kirkpoore1
Established Member
Since, as Mark Twain said, we are divided by a common language, I always find it interesting when the folks on this forum talk about a "garden shed" but come up with these very solid concrete block and brick structures suitable for holding off the Normandy invasion for a few hours (or until you run out of beer). Shed, in the American vernacular, definitely implies a much lighter structure, often slapped together, and usually used for storage. Yes, there are very elaborate exceptions to this, but you get my drift. What goes for a shed in this forum we'd definitely call a shop, since you use it for working in.
Well, I built a shop a couple of years ago, but now I need more. Not for machines, but for this:
It's about 800 bd ft of oak and sycamore, with a little cedar thrown in, all in eyesore form. Sooner or later I have to tell the city that I make & sell stuff out of my shop, and they get upset if you store materials outside. My neighbors are nice and haven't got upset, but why push them? So I went to the Borg (Home Depot, the local big box hardware & building supply store) and bought a shed. Now, city regulations say you have to keep it under a hundred square feet or you need a permit for anything permanent, and to hold the weight it was going to have to have a permanent foundation of some kind. So I bought an 8'x12' shed and had it delivered (in it's constituent boxes, stacked on a long pallet). The truck driver was amused by my johnson bar and pallet jack, and asked when I was going to pull out the forklift. I replied that if I had one, I'd have brought it out first.
But we parked the pallet in the garage, where it sat for the next two months.
I added poured piers to the list of stuff I needed my contractor to do, and the piers were done a month before I was ready. My first job was to add treated wood pads to give the base something to screw into:
The piers are 8" across and go down 30" below ground level. After screwing the pads the piers, I still had to make up over an inch in places to get all of them level. This was done by running some PT 2x6 scrap through the planer until the needed thickness was achieved, then the new blocks screwed into the old ones. Then I started on the frame:
All PT 2x6 construction.
Decking is 3/4" pressure treated ply. I had lots of gavanized 2" roofing nails left over from the shop build, so I used some of them up.
Shed floor applied:
Now, this shed didn't seem to have enough ventilation for when I put green lumber in there, so I added some vents:
(Yes, they're screwed down too.)
Then things got busy, and I forgot to take pictures until it was up:
The floor took Friday evening through Saturday, and the sides and roof took Sunday, plus Monday and Tuesday evening. Clever, apparently tough design. All parts snap together and then are screwed using some heavy duty screws. We had a major storms come through on both Sunday night and Monday, and even while only part complete and empty the shed held up just fine. Since the sides snap into the floor, but don't screw down, I added more screws just to be sure (after the storms).
Finally, it was time to load. The sycamore took Wednesday evening. Many of the pieces were too long (13'), so I had to cut them down. The oak and cedar went in on Thursday.
So there's room left for more wood, yard tools, and maybe even a ratholed machine or two--as long as my wife doesn't stash stuff in it first. Maybe a little expensive for a mere storage shed ($1600 or so including foundation, and wood floor), but it will keep everyone happy for a good long time.
Oh, and here's the end result, just waiting for large item pickup day by the trash men:
Kirk
Well, I built a shop a couple of years ago, but now I need more. Not for machines, but for this:
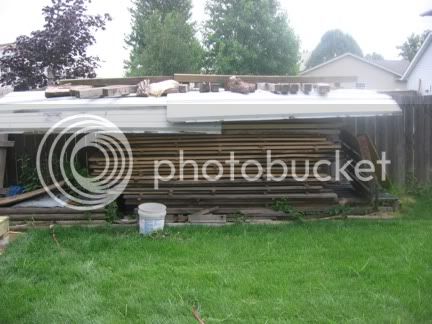
It's about 800 bd ft of oak and sycamore, with a little cedar thrown in, all in eyesore form. Sooner or later I have to tell the city that I make & sell stuff out of my shop, and they get upset if you store materials outside. My neighbors are nice and haven't got upset, but why push them? So I went to the Borg (Home Depot, the local big box hardware & building supply store) and bought a shed. Now, city regulations say you have to keep it under a hundred square feet or you need a permit for anything permanent, and to hold the weight it was going to have to have a permanent foundation of some kind. So I bought an 8'x12' shed and had it delivered (in it's constituent boxes, stacked on a long pallet). The truck driver was amused by my johnson bar and pallet jack, and asked when I was going to pull out the forklift. I replied that if I had one, I'd have brought it out first.
I added poured piers to the list of stuff I needed my contractor to do, and the piers were done a month before I was ready. My first job was to add treated wood pads to give the base something to screw into:
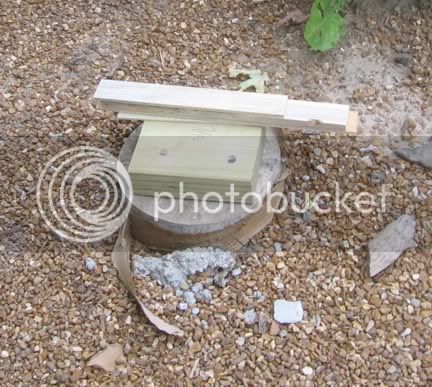
The piers are 8" across and go down 30" below ground level. After screwing the pads the piers, I still had to make up over an inch in places to get all of them level. This was done by running some PT 2x6 scrap through the planer until the needed thickness was achieved, then the new blocks screwed into the old ones. Then I started on the frame:
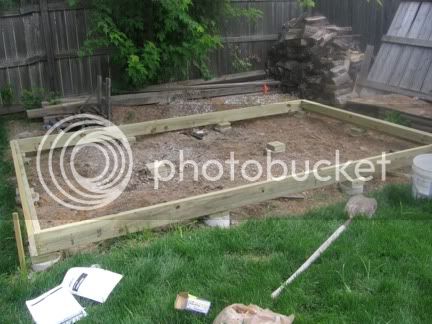
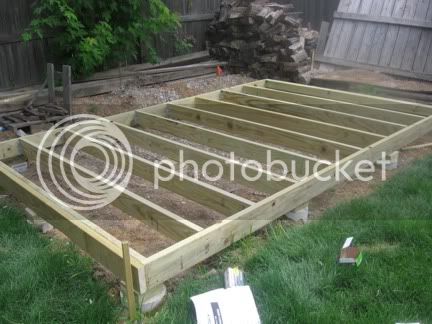
All PT 2x6 construction.
