Derek Cohen (Perth Oz)
Established Member
Part I: Morticing made easy
Recently I built two beds, which I have just got back to. Having completed them, I discovered that they were 40mm too long and too wide! Duh ... after many measurement checks!
Obviously this meant pulling them apart and shortening the lengths and widths.
The head-and foot board leg joinery is loose mortice-and-tenon. 110mm long x 10mm wide. This was made fairly easy with a Domino machine. The loose tenons were sized on a jointer/thickness-planer, and then rounded over on a router table. All wood is Jarrah. The aim was for an exact fit.
I am really appreciating the extra bench top space afforded by the new MFT table (yes, the Veritas hold down, although it is sized for a 19mm dog hole works very well on a 20mm dog hole) ...
I made a small positioner to mark the centre of the domino, and plunged for the outer ends ...
Then complete the mortice by nibbling away the centre section ..
Tight fit in the rail ..
Tight fit in the post ..
This was taken during the earlier build, and how the legs are once again ...
Part II: Construction
Rebuilding two single beds was a lot of work. To correct the oversizing, the beds were taken apart, and the rails shortened. Then the head- and foot boards were shortened, re-morticed, and re-glued. And finally, all the slats had to be shortened by 40mm, which was not a simple matter. More on this in a while.
About the beds and their design: One of the reasons I am posting the build details is that I hope it helps others in a similar position.
About 25 years ago I build a fantastic Jarrah King size double bed for my wife and myself. It was deliberately built 25mm over-width (which made it appear even wider) ...
The reason for this is my wife is an incredibly light sleeper, especially since our son was born 3 decades ago, and will wake up if I even roll over in bed. We spent a small fortune on mattresses ... all those special ones which promised to smother any vibration. Well, all I can say is that I am lucky I was not smothered in my sleep! The solution for a while was the King size bed with two single mattresses, pushed together, but able to be pulled apart by 25mm if I was restless in sleep. The issue with a single bed is that vibration is transmitted by the bed frame. Consequently, I decided to build two beds which would actually become a double bed, but able to be separated if needed. I will explain this in a while.
As mentioned, these beds are done. Now I have a new headboard to build, which is for another time.
My wife stipulated no tail board for the beds as they make is far more work when making up a bed. My preference was for clean lines, which meant that I did not want visible bed bolts. Bed bolts are used, but they are hidden.
Here is the start of re-assembling the beds ..
The head and tail ends are constructed with a mortice-and-tenon (this was the post made recently on morticing with a Domino). The side railed are connected with hidden bed bolts.
Here are the side rail connections. When the rails were shortened, so the bolts in these rails needed to be ..
The bolts are fixed into inserted metal threads in the posts permanently with Loctite. The post and rail are locked with double loose mortice-and-tenons (no glue) and then bolted in the rail ...
The slats for the beds are made in two parts ...
They are a T-section, which makes for a very rigid structure ...
... and screwed down for extra strength.
Now the secret to making a double bed out of two singles lies with the rails. The slats on the outer sides are lower by 6mm (1/4") to aid in preventing the mattress slipping off the base, but also low enough to make it easier to tuck in sheets, etc.
The slats on the inside rails are flush with the top ...
... enabling two mattresses to be placed alongside one another. Conversely, it is easy to pull them apart.
The Jarrah is finished in hard wax oil, and the result is quite stunning. Difficult to see in this light ..
Now I am left with the headboard to make, which will be secured to the wall and not the beds. The wood will come from these ...
Laminations and curves are planned.
Regards from Perth
Derek
Recently I built two beds, which I have just got back to. Having completed them, I discovered that they were 40mm too long and too wide! Duh ... after many measurement checks!
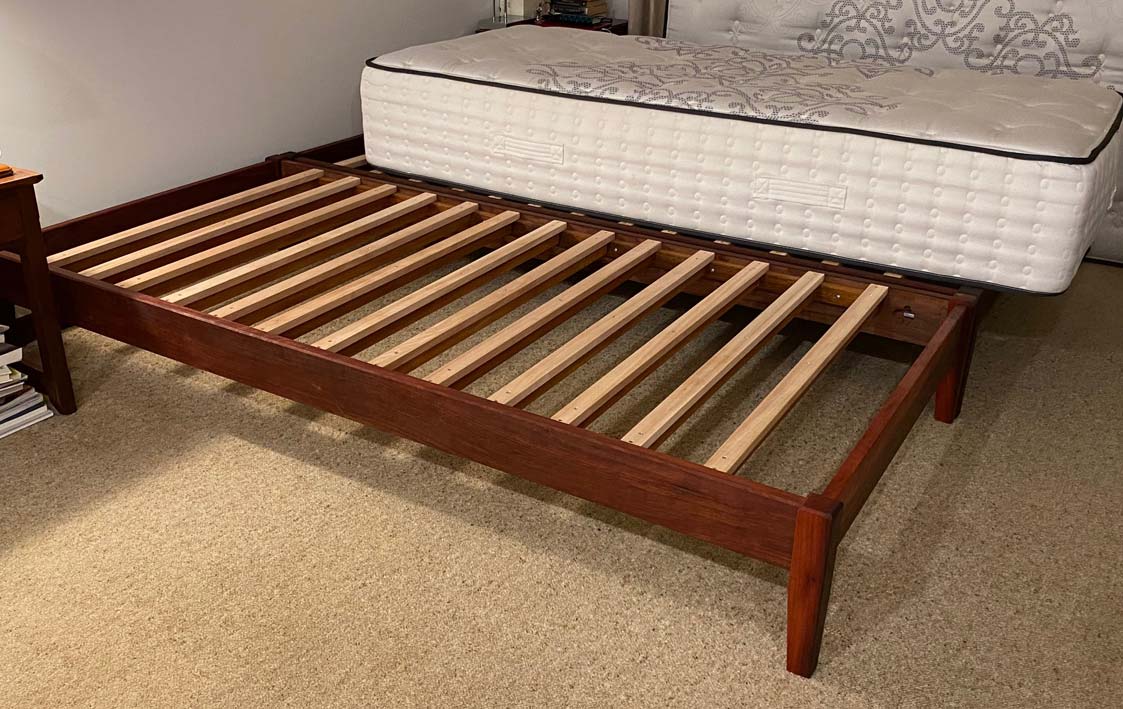
Obviously this meant pulling them apart and shortening the lengths and widths.
