Scouse
Established Member
First of all, if you are after a jaw-dropping rebuild WIP of Wallace proportions, keep right on walking, there’s nothing to see here. If, on the other hand, you enjoy endless detail about the minutiae of a reasonable example of a basic handtool, then put the kettle on; there's not much about them online so it's worthwhile pushing the boat out a bit.
As I noted in another thread, for some reason I find the number of mechanical methods our species has found to put a hole in something fascinating. The somewhat inevitable result of this is that over the years I have owned and restored a few drills; fairly recent English Stanleys, mid century Leytools, early 20th century Millers Falls and their Goodell-Pratt, Mohawk-Shelburne variants, hand drills, breast drills, on and on goes the list.
I would like to tell you that the opportunity to pick up a Yankee was irresistible, that I had been on the lookout etc. But the truth is that I didn’t even recognise it as the early morning mist cleared from my hungover brain and I spotted a breast drill plate sticking out of a box, which promised the possibility of yielding a side handle for an early (1915-21) green main gear Millers Falls number 12 I had just finished restoring.
Out of the box came the drill, I remained impassive as the chap accepted a fiver for what I now knew was unlikely to become a handle donor...
... Because it is a North Bros. Yankee 1555 ratcheting breast drill. It was very dirty on arrival at the Scouse residence, the actual model obscured by a thick layer of grease, but it was given a wipe and put to one side for cleaning and general restoration.
Many moons ago the hidden mechanism of a Leytool drill, and the associated difficulty in opening said tool, resulted in my speculation that the drill might be powered by magic, treadmills and a colony of a revolutionary pixies existing in a utopian Marxist society, underpinned by a workers co-operative.
I was wrong. But I was prepared to believe that something similar was afoot inside the seemingly incomprehensible workings of this drill. Turn it forward and it spins, turn it backward and it still spins in the same direction! Must be magic. I was wrong again, but old fashioned engineering, it would appear, is better than new age hocus pocus.
Having once tried to take apart a fairly modern Stanley Yankee screwdriver and ending up with bits of brass and rude words flying around the workshop, my bottle went and the drill sat on a shelf with an air of dishevelled superiority and a slight musty smell. A bit like the royal family.
So here we are, almost a year later, and I have finally plucked up the courage to take it apart.
The chuck unscrewed, as you would expect. No surprises yet, except for the fact that the dirt is sitting on an even coat of grease which has protected the drill and meant that there are no seized screws.
As a result the chuck comes apart with ease. It’s similar to the Ryther’s chuck found on some Millers Falls drills (and an example here), but the internal top pressure plate (as it is now called!) is machined away to accept the tops of the jaws. On a Ryther’s chuck the jaws are simply held in place below the pressure plate by ‘S’ springs and a wider profile (the three of them held together form a cone); in this case they have flat sides sitting in the machined underside of the pressure plate.
The three jaws are held on by ‘S’ shaped springs which hook over the plate and are slipped into slots cut into the jaw. Unlike the Millers Falls chuck, the Yankee jaws have a small square machined out with a pin pressed into it, through which is drilled a hole. It really is as complicated as it sounds; why would they not just drill a hole in the jaw?
At this point I would point out an ongoing theme regarding the Victorian level of thought and over-engineering present on the drill.
A quick example or two:
The end of the side handle, has a flat ground into it, which acts as a screwdriver for the various screws present, allowing maintenance without the need for an extra tool, as you can see from the helpful picture below, demonstrating the use of a screwdriver.
The top of the frame where the breast plate is attached has a pin which fits into one of two holes in the plate for repositioning at angles 90 degrees apart, very precise. It seems like a complicated step to use a system such as this rather than simply machine a divot in the side and put a machine screw through the edge of the plate as with other drills of the period. Thus;
Yet in spite of this engineering flamboyance, I read on the Old Tools List that the metallurgy used by North Bros. results in a weakness in the gears which means they commonly lose teeth. A strange anomaly which I suspect will result in me using this drill less than I would otherwise; 1/8th inch pilot holes maybe. That's what it was made for...
As I noted in another thread, for some reason I find the number of mechanical methods our species has found to put a hole in something fascinating. The somewhat inevitable result of this is that over the years I have owned and restored a few drills; fairly recent English Stanleys, mid century Leytools, early 20th century Millers Falls and their Goodell-Pratt, Mohawk-Shelburne variants, hand drills, breast drills, on and on goes the list.
I would like to tell you that the opportunity to pick up a Yankee was irresistible, that I had been on the lookout etc. But the truth is that I didn’t even recognise it as the early morning mist cleared from my hungover brain and I spotted a breast drill plate sticking out of a box, which promised the possibility of yielding a side handle for an early (1915-21) green main gear Millers Falls number 12 I had just finished restoring.
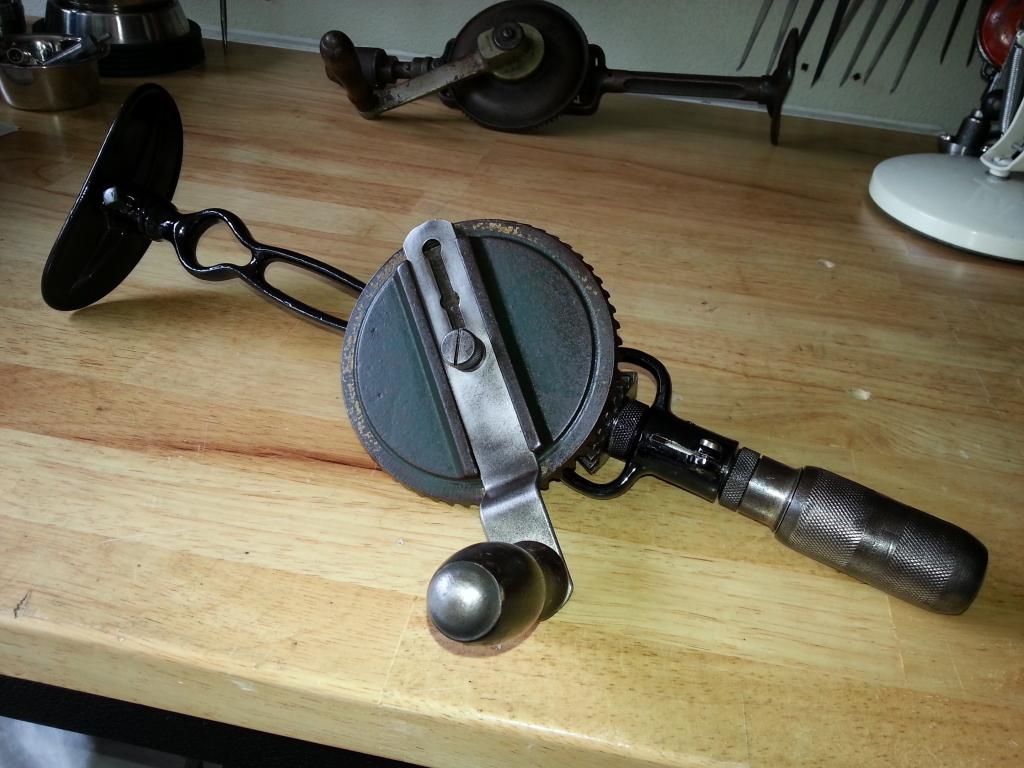
Out of the box came the drill, I remained impassive as the chap accepted a fiver for what I now knew was unlikely to become a handle donor...