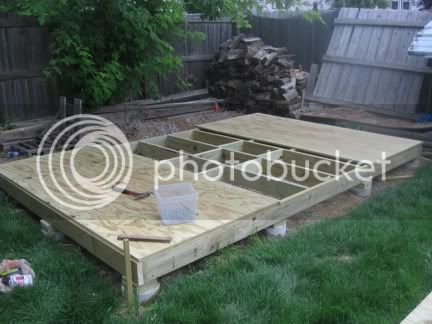
Decking is 3/4" pressure treated ply. I had lots of gavanized 2" roofing nails left over from the shop build, so I used some of them up.
Shed floor applied:
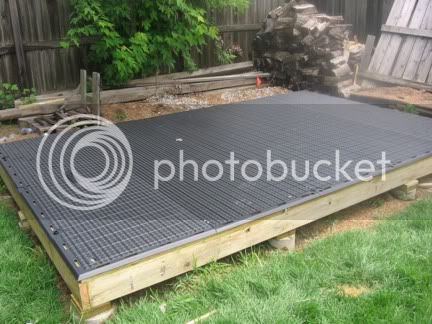
Now, this shed didn't seem to have enough ventilation for when I put green lumber in there, so I added some vents:
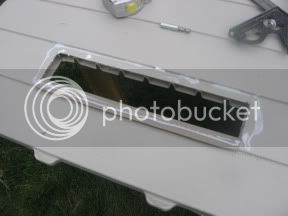
(Yes, they're screwed down too.)
Then things got busy, and I forgot to take pictures until it was up:
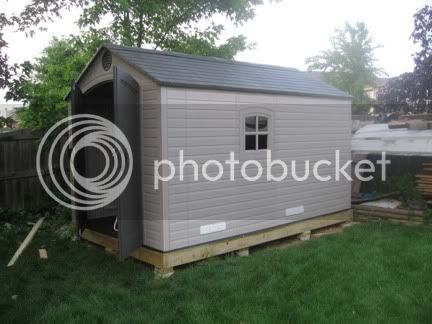
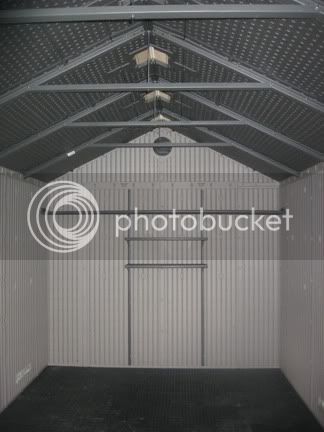
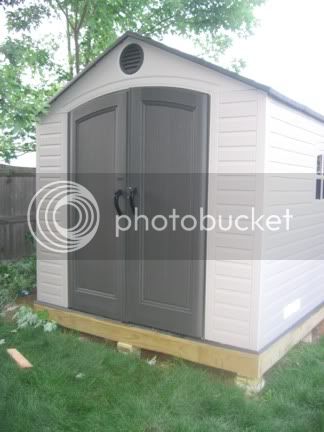
The floor took Friday evening through Saturday, and the sides and roof took Sunday, plus Monday and Tuesday evening. Clever, apparently tough design. All parts snap together and then are screwed using some heavy duty screws. We had a major storms come through on both Sunday night and Monday, and even while only part complete and empty the shed held up just fine. Since the sides snap into the floor, but don't screw down, I added more screws just to be sure (after the storms).
Finally, it was time to load. The sycamore took Wednesday evening. Many of the pieces were too long (13'), so I had to cut them down. The oak and cedar went in on Thursday.
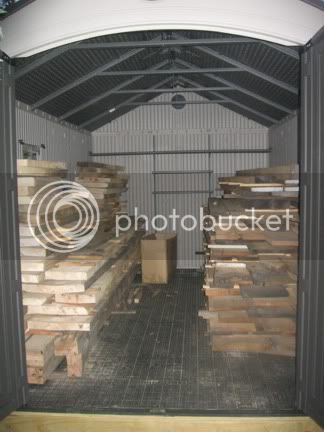
So there's room left for more wood, yard tools, and maybe even a ratholed machine or two--as long as my wife doesn't stash stuff in it first. Maybe a little expensive for a mere storage shed ($1600 or so including foundation, and wood floor), but it will keep everyone happy for a good long time.
Oh, and here's the end result, just waiting for large item pickup day by the trash men:
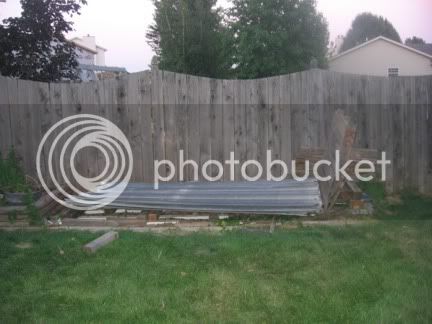
Kirk