The head-and foot board leg joinery is loose mortice-and-tenon. 110mm long x 10mm wide. This was made fairly easy with a Domino machine. The loose tenons were sized on a jointer/thickness-planer, and then rounded over on a router table. All wood is Jarrah. The aim was for an exact fit.
I am really appreciating the extra bench top space afforded by the new MFT table (yes, the Veritas hold down, although it is sized for a 19mm dog hole works very well on a 20mm dog hole) ...
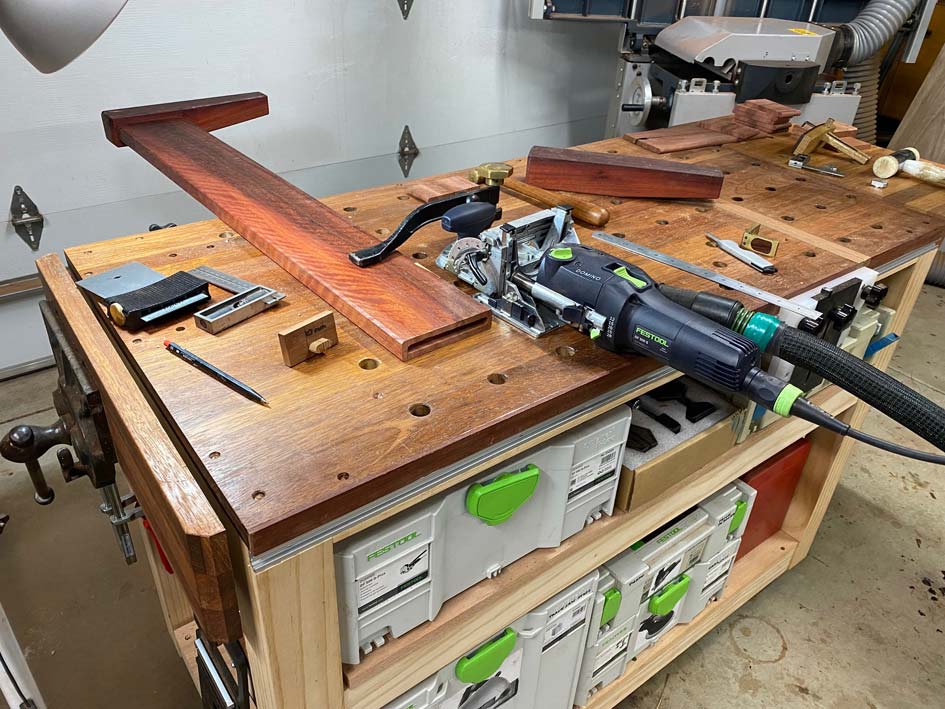
I made a small positioner to mark the centre of the domino, and plunged for the outer ends ...
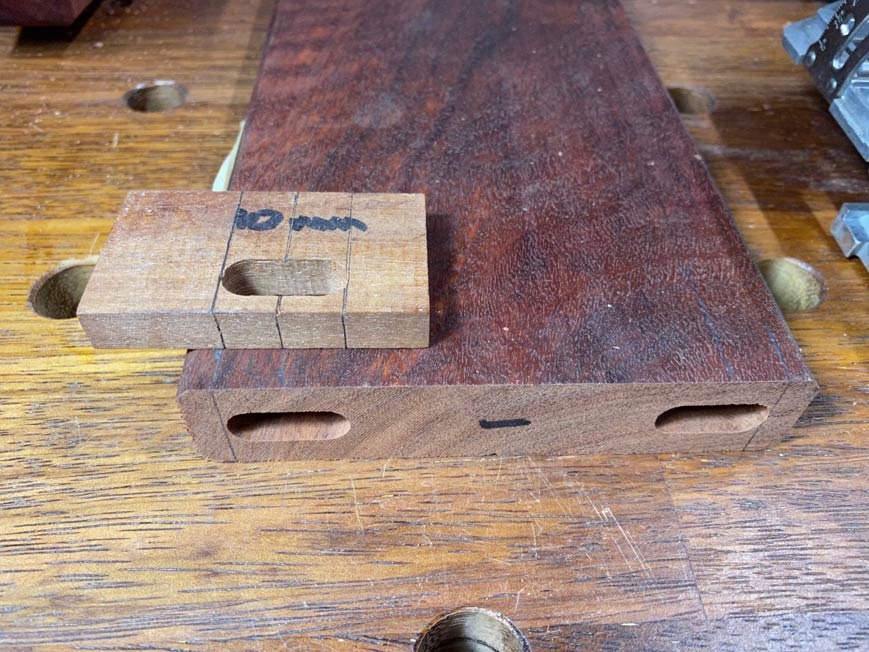
Then complete the mortice by nibbling away the centre section ..
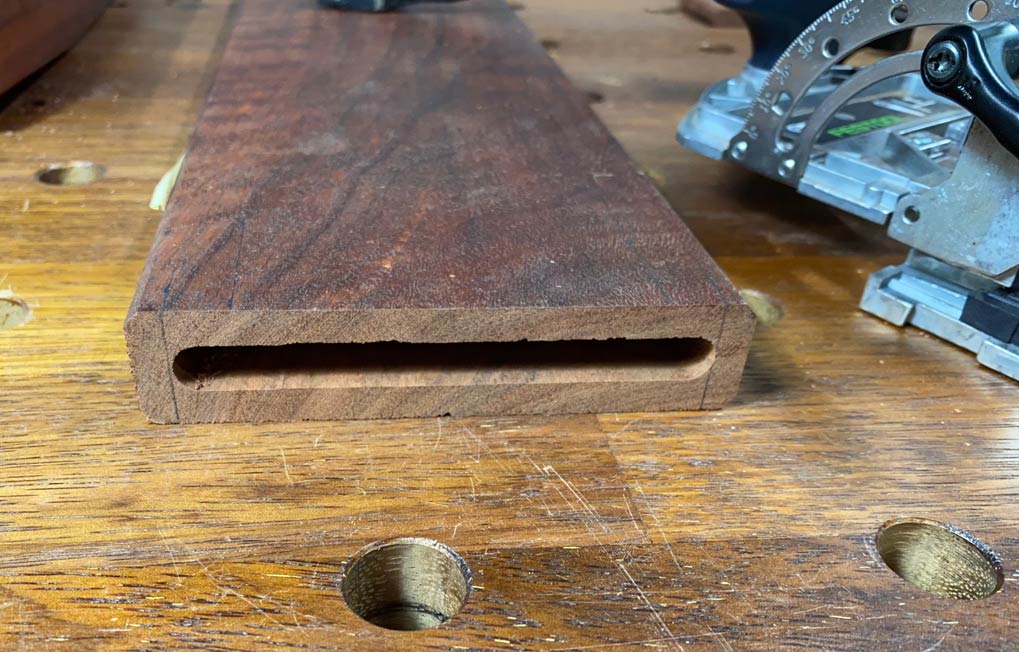
Tight fit in the rail ..
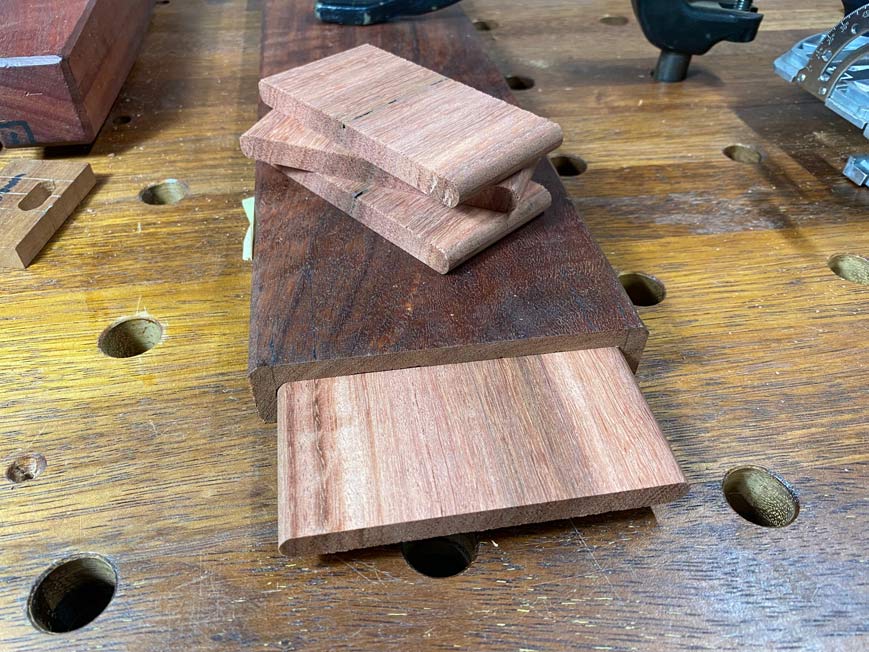
Tight fit in the post ..
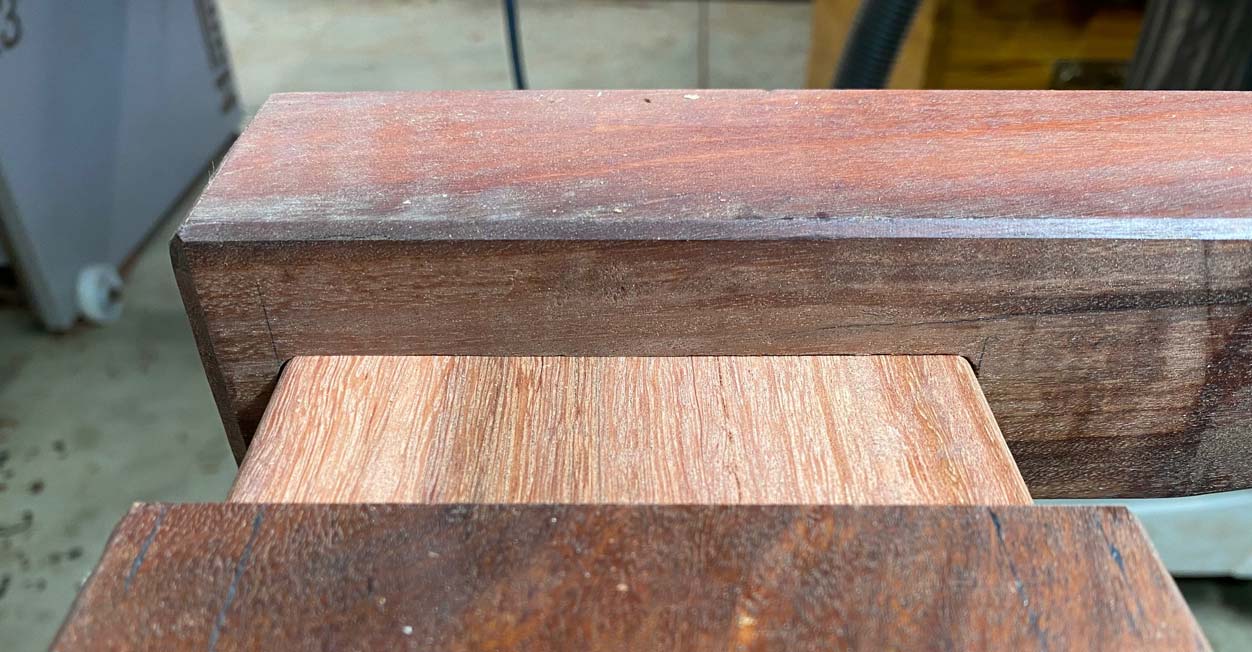
This was taken during the earlier build, and how the legs are once again ...
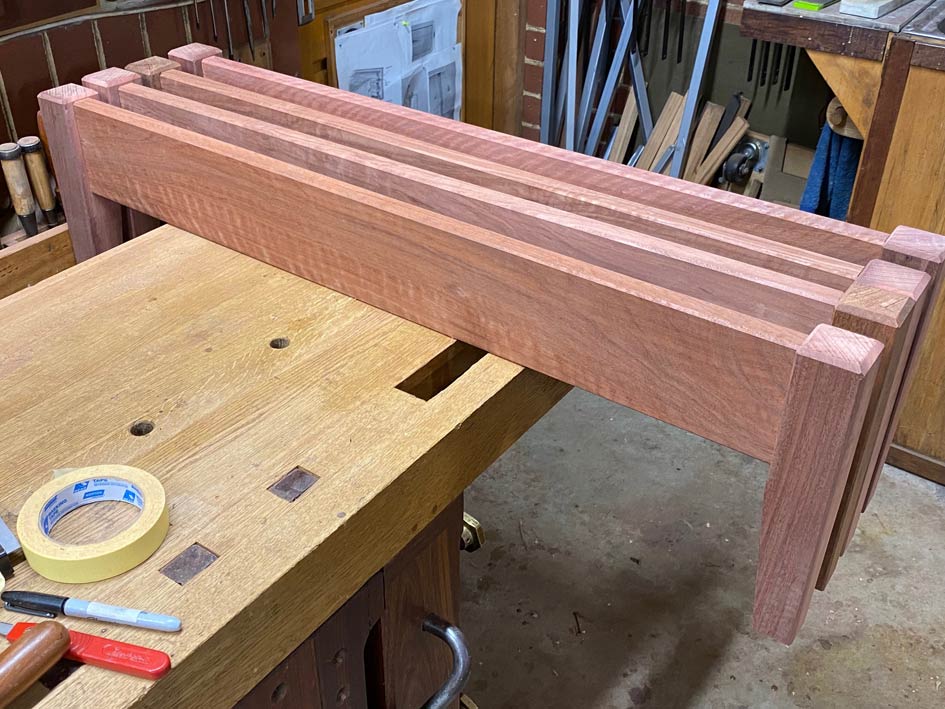
Part II: Construction
Rebuilding two single beds was a lot of work. To correct the oversizing, the beds were taken apart, and the rails shortened. Then the head- and foot boards were shortened, re-morticed, and re-glued. And finally, all the slats had to be shortened by 40mm, which was not a simple matter. More on this in a while.
About the beds and their design: One of the reasons I am posting the build details is that I hope it helps others in a similar position.
About 25 years ago I build a fantastic Jarrah King size double bed for my wife and myself. It was deliberately built 25mm over-width (which made it appear even wider) ...
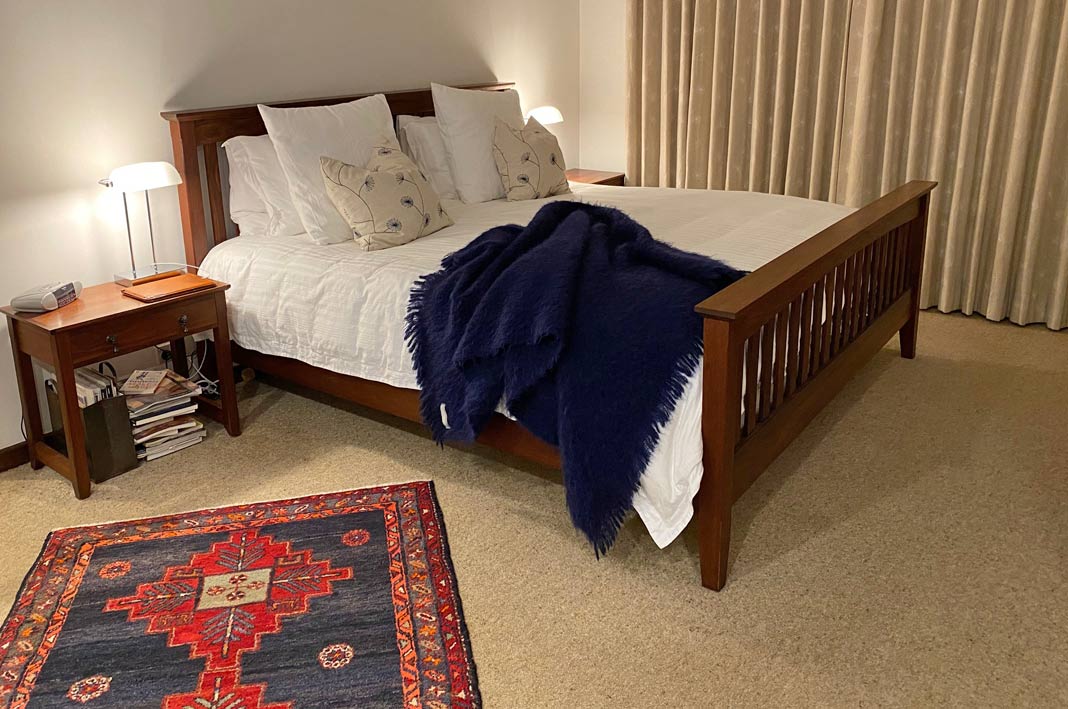
The reason for this is my wife is an incredibly light sleeper, especially since our son was born 3 decades ago, and will wake up if I even roll over in bed. We spent a small fortune on mattresses ... all those special ones which promised to smother any vibration. Well, all I can say is that I am lucky I was not smothered in my sleep! The solution for a while was the King size bed with two single mattresses, pushed together, but able to be pulled apart by 25mm if I was restless in sleep. The issue with a single bed is that vibration is transmitted by the bed frame. Consequently, I decided to build two beds which would actually become a double bed, but able to be separated if needed. I will explain this in a while.
As mentioned, these beds are done. Now I have a new headboard to build, which is for another time.
My wife stipulated no tail board for the beds as they make is far more work when making up a bed. My preference was for clean lines, which meant that I did not want visible bed bolts. Bed bolts are used, but they are hidden.
