MikeG.
Established Member
I did some gardening this morning, but got bored. Back to the workshop! The next item on the agenda is a bathroom cabinet to sit on the flat shelf created by the stairwell. A couple of manky bits of contiboard cover the space at the moment:
I pondered for hours and then drew up an in depth design in 3D with cutting list and every joint illustrated:
When I took the old stairs out of the house 5 or so years ago, I set the parana pine aside knowing I'd use it one day. I've worked my way through it, but this is what is left:
Looks great, hey?
It took quite a while getting all the steel out of it:
And any that got broken off got marked:
Now, the basic idea is to do a rustic thing and wash it over with a watery paint that I'll rub straight off. I wanted to show sawn faces, not planed, so after much experimenting with spacers and different saws, I set about "kerfing" the boards in pairs:
It was such a fiddle, and exhausting, that I quickly realised it wasn't going to work. Time for a change of plan. I decided to scrub plane the boards, and leave those marks in:
My number 6 has my most cambered iron, so that's the one I used. The paint was a really nasty obstacle, and I took to using an unrestored saw as a toother scraper to break up the worst of it. Mask on, as this is obviously lead paint (the stairs date from the 50s or 60s). I soon swapped to doing one board at a time, rather than two, and after a couple of hours I had all the stock done:
You can just about see the diagonal tool marks if you look carefully. That is my final surface. Hopefully the undulations will pick up the light nicely when it in situ.
Setting out the necessary angle for the face of the cabinet, which is like a corner cupboard. Precisely like a corner cupboard, because that's what this is:
I then started ripping:
The offcut was then flipped over to make the desired angle. All edges were planed of course:
I ripped some more to produce some 70mm and some 50mm bits, and marked up the shoulders:
Having decided on a 10mm tenon I marked up:
Then cut the shoulders:
Then chiseled off the cheeks, using Mike's Rule of Halves:
Now, the thing is, the narrower boards are also thinner, by quite a lot. This isn't going to cause too many issues, but when setting out the joints I should really have worked it out on the thinner stock, not the thicker stuff. There's not much meat left around this mortise:
Fearing breaking out the sidewall whilst chopping the mortise, I took an unusual approach. I have a saw with about 10TPI, rip cut, which is perfect for cutting along the grain in these situations:
The rest was hacking out the waste with a 1/4" chisel then carefully paring. Very much NOT my normal approach to a mortise:
That's 3.6mm. Probably just slightly less than ideal........
Anyway, the joints worked out OK:
.......despite the differing timber thicknesses:
I'd never normally chisel in the vice, but with an angled face behind, I had no choice:
I just had time to glue up the frame before coming in to cook:
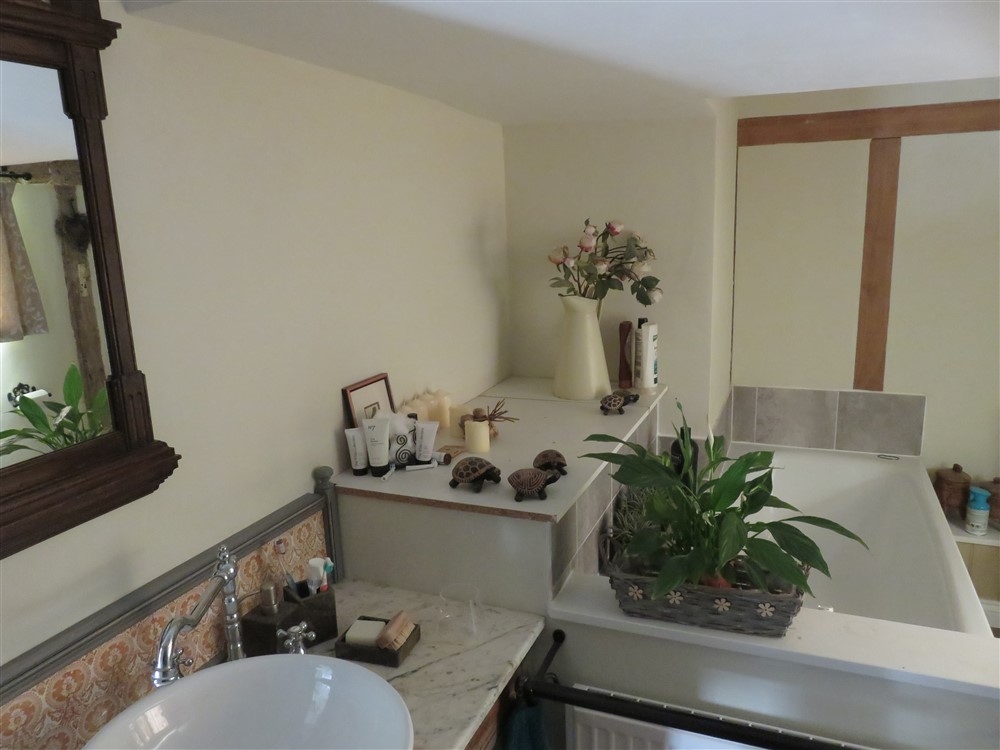
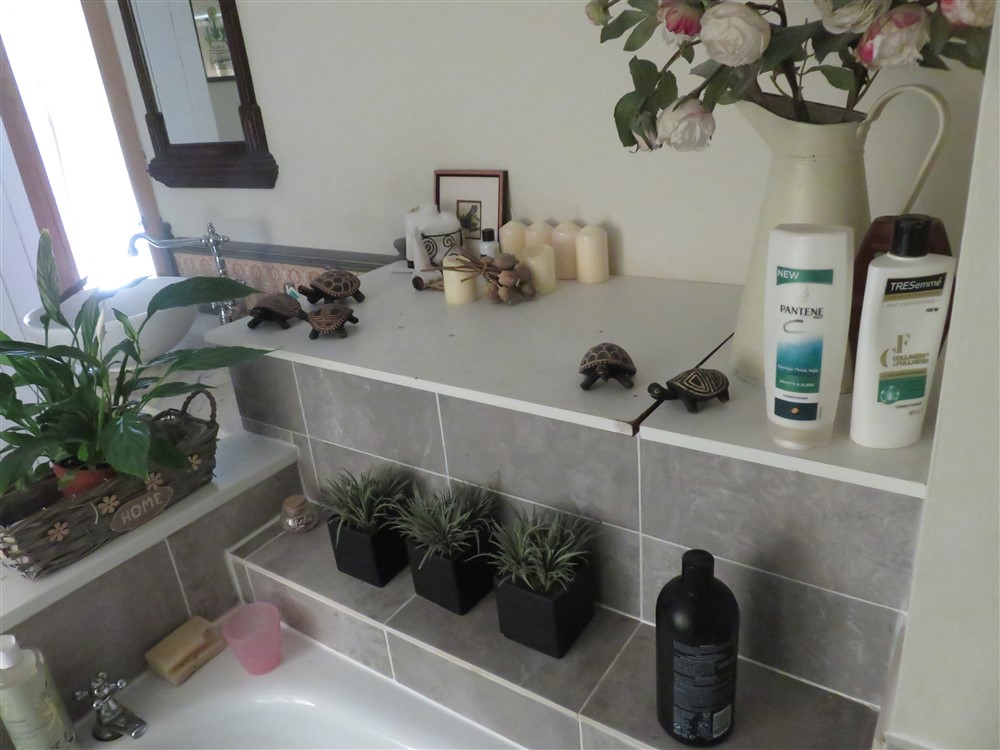
I pondered for hours and then drew up an in depth design in 3D with cutting list and every joint illustrated:
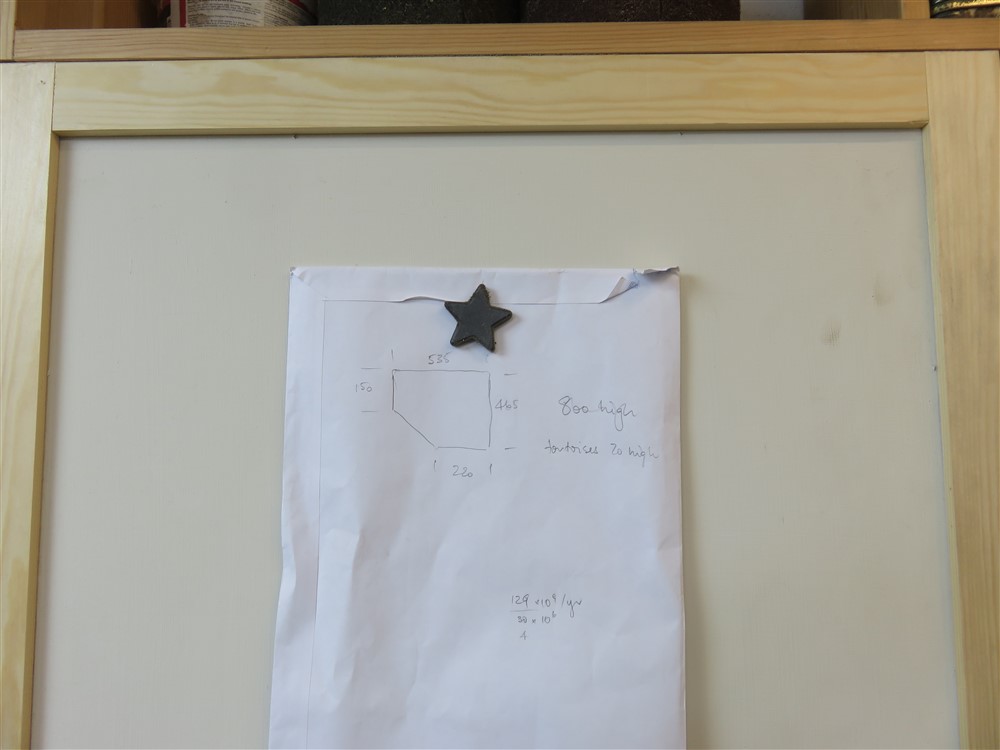
When I took the old stairs out of the house 5 or so years ago, I set the parana pine aside knowing I'd use it one day. I've worked my way through it, but this is what is left:
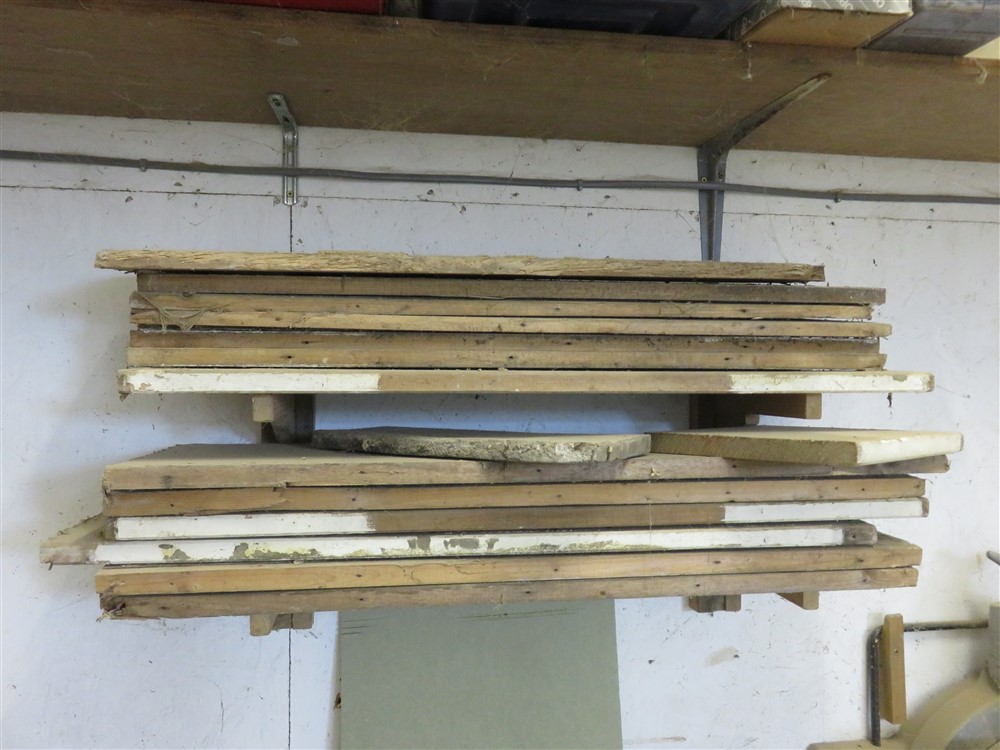
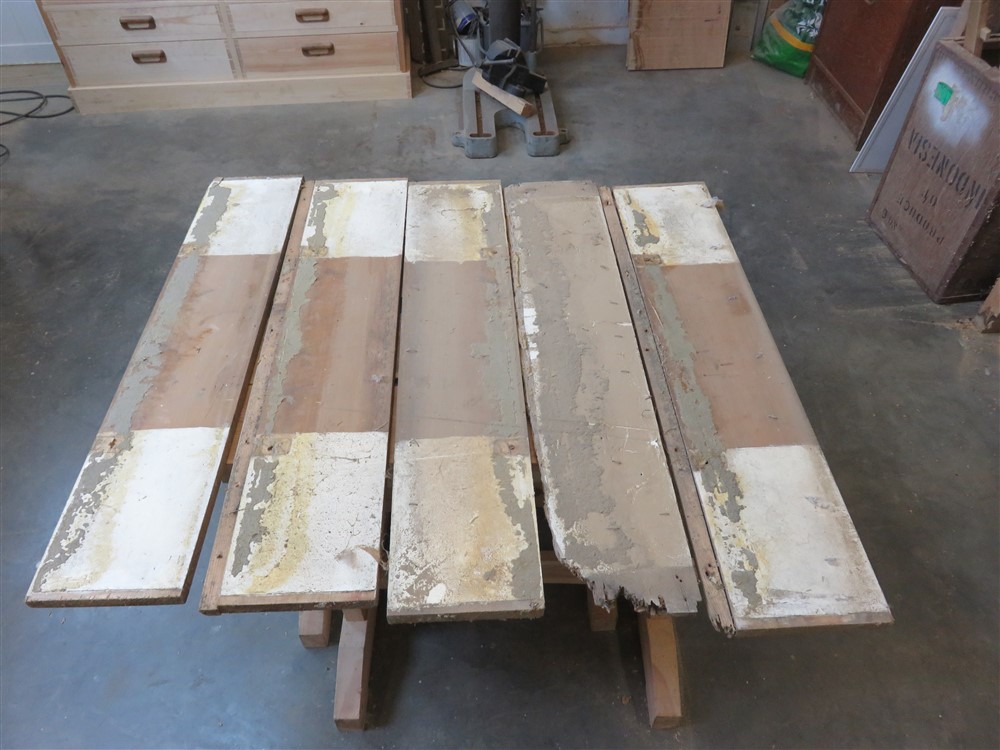
Looks great, hey?
It took quite a while getting all the steel out of it:
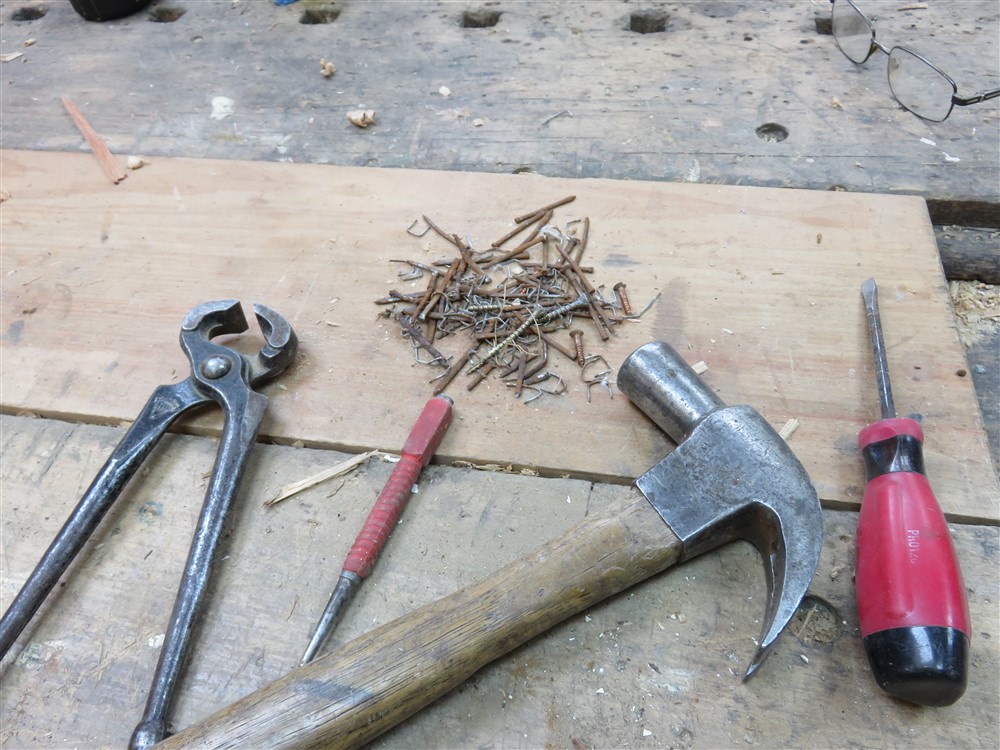
And any that got broken off got marked:
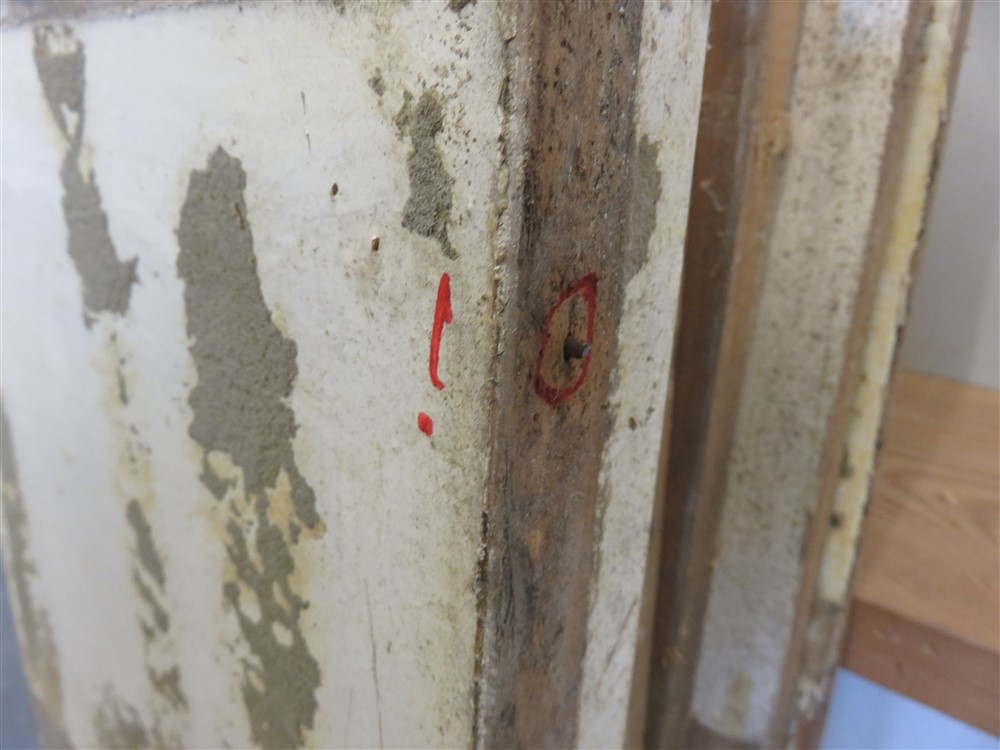