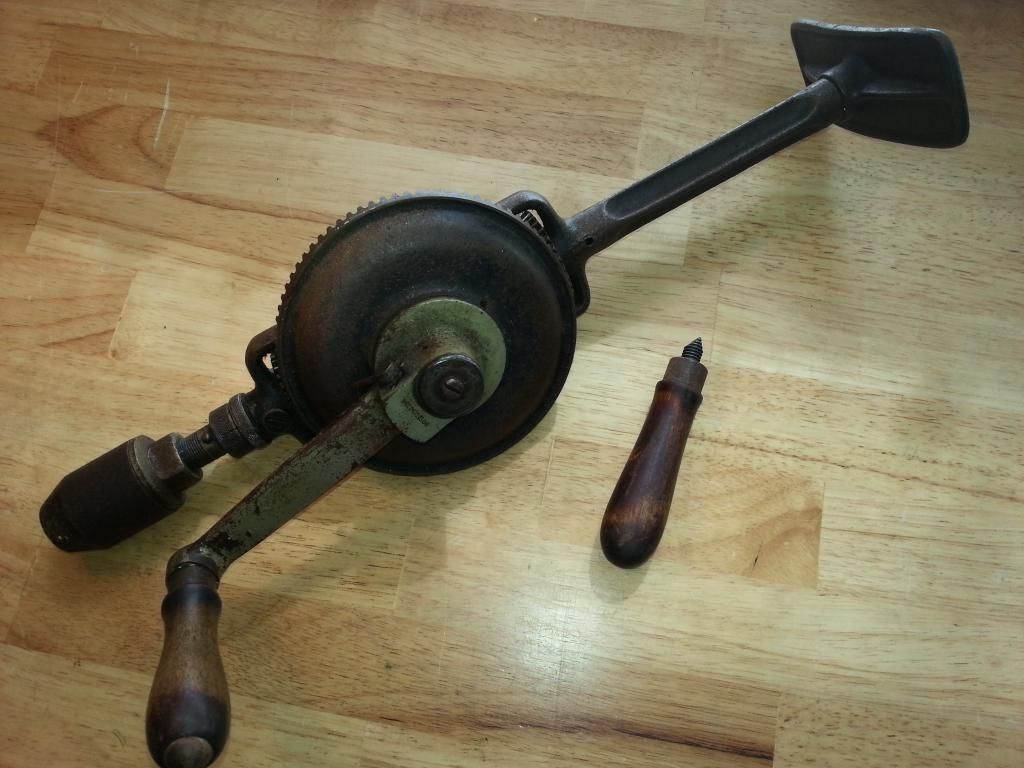
... Because it is a North Bros. Yankee 1555 ratcheting breast drill. It was very dirty on arrival at the Scouse residence, the actual model obscured by a thick layer of grease, but it was given a wipe and put to one side for cleaning and general restoration.
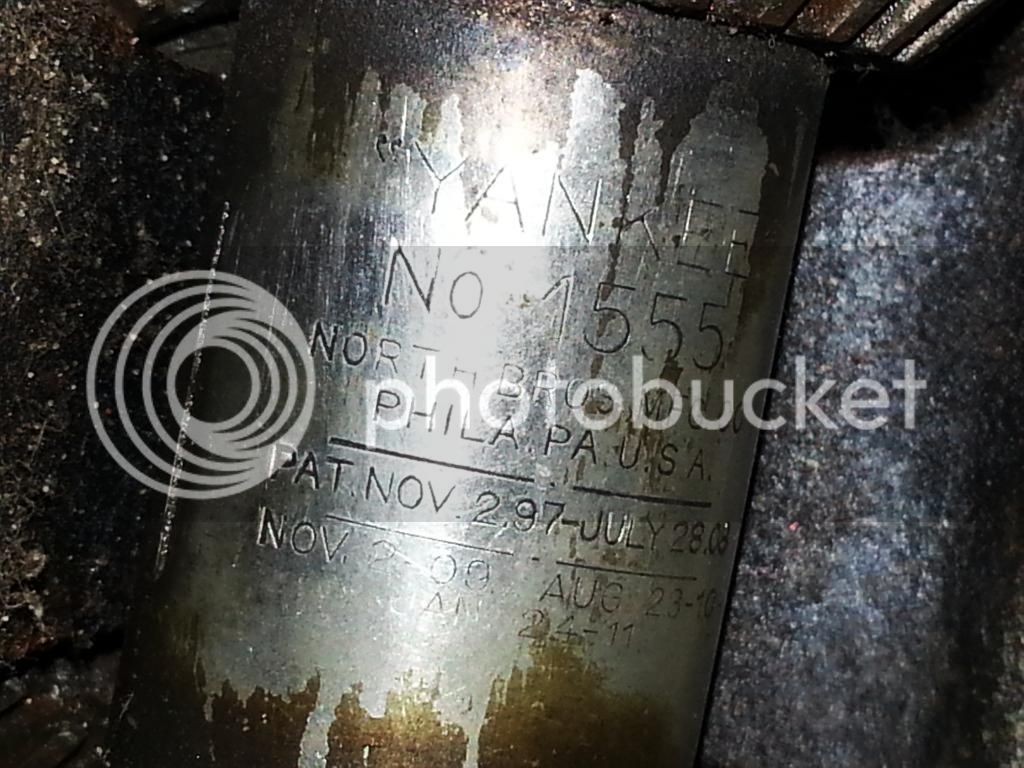
Many moons ago the hidden mechanism of a Leytool drill, and the associated difficulty in opening said tool, resulted in my speculation that the drill might be powered by magic, treadmills and a colony of a revolutionary pixies existing in a utopian Marxist society, underpinned by a workers co-operative.
I was wrong. But I was prepared to believe that something similar was afoot inside the seemingly incomprehensible workings of this drill. Turn it forward and it spins, turn it backward and it still spins in the same direction! Must be magic. I was wrong again, but old fashioned engineering, it would appear, is better than new age hocus pocus.
Having once tried to take apart a fairly modern Stanley Yankee screwdriver and ending up with bits of brass and rude words flying around the workshop, my bottle went and the drill sat on a shelf with an air of dishevelled superiority and a slight musty smell. A bit like the royal family.
So here we are, almost a year later, and I have finally plucked up the courage to take it apart.
The chuck unscrewed, as you would expect. No surprises yet, except for the fact that the dirt is sitting on an even coat of grease which has protected the drill and meant that there are no seized screws.
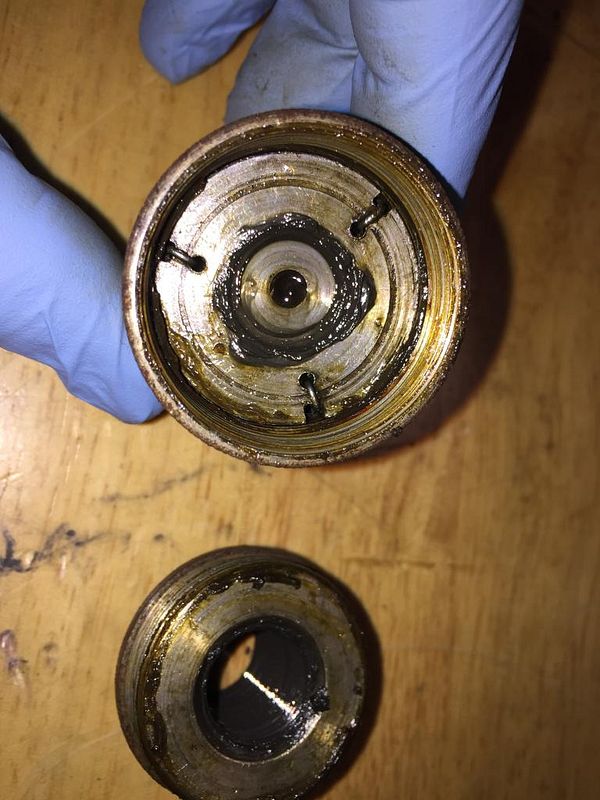
As a result the chuck comes apart with ease. It’s similar to the Ryther’s chuck found on some Millers Falls drills (and an example here), but the internal top pressure plate (as it is now called!) is machined away to accept the tops of the jaws. On a Ryther’s chuck the jaws are simply held in place below the pressure plate by ‘S’ springs and a wider profile (the three of them held together form a cone); in this case they have flat sides sitting in the machined underside of the pressure plate.
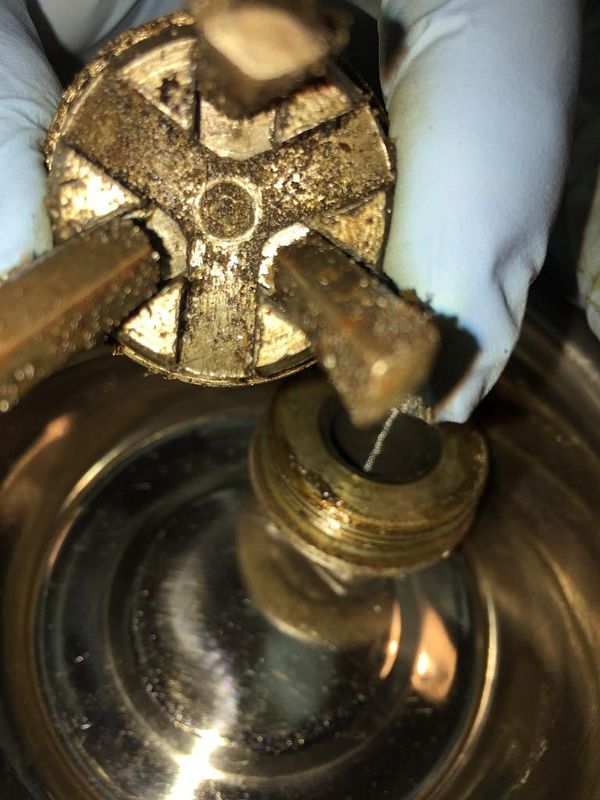
The three jaws are held on by ‘S’ shaped springs which hook over the plate and are slipped into slots cut into the jaw. Unlike the Millers Falls chuck, the Yankee jaws have a small square machined out with a pin pressed into it, through which is drilled a hole. It really is as complicated as it sounds; why would they not just drill a hole in the jaw?
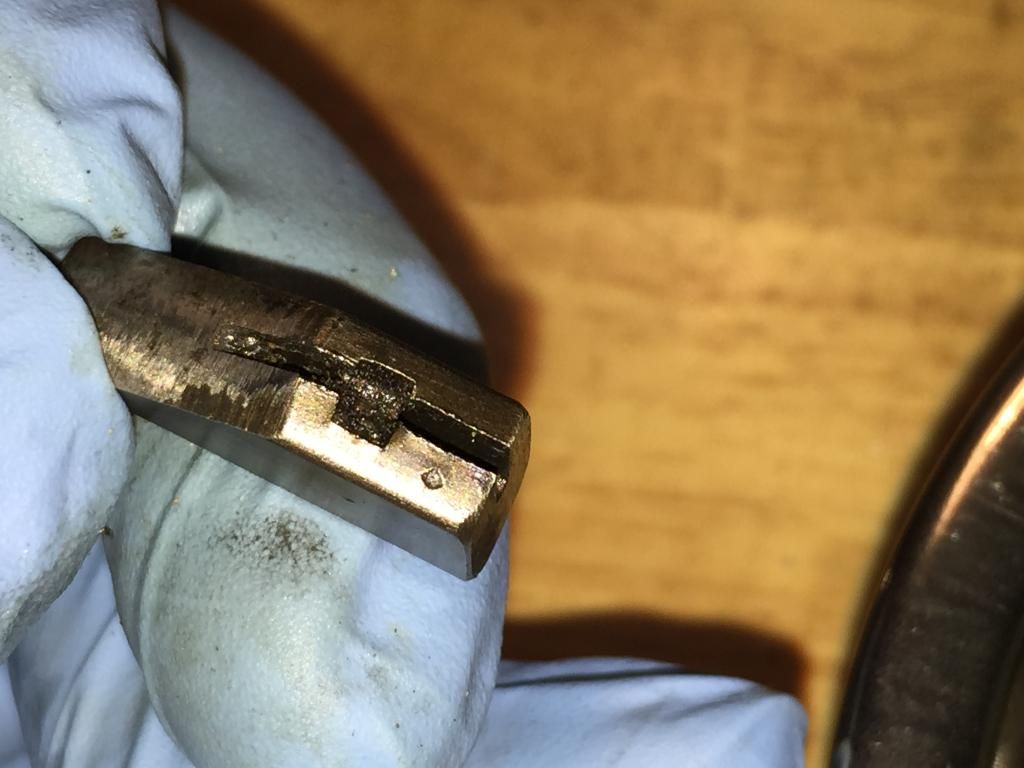
At this point I would point out an ongoing theme regarding the Victorian level of thought and over-engineering present on the drill.
A quick example or two:
The end of the side handle, has a flat ground into it, which acts as a screwdriver for the various screws present, allowing maintenance without the need for an extra tool, as you can see from the helpful picture below, demonstrating the use of a screwdriver.
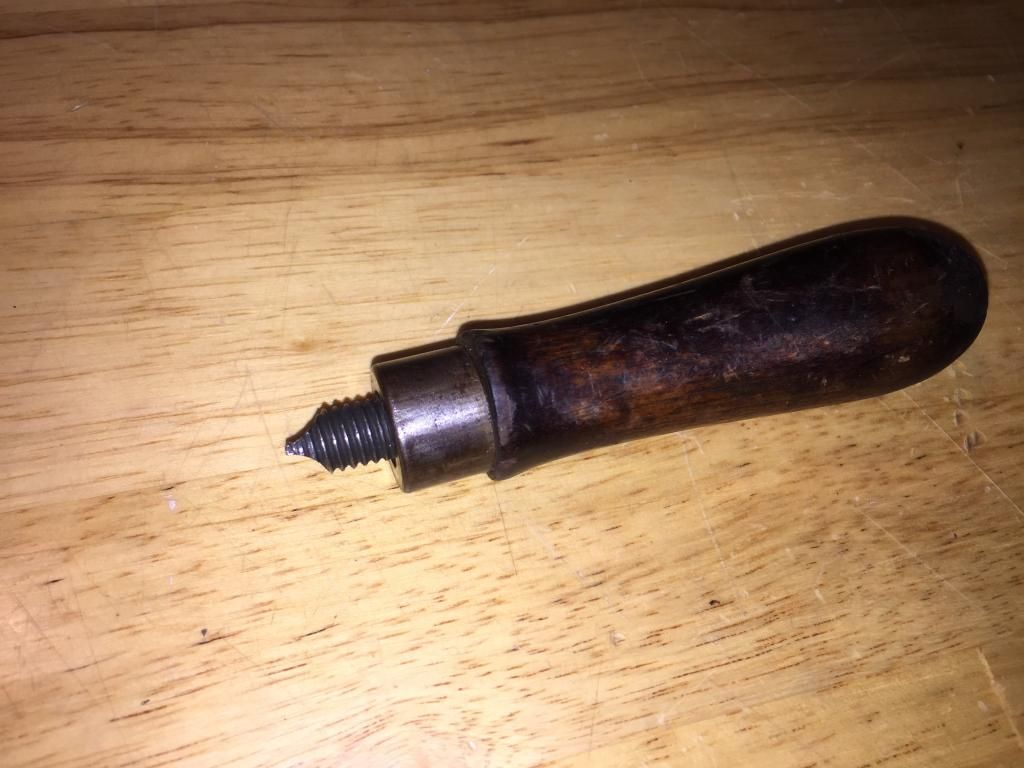
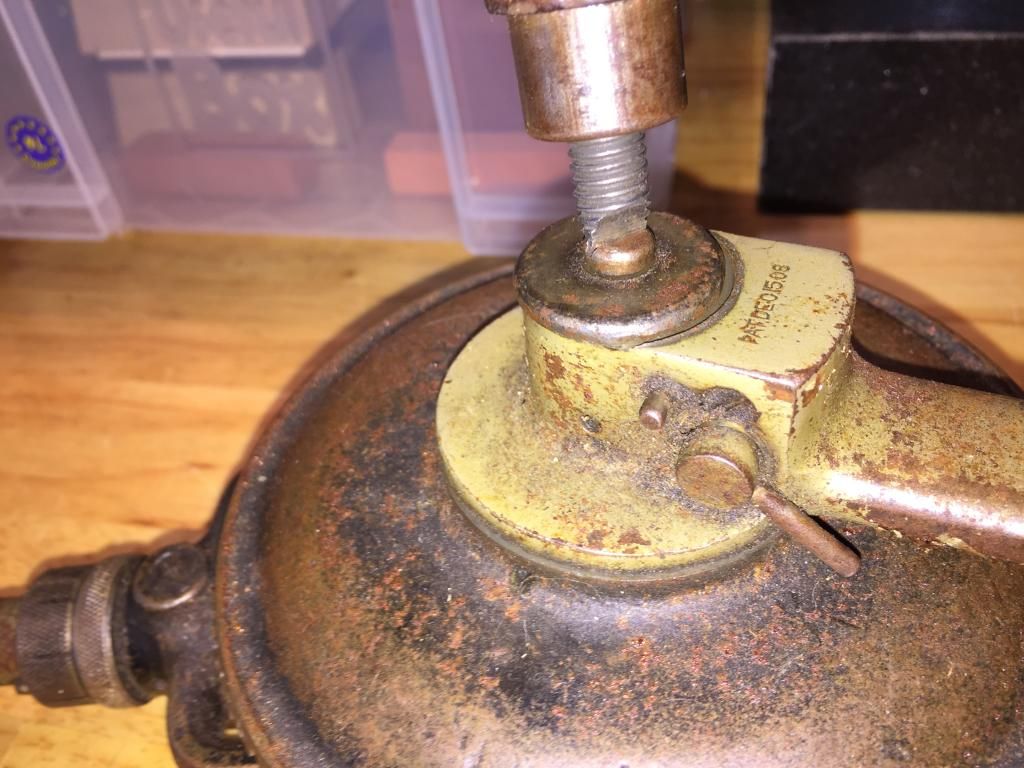
The top of the frame where the breast plate is attached has a pin which fits into one of two holes in the plate for repositioning at angles 90 degrees apart, very precise. It seems like a complicated step to use a system such as this rather than simply machine a divot in the side and put a machine screw through the edge of the plate as with other drills of the period. Thus;
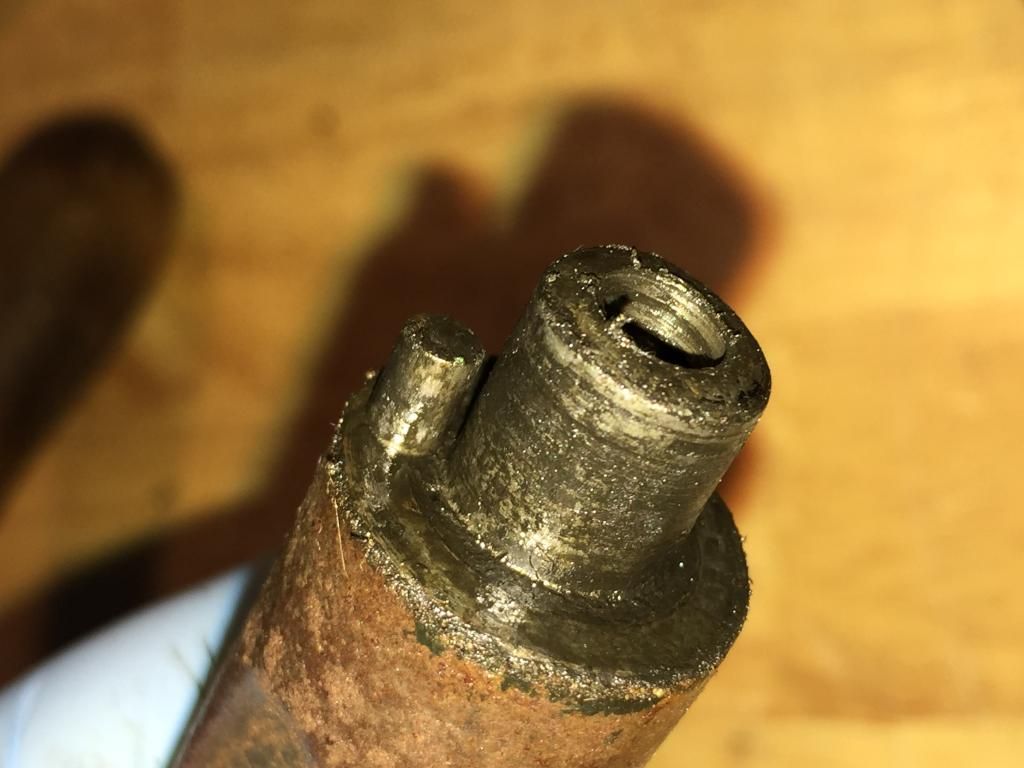