Here is the start of re-assembling the beds ..
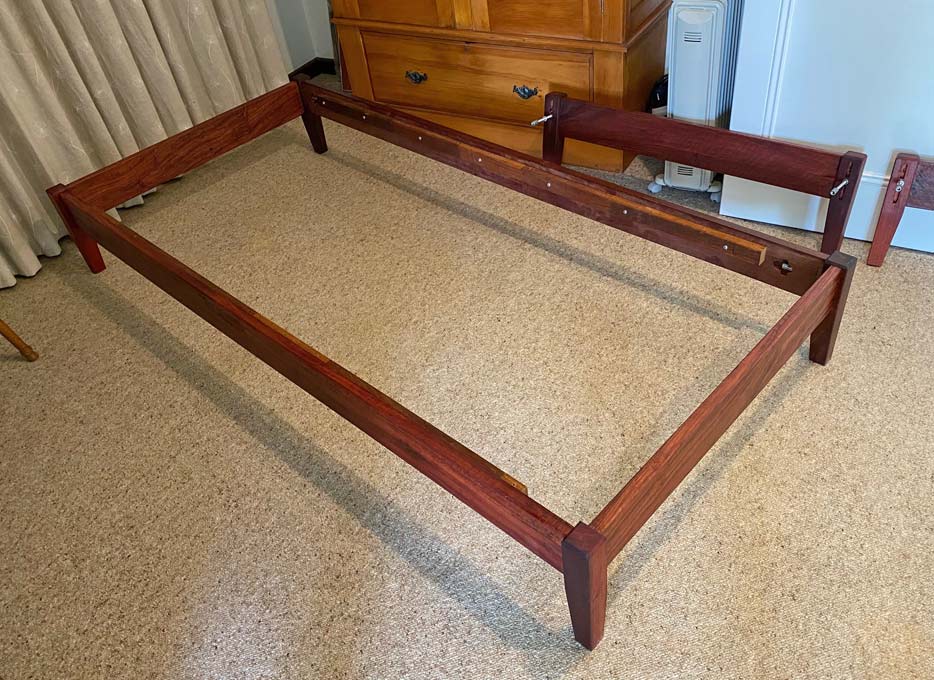
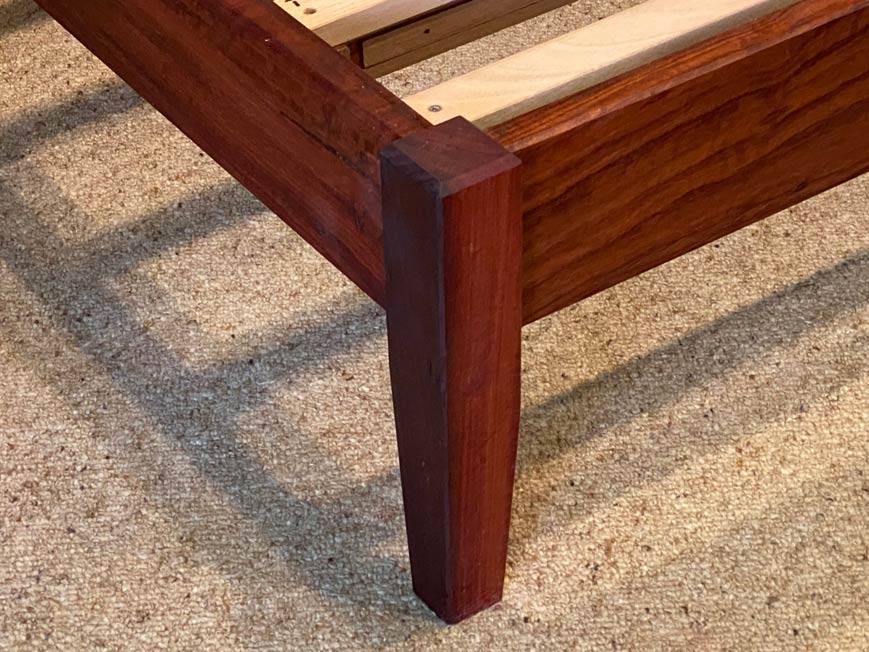
The head and tail ends are constructed with a mortice-and-tenon (this was the post made recently on morticing with a Domino). The side railed are connected with hidden bed bolts.
Here are the side rail connections. When the rails were shortened, so the bolts in these rails needed to be ..
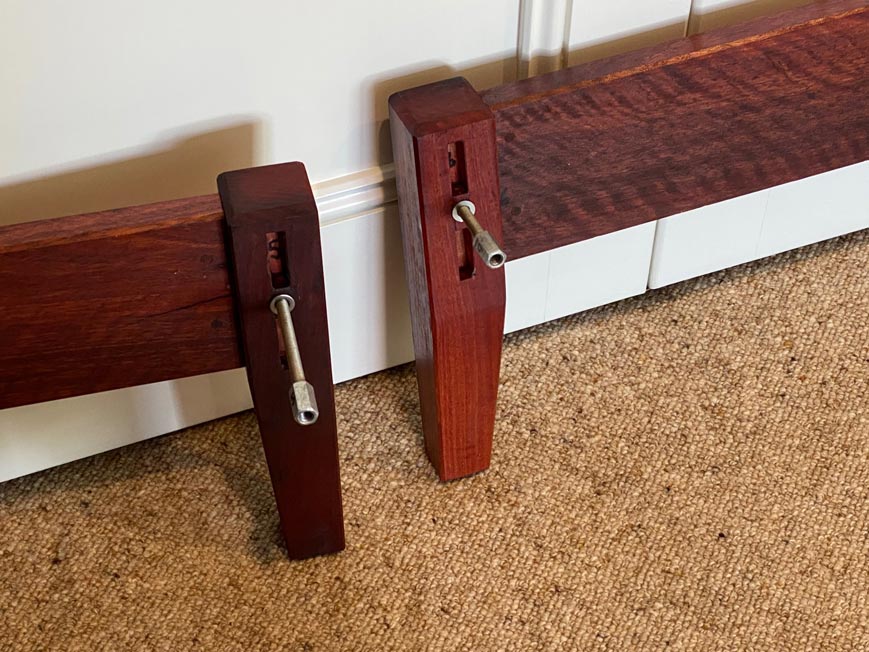
The bolts are fixed into inserted metal threads in the posts permanently with Loctite. The post and rail are locked with double loose mortice-and-tenons (no glue) and then bolted in the rail ...
