Hi all.
So I'm building a camper box for my 4x4 truck. I bought an ex-asda fridge box. Its too big, so I'm going to cut it apart and use the panels to make a smaller box.
This box is joined at the edges using extruded aluminium. This is fine for a fridge unit but I'm making a camper and I want the camper to be warm. The aluminium protrudes into the inside of the box and therefore will be a cold bridge, transmitting cold into the interior.
So what I want to do, is use wood to join the panels. I created the below diagrams to show what im thinking.
What I would love to ask you guys is, what kind of wood would be suitable for this?
It needs to be strong.
It will likely be exposed to water.
It needs to be available in 80x80mm and in 11 foot lengths (the length of my box)
Advice on treating the wood also appreciated. I haven't undertaken anything like this before. Its my first time working with GRP panels, and sikaflex.
In fact any and all insight or advice appreciated and soaked up, I havnt a notion what im doing lol
truck
regards
So I'm building a camper box for my 4x4 truck. I bought an ex-asda fridge box. Its too big, so I'm going to cut it apart and use the panels to make a smaller box.
This box is joined at the edges using extruded aluminium. This is fine for a fridge unit but I'm making a camper and I want the camper to be warm. The aluminium protrudes into the inside of the box and therefore will be a cold bridge, transmitting cold into the interior.
So what I want to do, is use wood to join the panels. I created the below diagrams to show what im thinking.
What I would love to ask you guys is, what kind of wood would be suitable for this?
It needs to be strong.
It will likely be exposed to water.
It needs to be available in 80x80mm and in 11 foot lengths (the length of my box)
Advice on treating the wood also appreciated. I haven't undertaken anything like this before. Its my first time working with GRP panels, and sikaflex.
In fact any and all insight or advice appreciated and soaked up, I havnt a notion what im doing lol
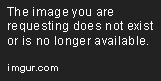
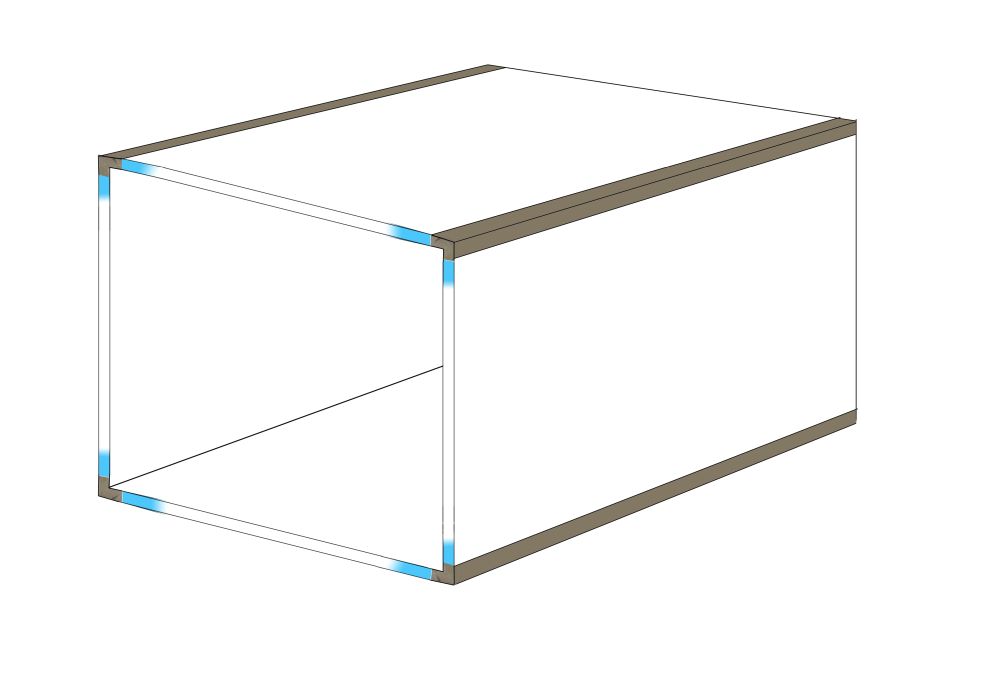
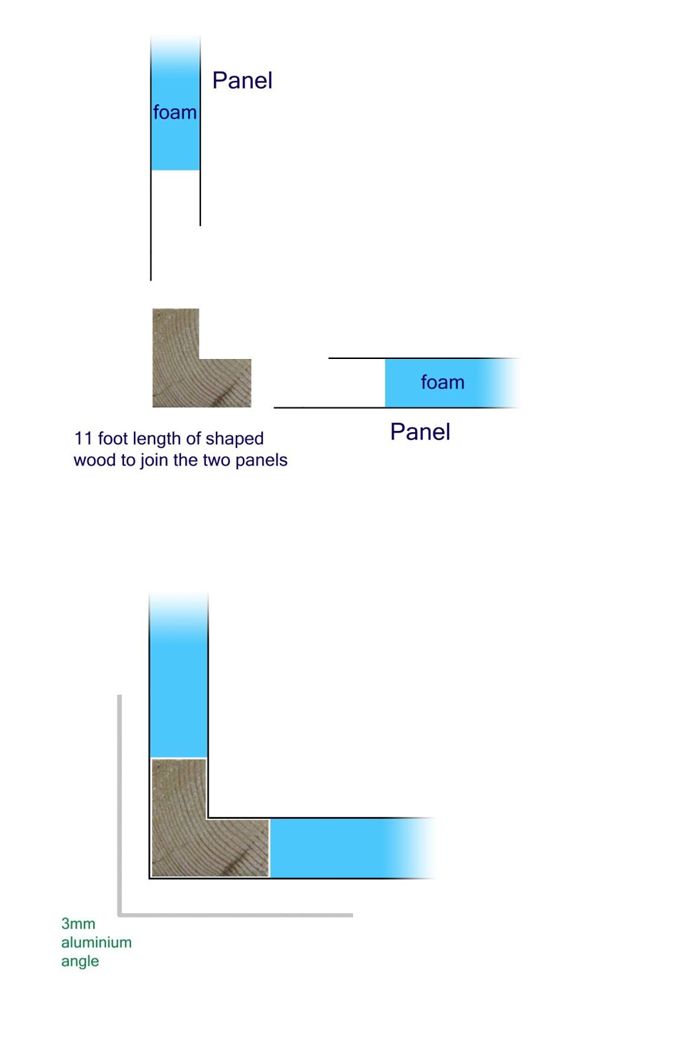
truck
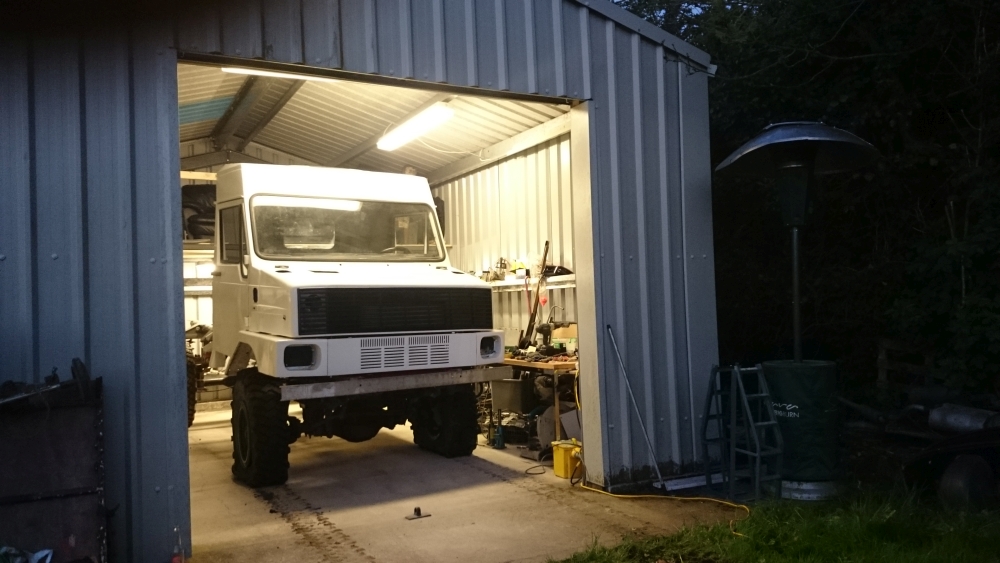
regards