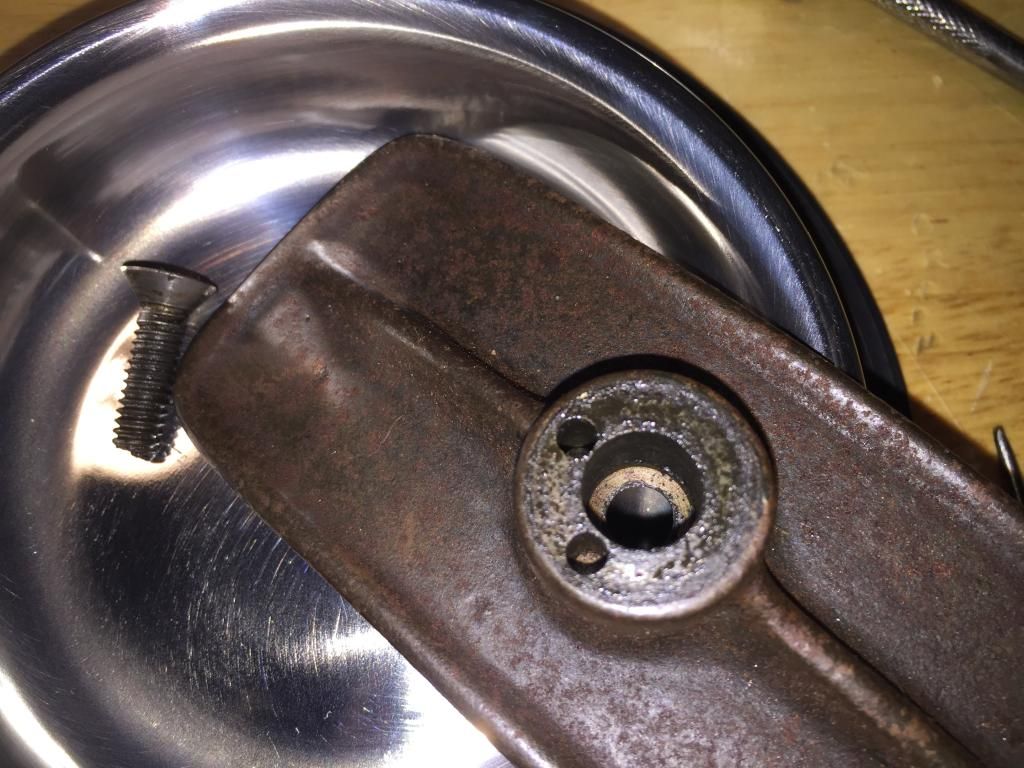
Yet in spite of this engineering flamboyance, I read on the Old Tools List that the metallurgy used by North Bros. results in a weakness in the gears which means they commonly lose teeth. A strange anomaly which I suspect will result in me using this drill less than I would otherwise; 1/8th inch pilot holes maybe. That's what it was made for...