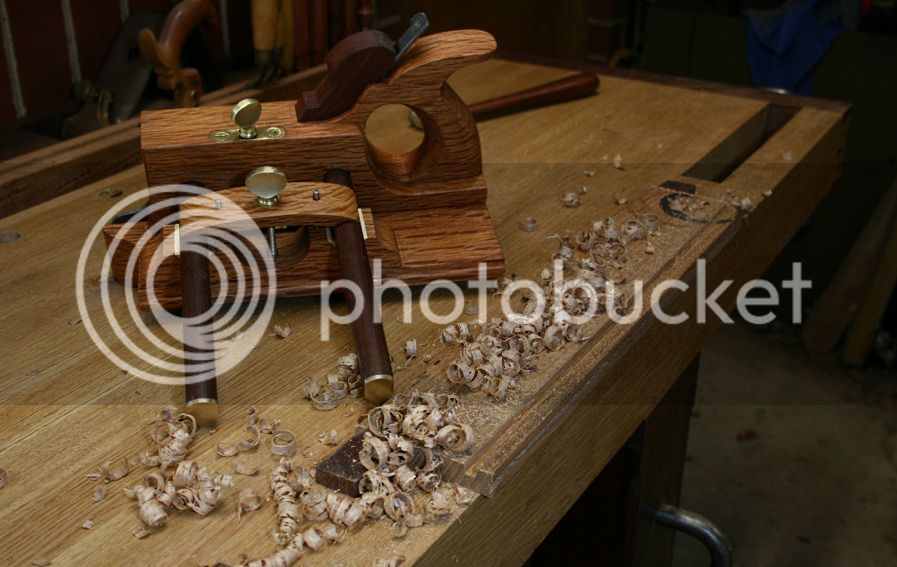
Nice square and clean grooves ...
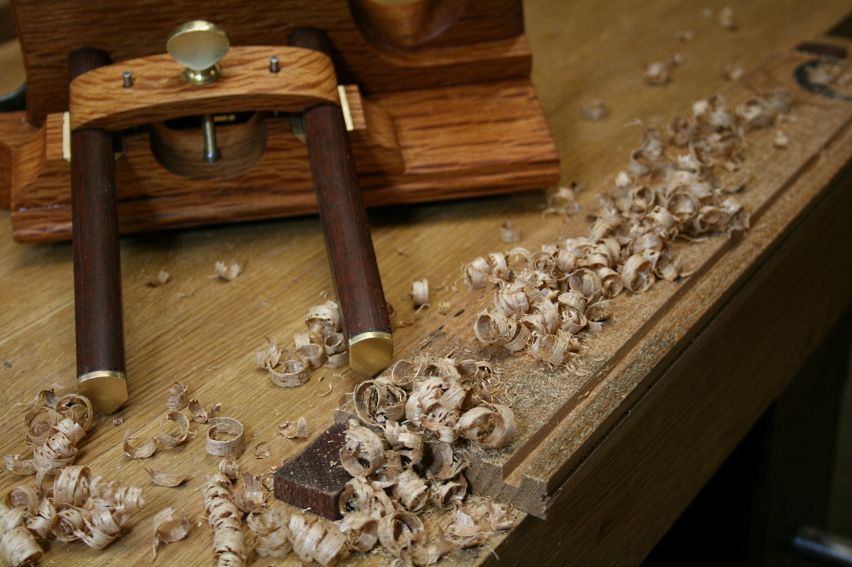
There is a full set of 8 unused vintage irons ..
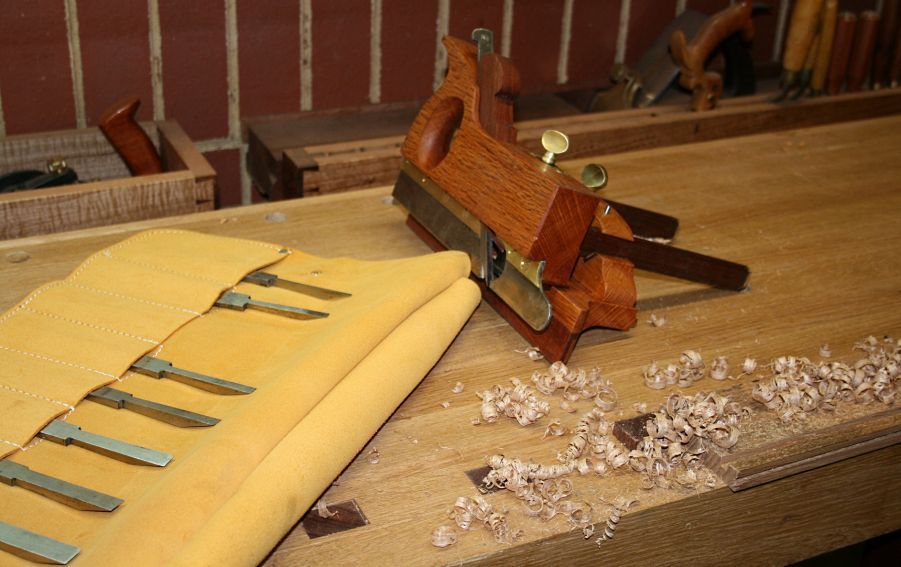
Regards from Perth
Derek