engineer one
Established Member
so no thoughts about marking, maybe i should ask the question on another section. :roll:
anyway made progress to the extent that the basic frame is now finished.
and it stays together without clamps so far.
even more interesting, is the fact that it is level and does not rock.
the cross and lengthway rails are horizontal and also across the corners.
just hope i retain that in glue up :?
so what do you think, not bad, just have to finish the shadow lines on the long rails, and check all the others look similar in conjunction with each other.
[/url]
next part of the process is to cut the grooves for the mdf shelves top and bottom. for strength will use 12mm veneered that i already have,
(thanks jfc :roll: ) that will help keep it square too.
i am still thinking about the end panels and a back one.
will see how it looks over the next couple of days.
thanks for looking again
paul :wink: [/img]
anyway made progress to the extent that the basic frame is now finished.
and it stays together without clamps so far.
even more interesting, is the fact that it is level and does not rock.
the cross and lengthway rails are horizontal and also across the corners.
just hope i retain that in glue up :?
so what do you think, not bad, just have to finish the shadow lines on the long rails, and check all the others look similar in conjunction with each other.

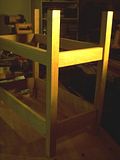
next part of the process is to cut the grooves for the mdf shelves top and bottom. for strength will use 12mm veneered that i already have,
(thanks jfc :roll: ) that will help keep it square too.
i am still thinking about the end panels and a back one.
will see how it looks over the next couple of days.
thanks for looking again
paul :wink: [/img]