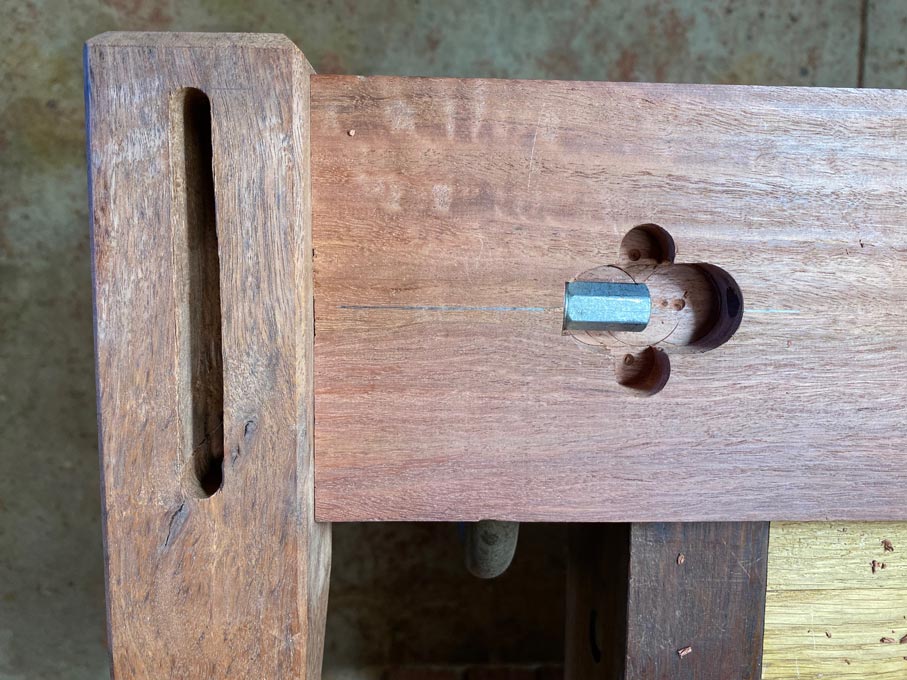
The slats for the beds are made in two parts ...
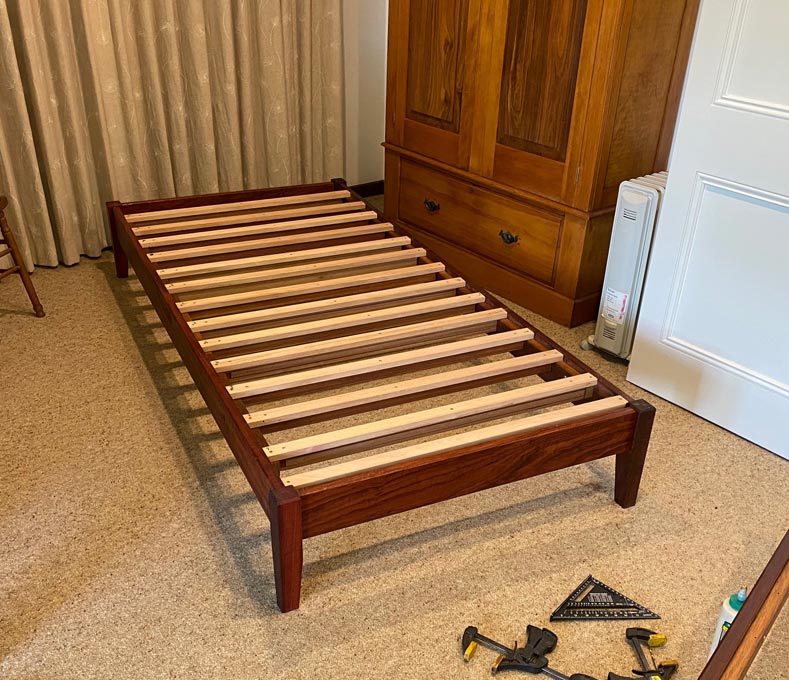
They are a T-section, which makes for a very rigid structure ...
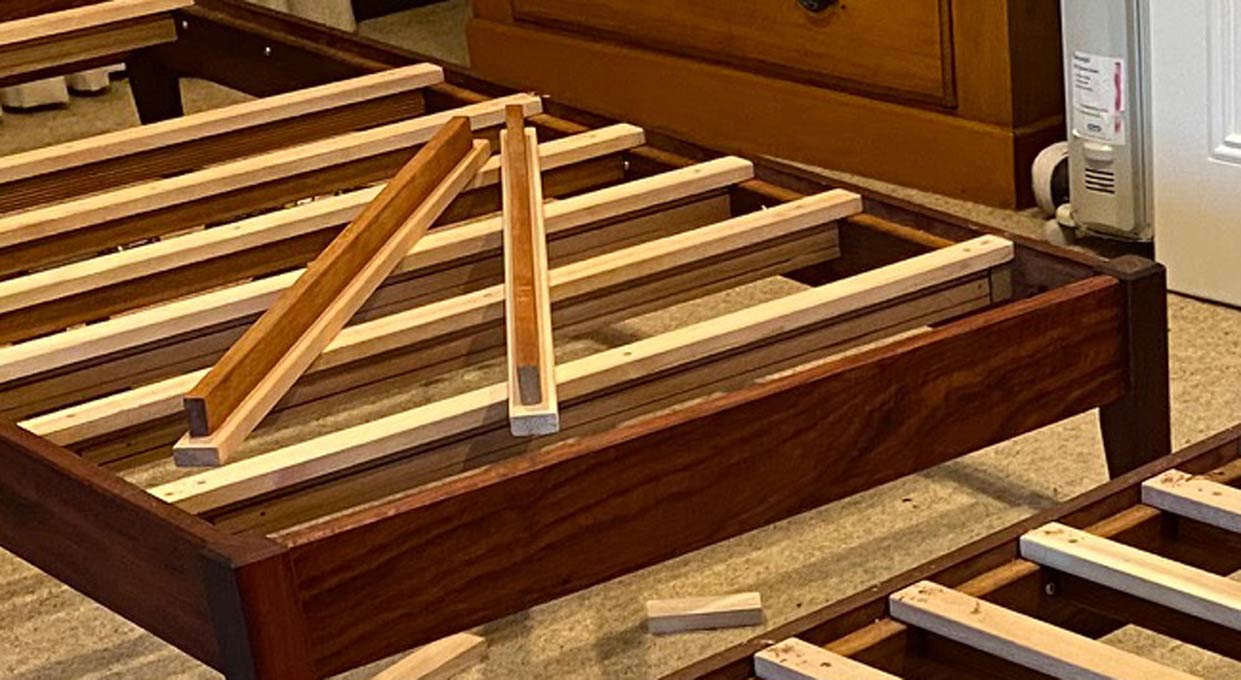
... and screwed down for extra strength.