Now, the basic idea is to do a rustic thing and wash it over with a watery paint that I'll rub straight off. I wanted to show sawn faces, not planed, so after much experimenting with spacers and different saws, I set about "kerfing" the boards in pairs:
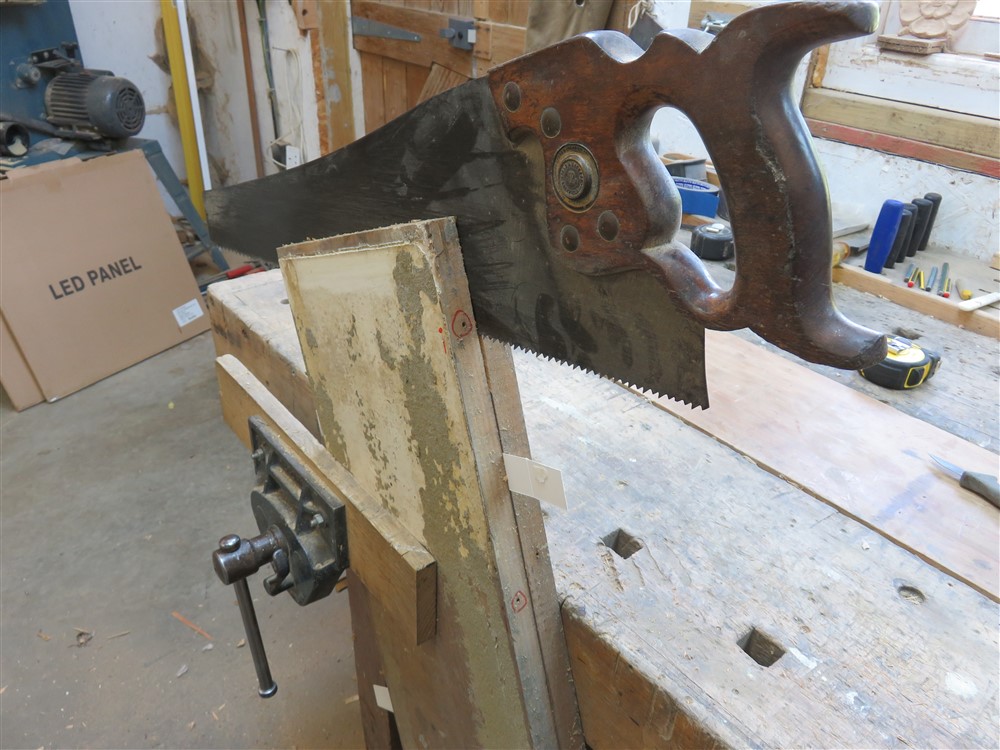
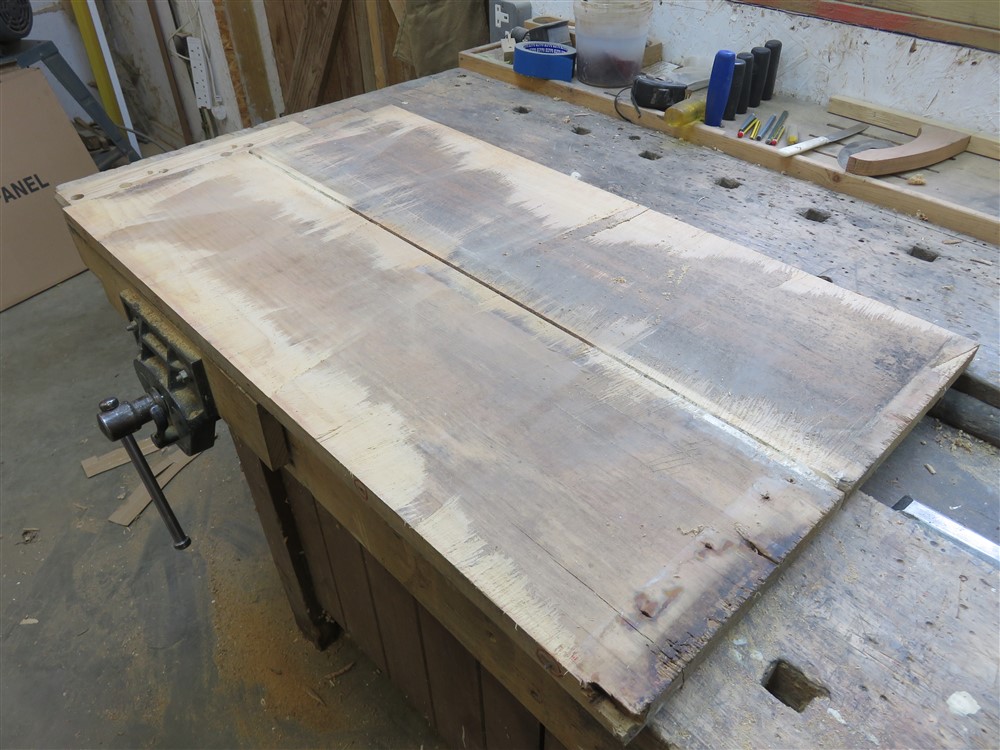
It was such a fiddle, and exhausting, that I quickly realised it wasn't going to work. Time for a change of plan. I decided to scrub plane the boards, and leave those marks in:
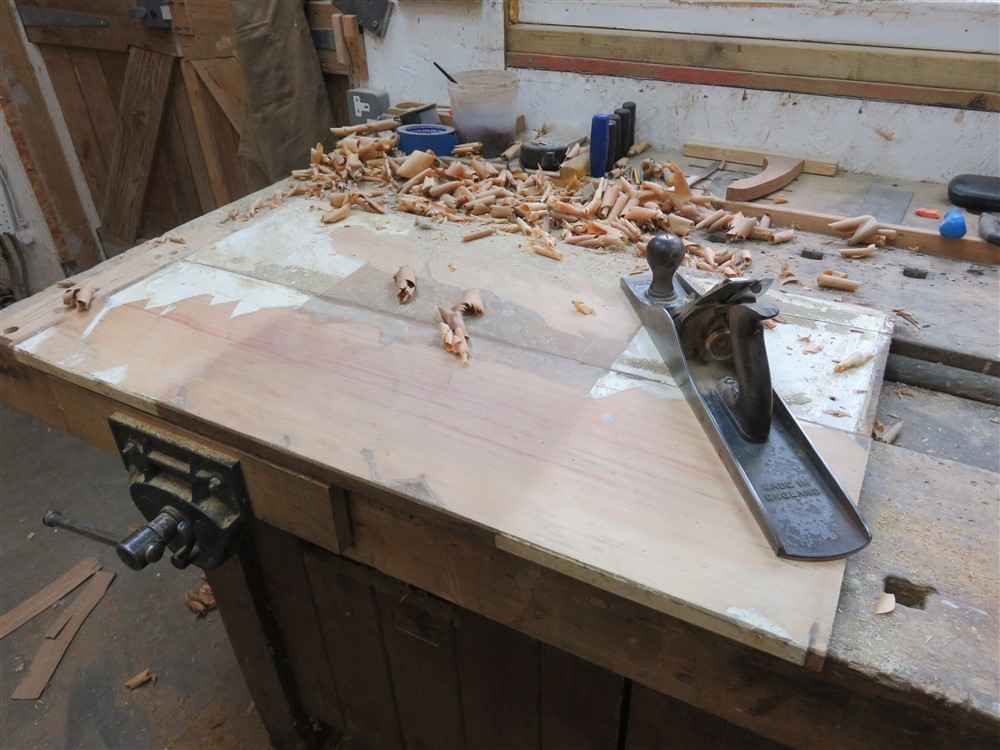
My number 6 has my most cambered iron, so that's the one I used. The paint was a really nasty obstacle, and I took to using an unrestored saw as a toother scraper to break up the worst of it. Mask on, as this is obviously lead paint (the stairs date from the 50s or 60s). I soon swapped to doing one board at a time, rather than two, and after a couple of hours I had all the stock done:
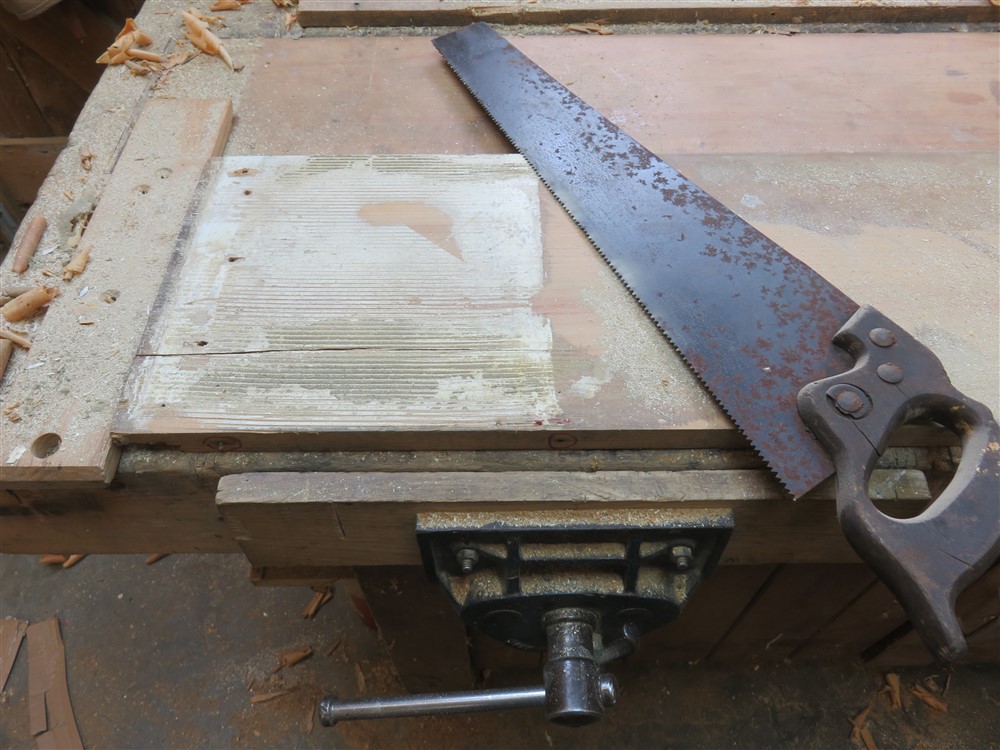
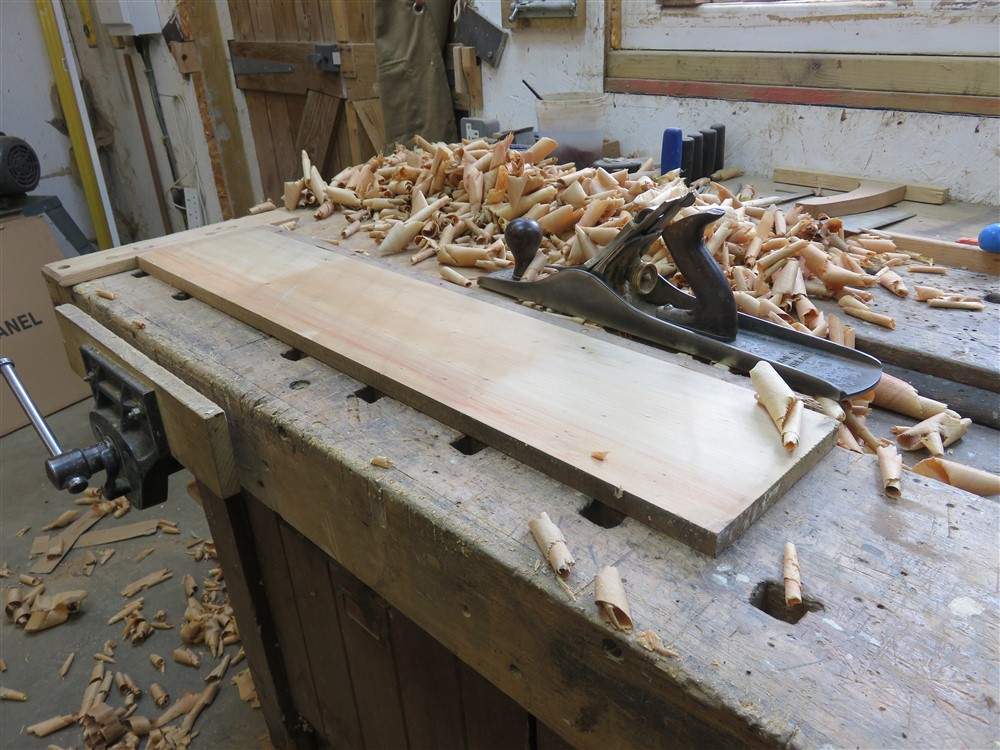
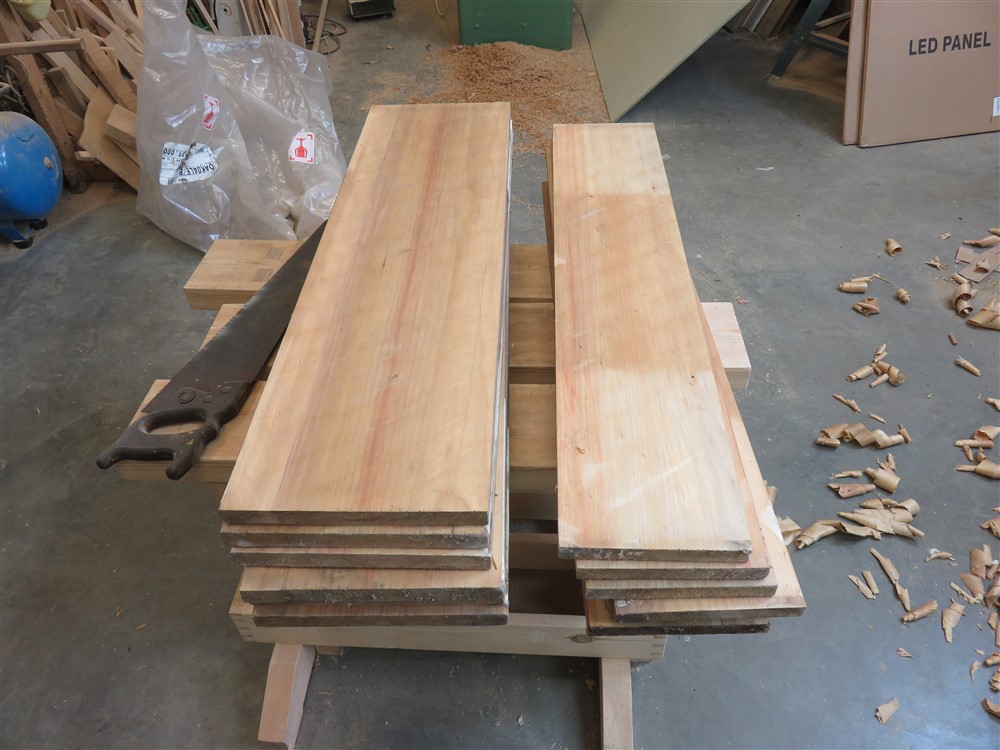
You can just about see the diagonal tool marks if you look carefully. That is my final surface. Hopefully the undulations will pick up the light nicely when it in situ.
Setting out the necessary angle for the face of the cabinet, which is like a corner cupboard. Precisely like a corner cupboard, because that's what this is:
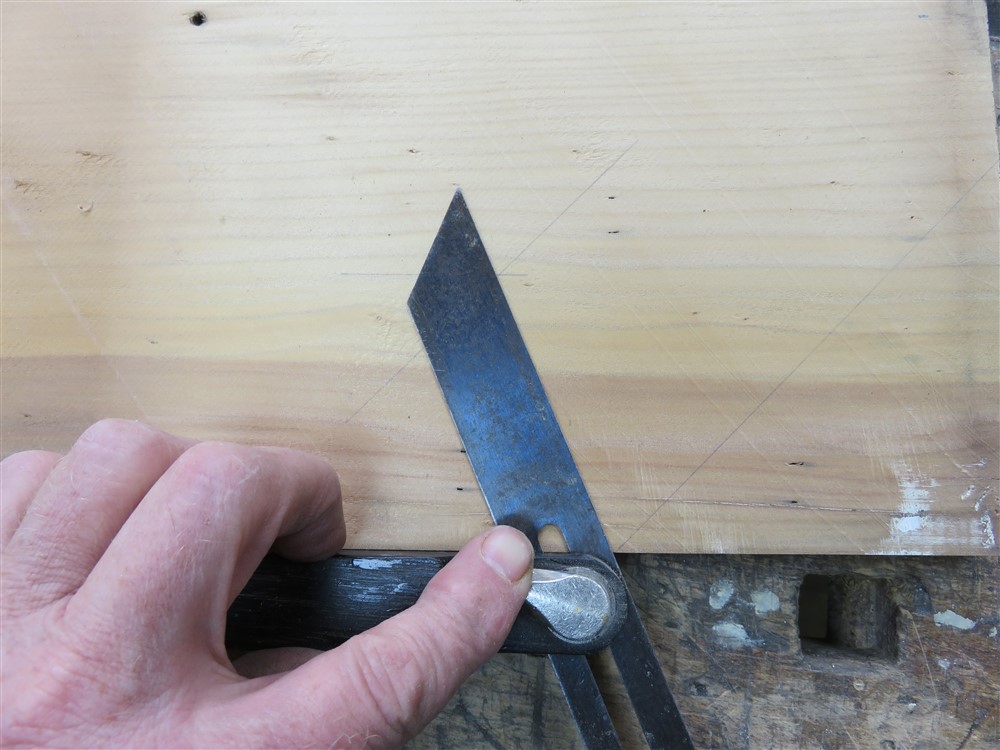
I then started ripping:
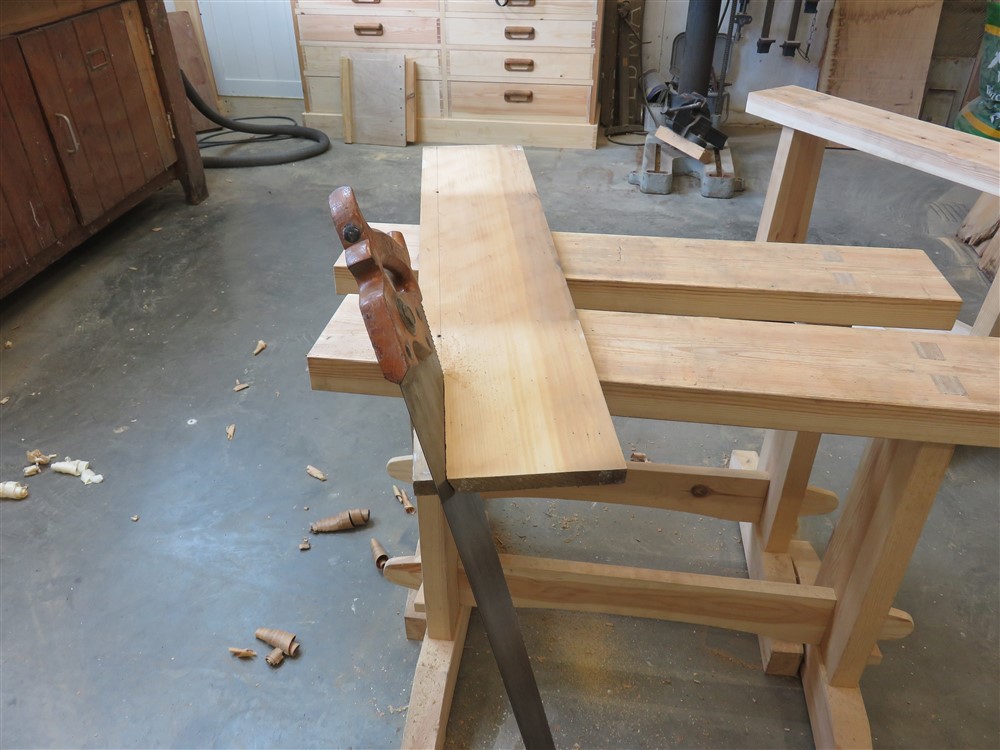
The offcut was then flipped over to make the desired angle. All edges were planed of course:
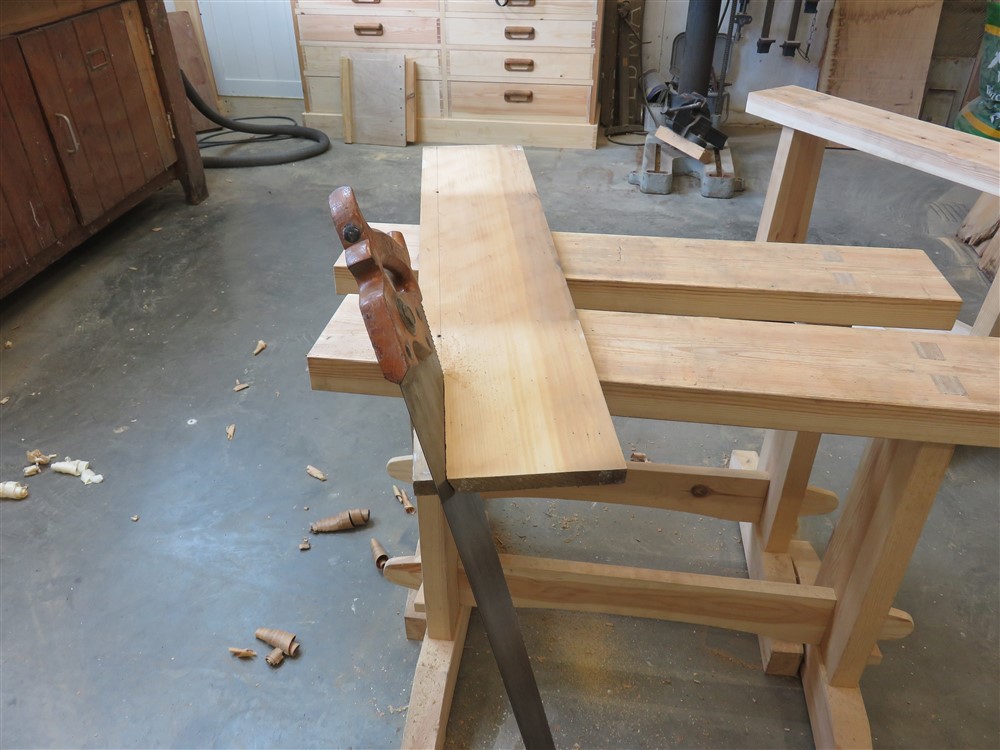
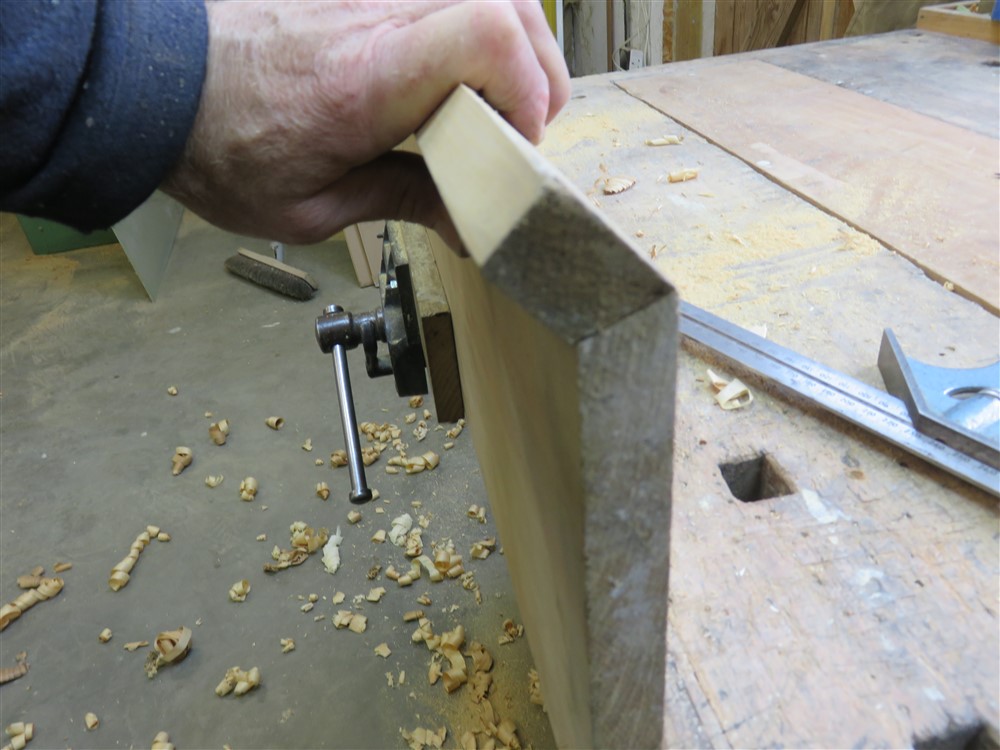
I ripped some more to produce some 70mm and some 50mm bits, and marked up the shoulders:
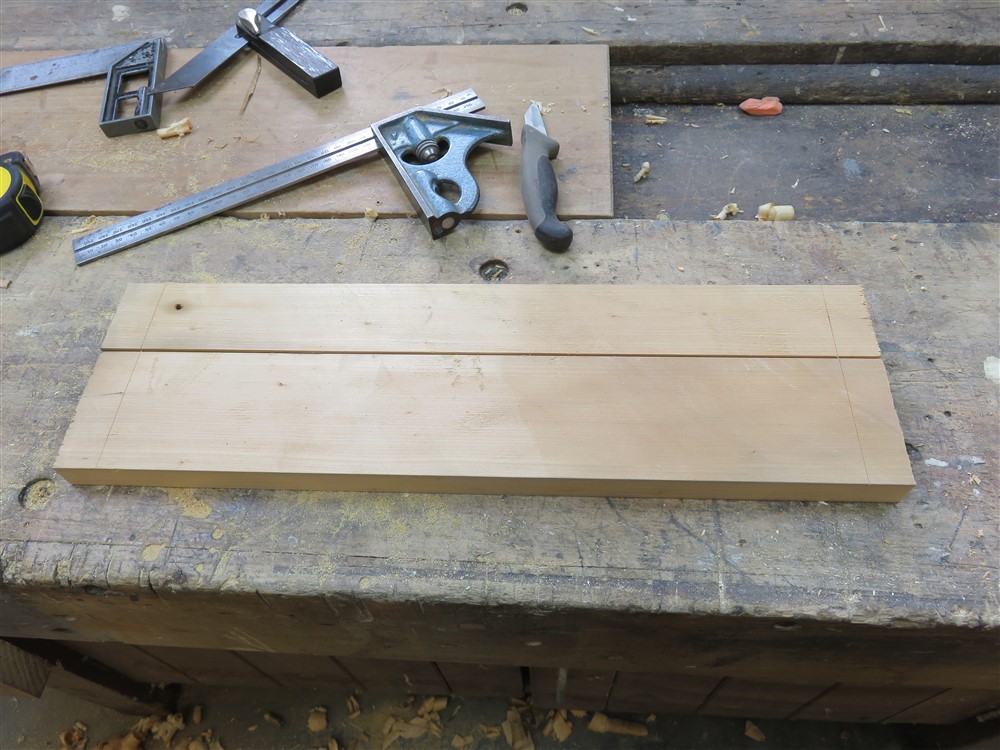
Having decided on a 10mm tenon I marked up:
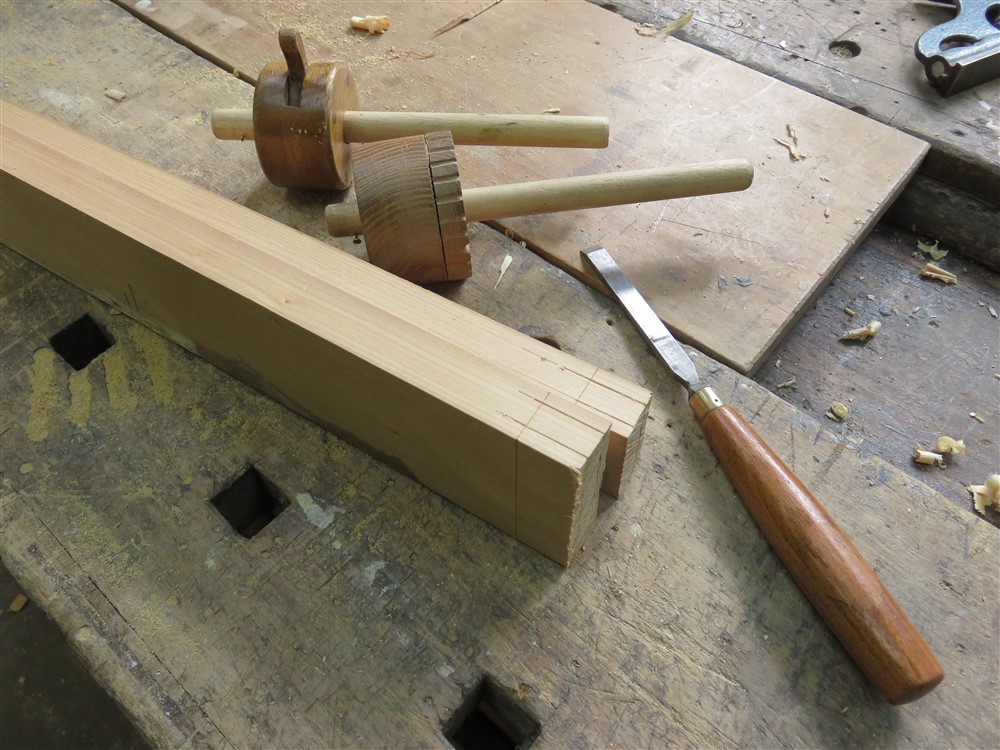
Then cut the shoulders:
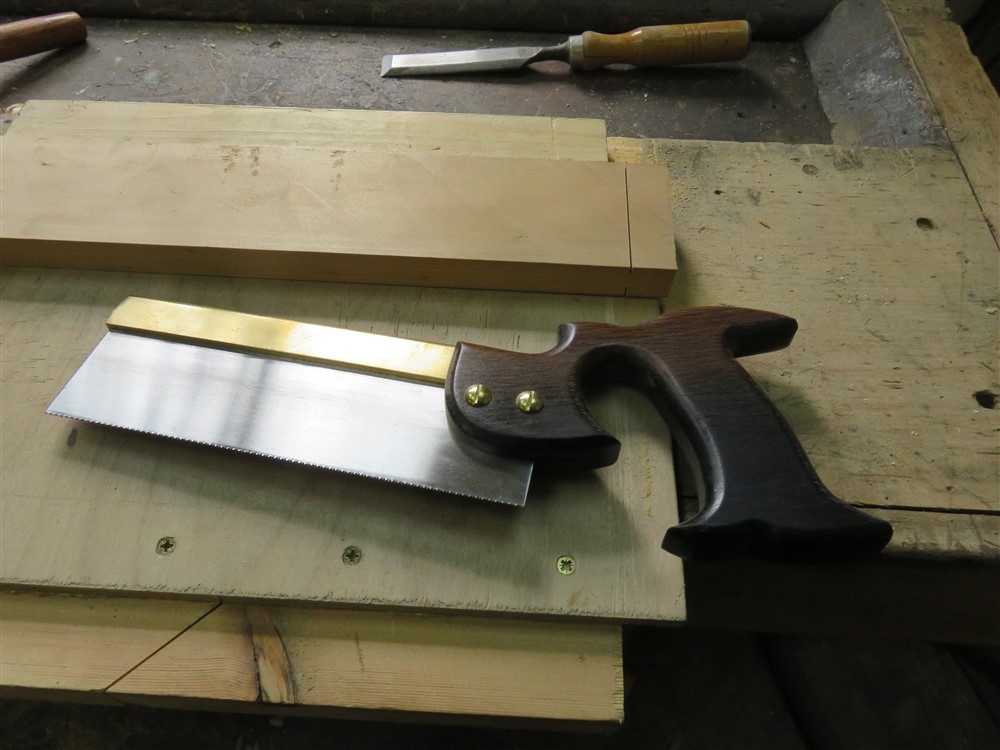
Then chiseled off the cheeks, using Mike's Rule of Halves:
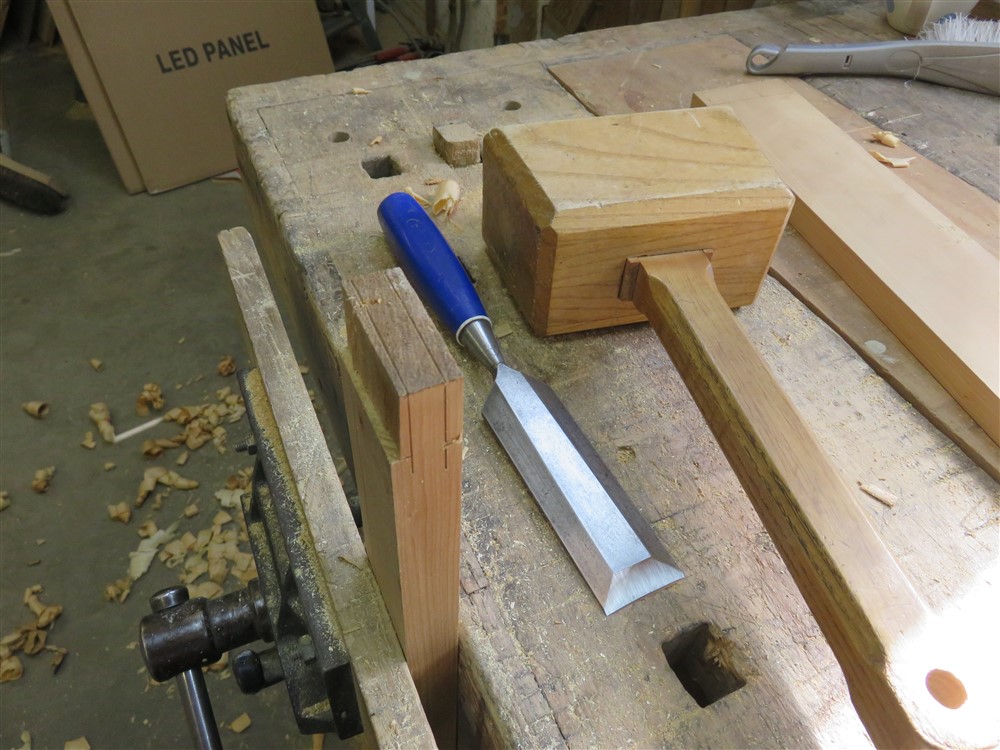
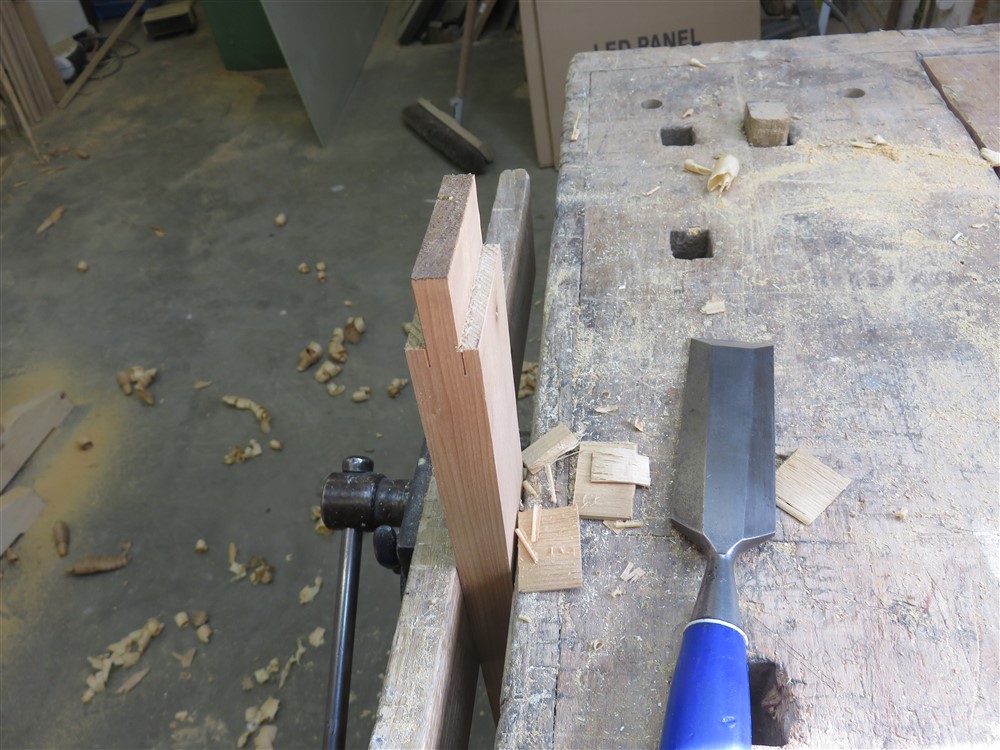
Now, the thing is, the narrower boards are also thinner, by quite a lot. This isn't going to cause too many issues, but when setting out the joints I should really have worked it out on the thinner stock, not the thicker stuff. There's not much meat left around this mortise:
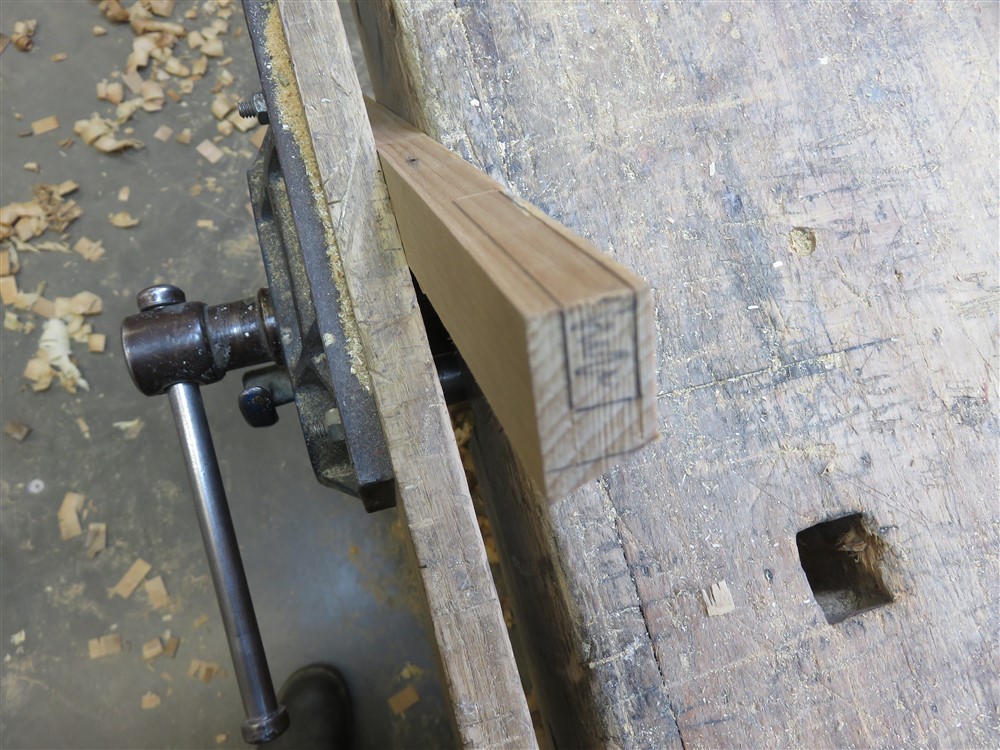
Fearing breaking out the sidewall whilst chopping the mortise, I took an unusual approach. I have a saw with about 10TPI, rip cut, which is perfect for cutting along the grain in these situations:
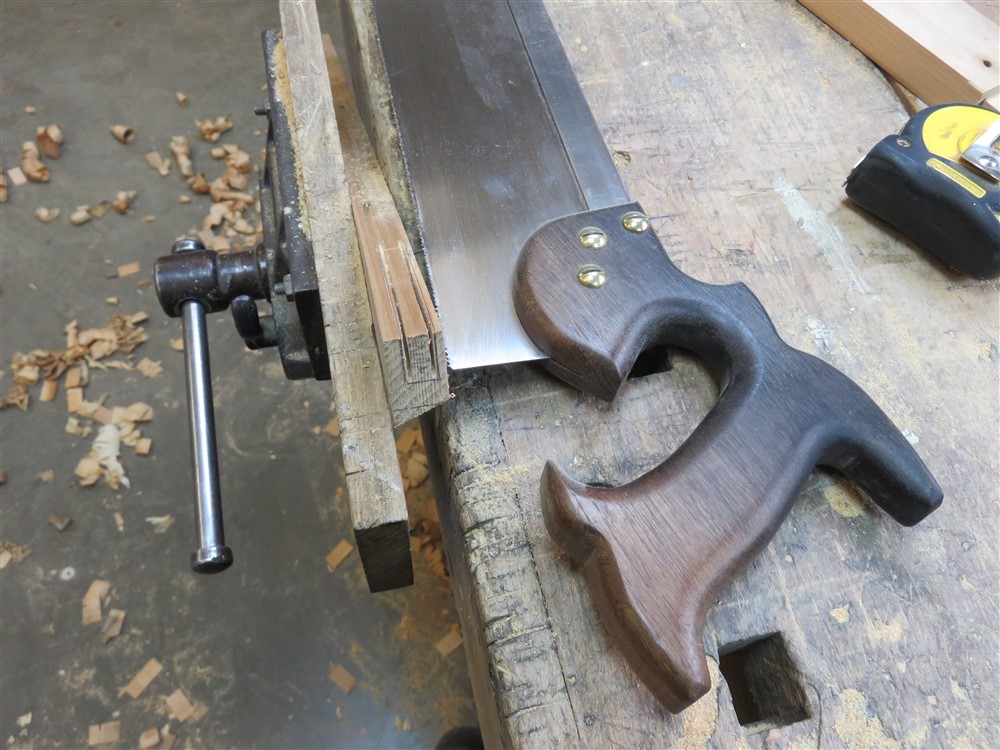
The rest was hacking out the waste with a 1/4" chisel then carefully paring. Very much NOT my normal approach to a mortise:
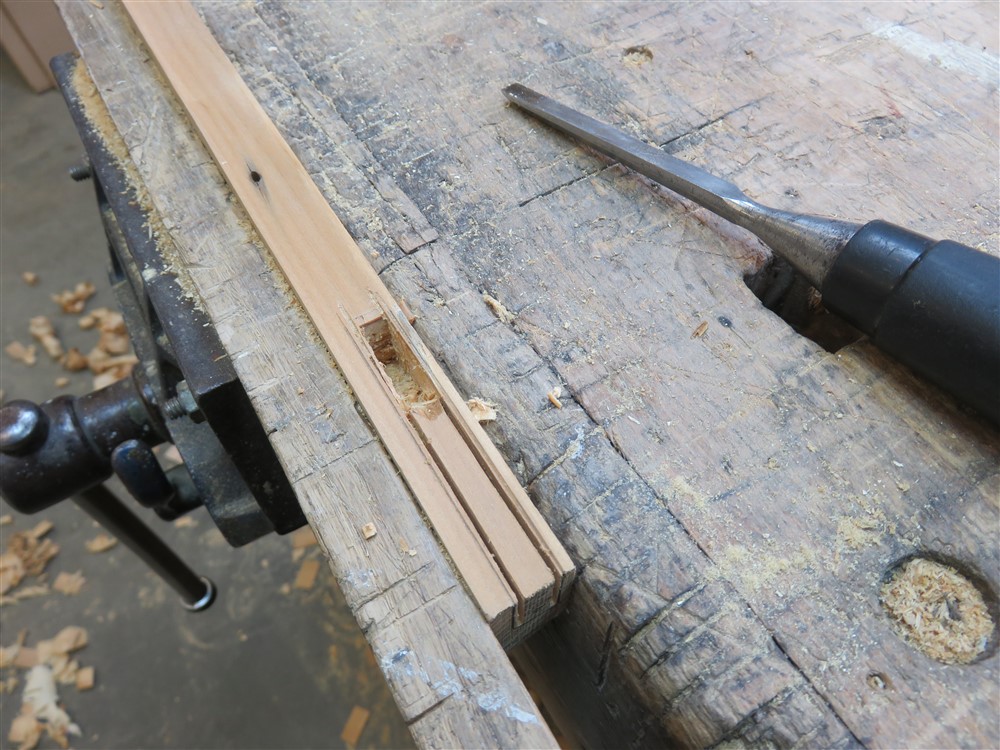
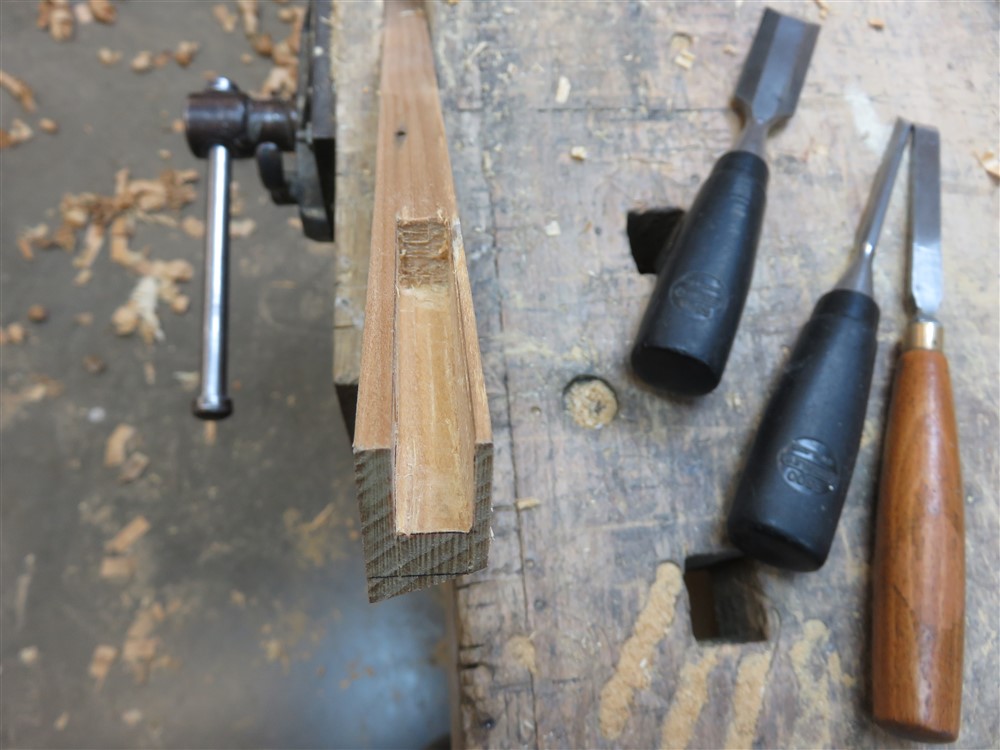
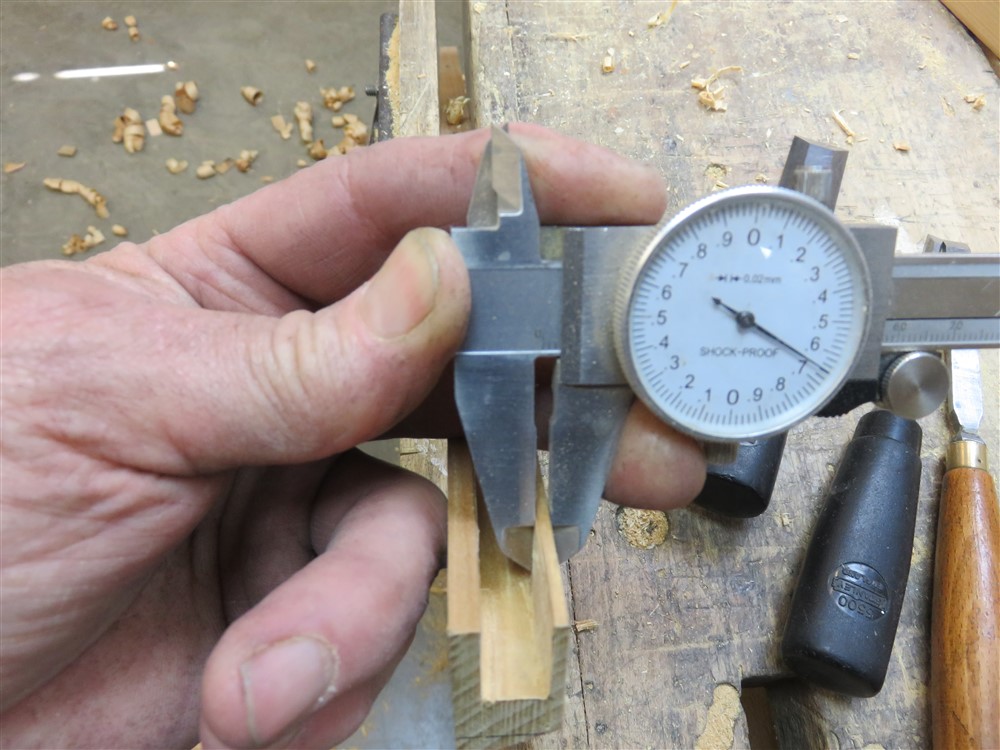
That's 3.6mm. Probably just slightly less than ideal........
Anyway, the joints worked out OK:
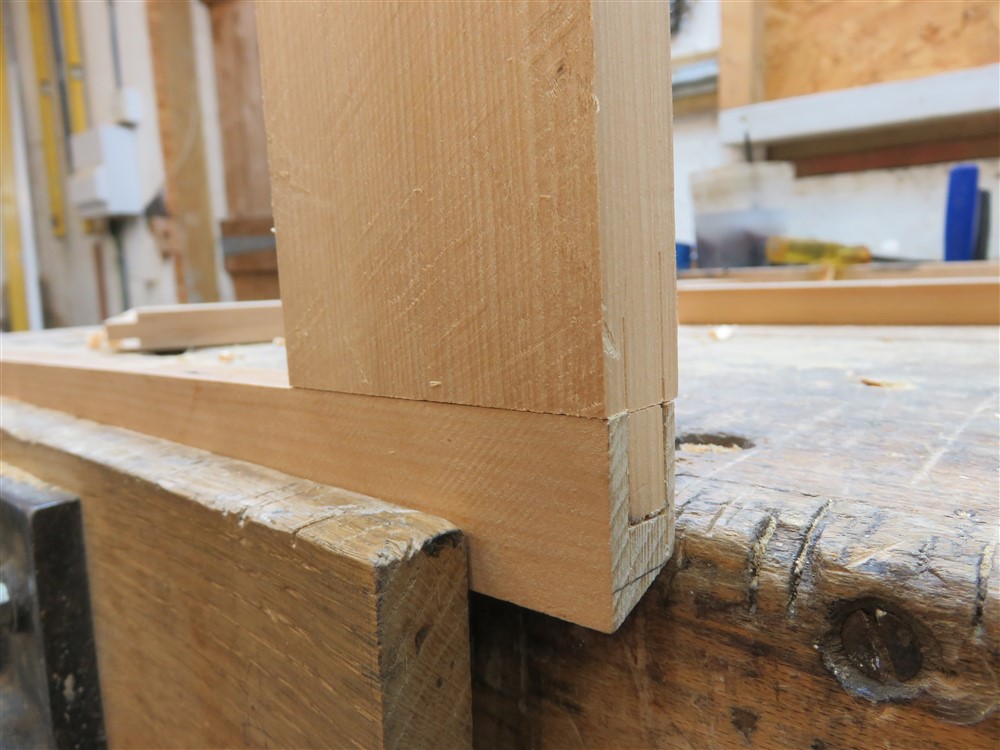
.......despite the differing timber thicknesses:
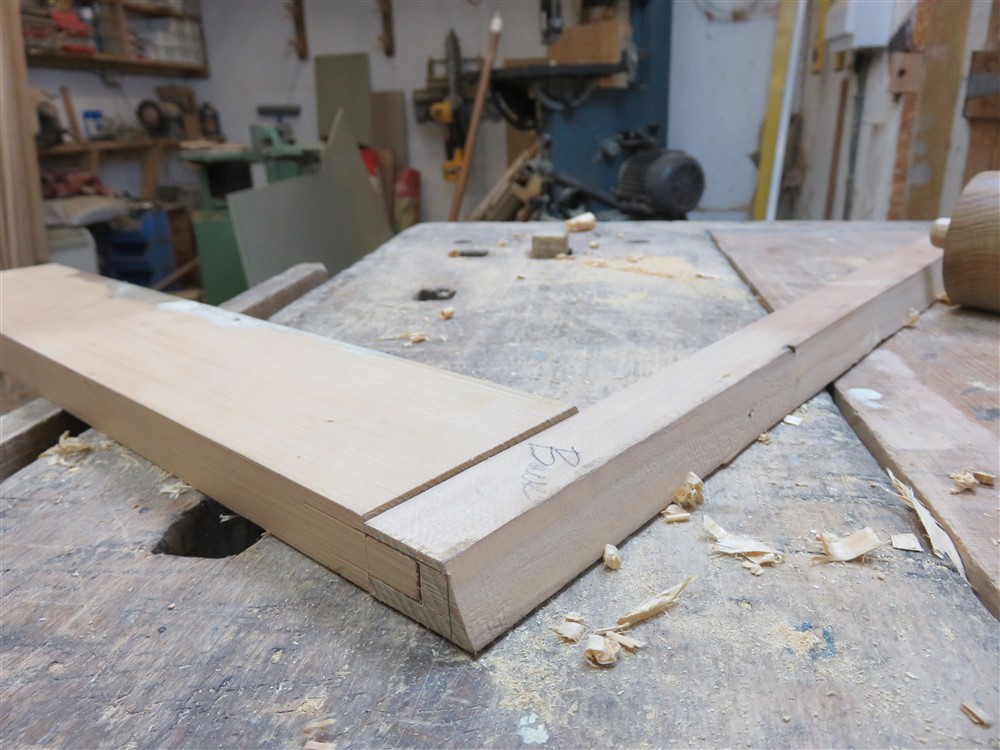
I'd never normally chisel in the vice, but with an angled face behind, I had no choice:
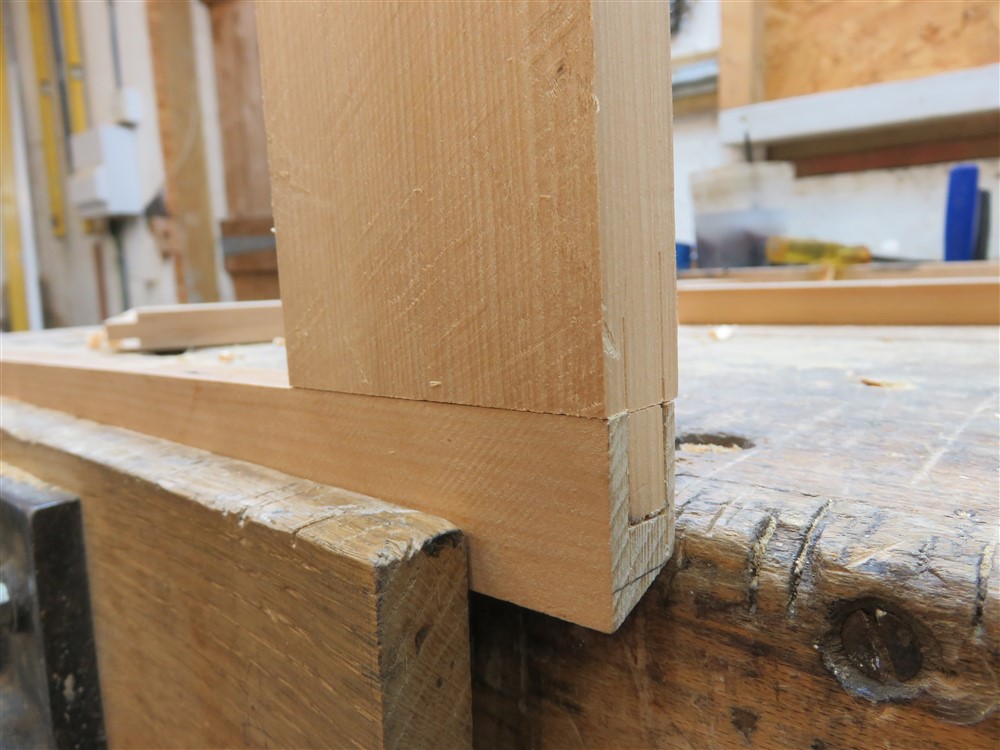
I just had time to glue up the frame before coming in to cook:
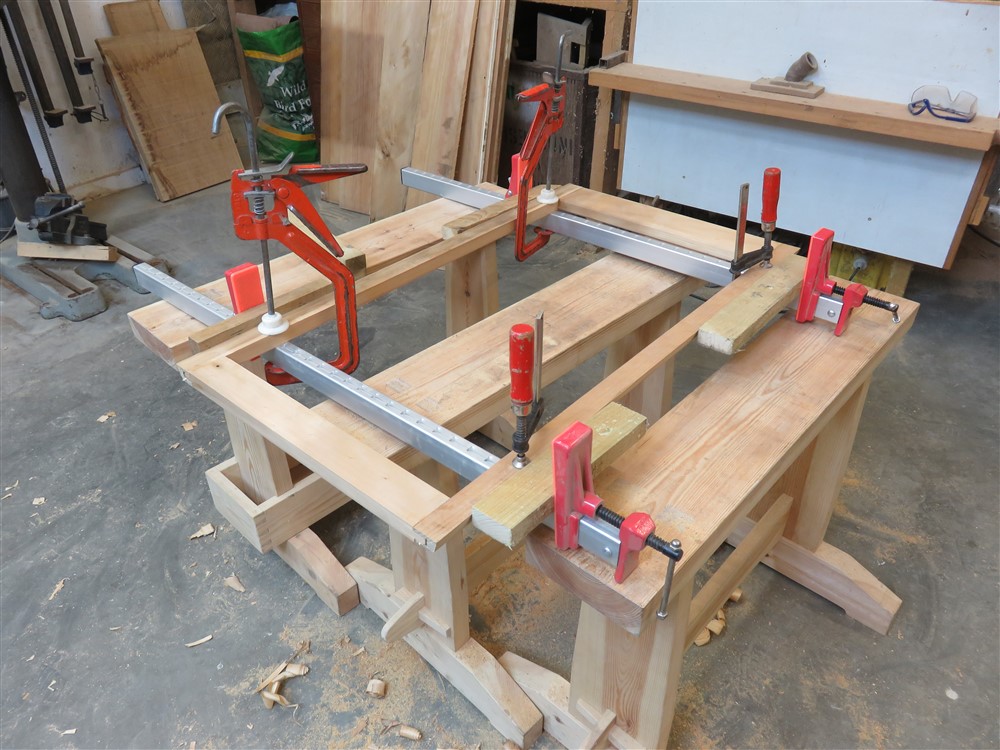