- Joined
- 11 Mar 2009
- Messages
- 1,315
- Reaction score
- 11
Any seasoned vacuum pressers out there, I would really appreciate your help here. I made a former out of 18mm mdf and 18mm chipboard that I had lying around in the garage. The former looked great, but on the 1st test run before gluing up, it did not even get to full vacuum before the vacuum just destroyed it
I have attached a couple of pictures. Did I go wrong by using mdf / chipboard ?
Any pointers really welcomed
Thanks
I have attached a couple of pictures. Did I go wrong by using mdf / chipboard ?
Any pointers really welcomed
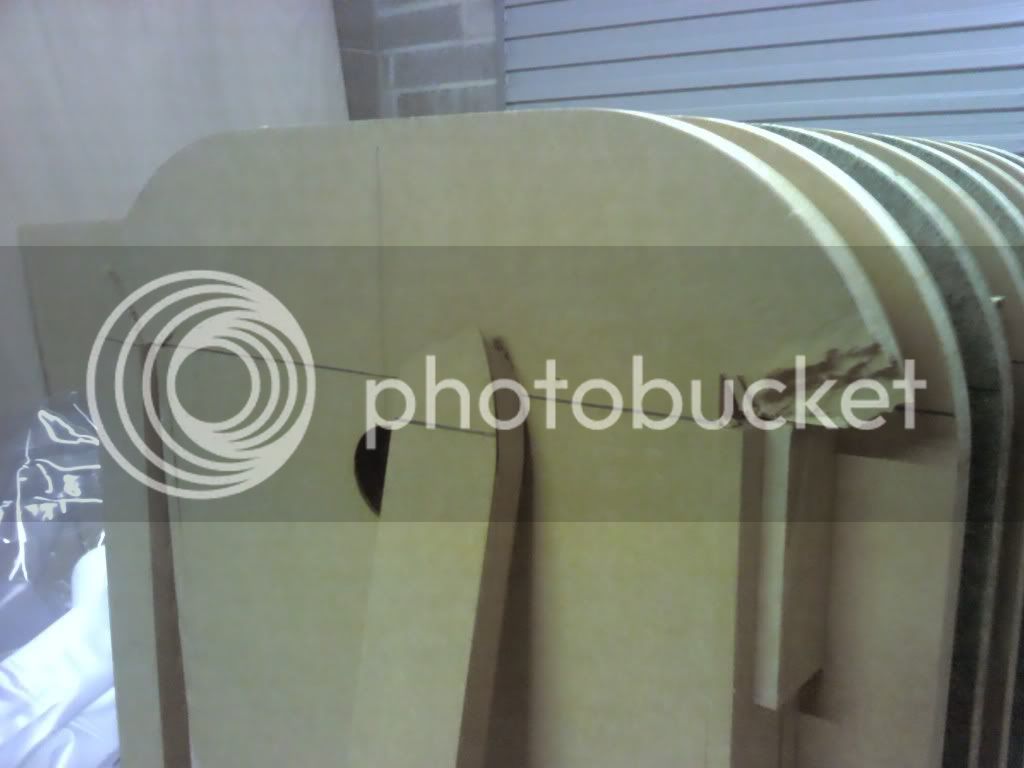
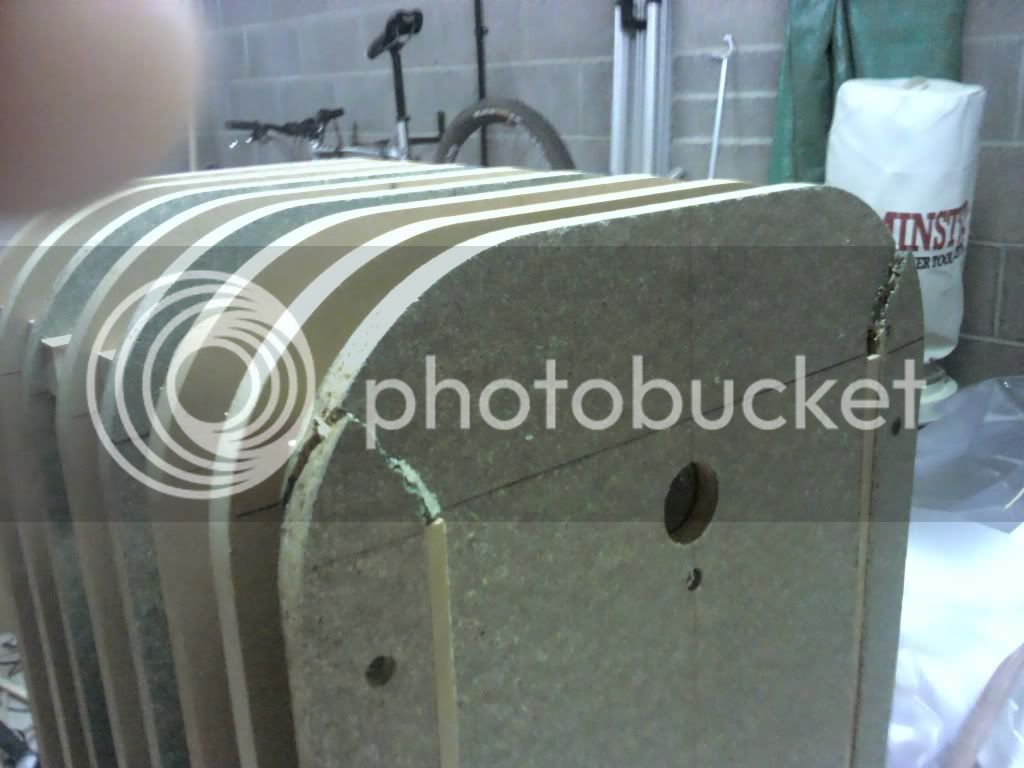
Thanks