Now the secret to making a double bed out of two singles lies with the rails. The slats on the outer sides are lower by 6mm (1/4") to aid in preventing the mattress slipping off the base, but also low enough to make it easier to tuck in sheets, etc.
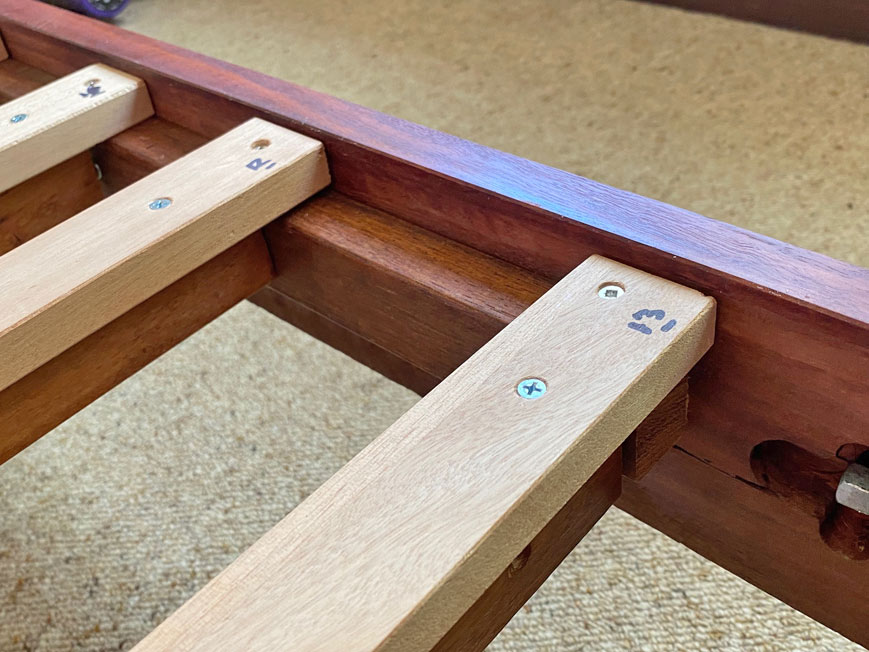
The slats on the inside rails are flush with the top ...
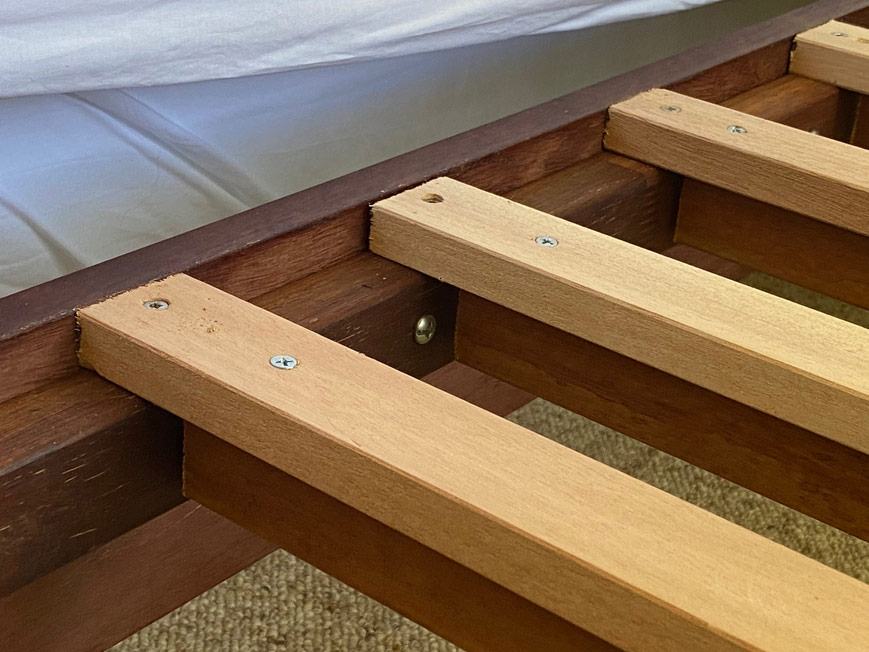
... enabling two mattresses to be placed alongside one another. Conversely, it is easy to pull them apart.
The Jarrah is finished in hard wax oil, and the result is quite stunning. Difficult to see in this light ..
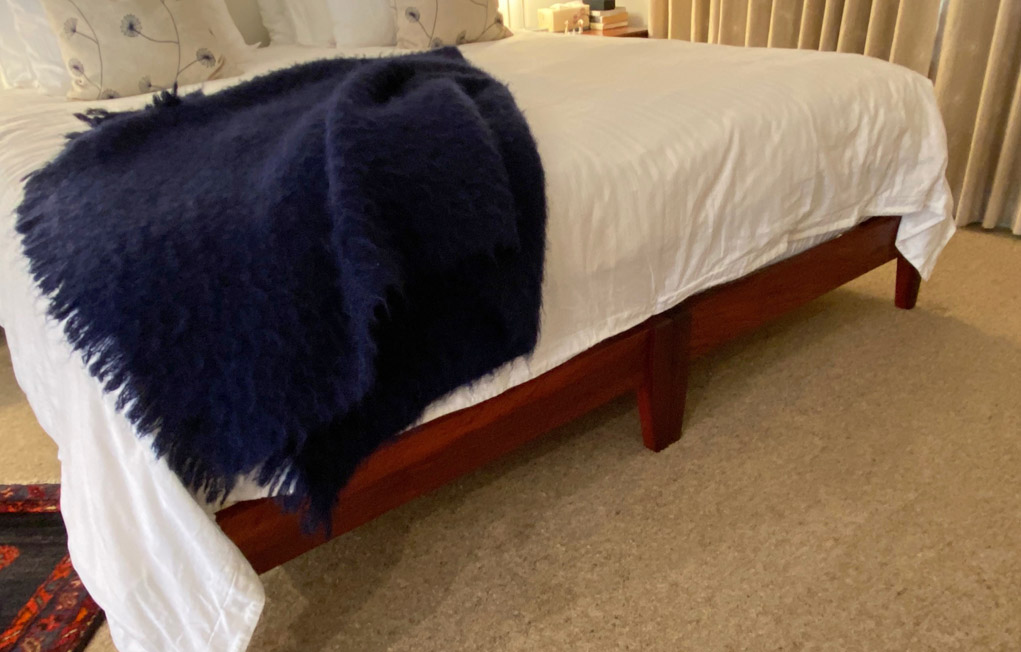
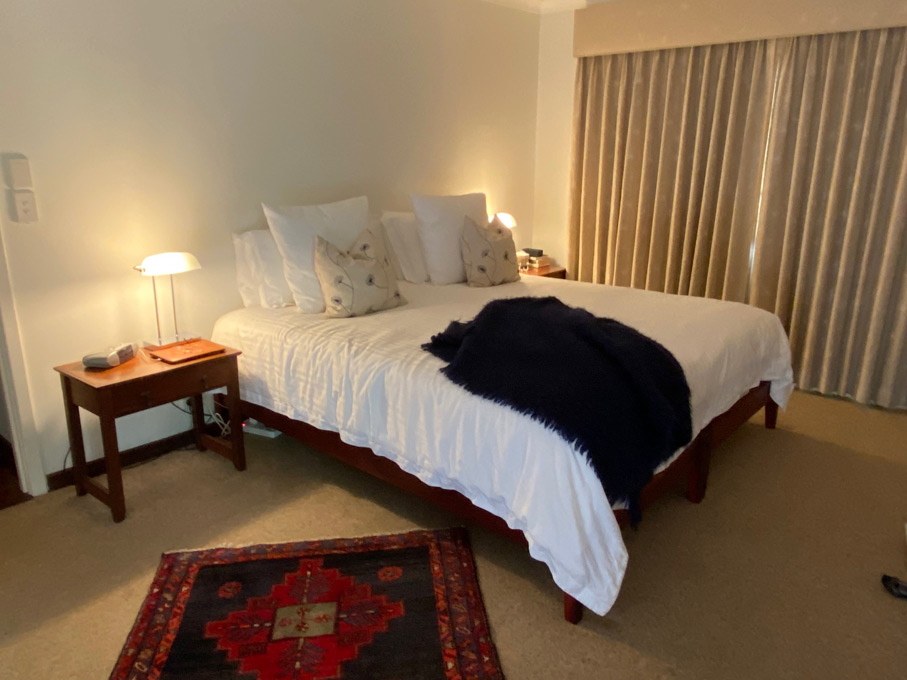
Now I am left with the headboard to make, which will be secured to the wall and not the beds. The wood will come from these ...
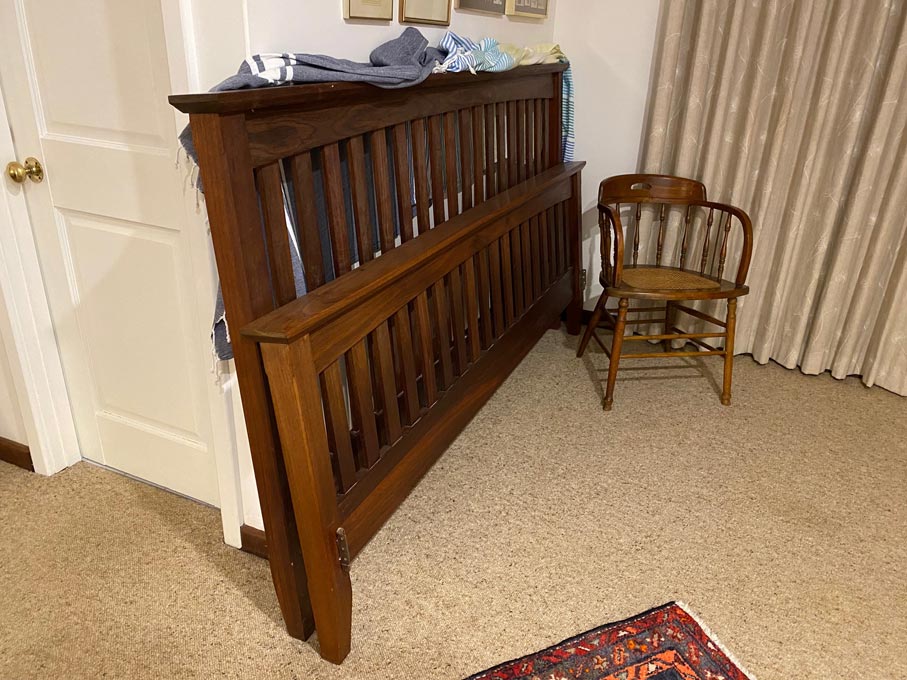
Laminations and curves are planned.
Regards from Perth
Derek
Last edited: