engineer one
Established Member
we had thought to make this lump of oak into an oval table ages ago.
however having not got round to it, i decided now to make it into a more rustic, and shapely sofa table which can be used for food or drinking
whilst watching tv.
the top is about 900 x550x 35mm has one slightly curved side and the other side is not square either so it has charm.
i checked through my stock of oak offies and found enough to go where i want. so recently i spent some time hand planing this to flat face and edge, and left it to settle.
after a number of discussions here, i decided to make a jig for more accurately laying out the mortices in the legs and ensuring that i got the legs orientated properly all the times.
it is only a simple base with two sides at right angles to each other. the toe board is higher than the side to allow for use of the square across the sides. i just cut up some offies and screwed them together.
since it is not as long as the legs, i also ensured that i had spare piece of wood the thickness of the base to ensure that the legs would stay horizontal. i then clamped them in the jig, and marked out the mortice tops and bottoms and the orientation.
upon release i used a wheel gauge to mark the widths.
[/url]
[/img]
this shows the jig, the marking tools, and the wood pile before cutting :roll:
the next stage is to cut the mortices, and the jig is universal enough to be turned over and used as the cutting surface for the mortices.
next bit is the legs with the mortices.
sorry about the different picture contrast, my workroom has very bad light, and my camera is not all it should be :?
paul :wink:
however having not got round to it, i decided now to make it into a more rustic, and shapely sofa table which can be used for food or drinking
whilst watching tv.
the top is about 900 x550x 35mm has one slightly curved side and the other side is not square either so it has charm.
i checked through my stock of oak offies and found enough to go where i want. so recently i spent some time hand planing this to flat face and edge, and left it to settle.
after a number of discussions here, i decided to make a jig for more accurately laying out the mortices in the legs and ensuring that i got the legs orientated properly all the times.
it is only a simple base with two sides at right angles to each other. the toe board is higher than the side to allow for use of the square across the sides. i just cut up some offies and screwed them together.
since it is not as long as the legs, i also ensured that i had spare piece of wood the thickness of the base to ensure that the legs would stay horizontal. i then clamped them in the jig, and marked out the mortice tops and bottoms and the orientation.
upon release i used a wheel gauge to mark the widths.

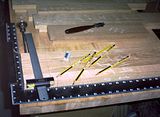
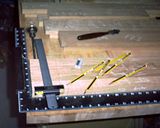

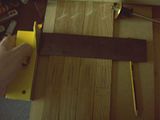
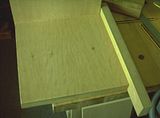
[/img]
this shows the jig, the marking tools, and the wood pile before cutting :roll:
the next stage is to cut the mortices, and the jig is universal enough to be turned over and used as the cutting surface for the mortices.
next bit is the legs with the mortices.
sorry about the different picture contrast, my workroom has very bad light, and my camera is not all it should be :?
paul :wink: