I've been browsing forums trying to search for insulation advice for my concrete prefab workshop but whatever I read raises question so thought I better join a forum and this seems like a fairly busy one with solid info.
So moved into my new house on 1st June and I had compromised on buying a house without a garage as long as it had a garden big enough to build a workshop.
Once the house was sorted I started work...
Base dug out to 6" throughout and DPM was laid before concrete was poured.
I had the ferns cut before workshop was installed
Then voila!
It's a 16'6"x9' with 30" steel door and UPVC throughout, I wanted minimal upkeep so didn't want to need to treat wood regularly.
Insulation wise I was planning on a basic stud work wall around the inside with 2x2 as to not take too much space, the most I'll have directly on the wall are hand tool hangers and those plastic box racks. Then fill the void with sheet polystyrene.
Much the same on the roof aswell, just using a thinner ply to board it out.
My main question is what kind of ventilation should I leave into the insulation space?
I'm using Thomson water seal on the outside and was going to coat the inside too to reduce ingress damp(?)
I was originally thinking of using celotex/kingspan originally but unless some comes up dirt cheap then it's too expensive.
Comments and advice much appreciated!
So moved into my new house on 1st June and I had compromised on buying a house without a garage as long as it had a garden big enough to build a workshop.
Once the house was sorted I started work...
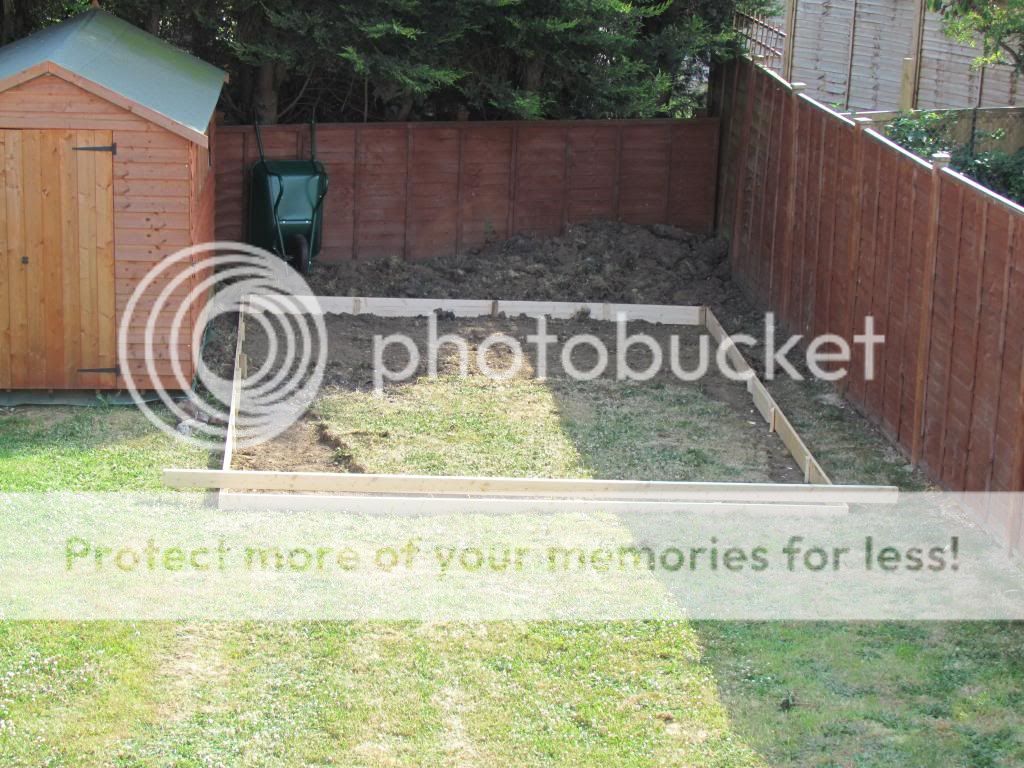
Base dug out to 6" throughout and DPM was laid before concrete was poured.
I had the ferns cut before workshop was installed
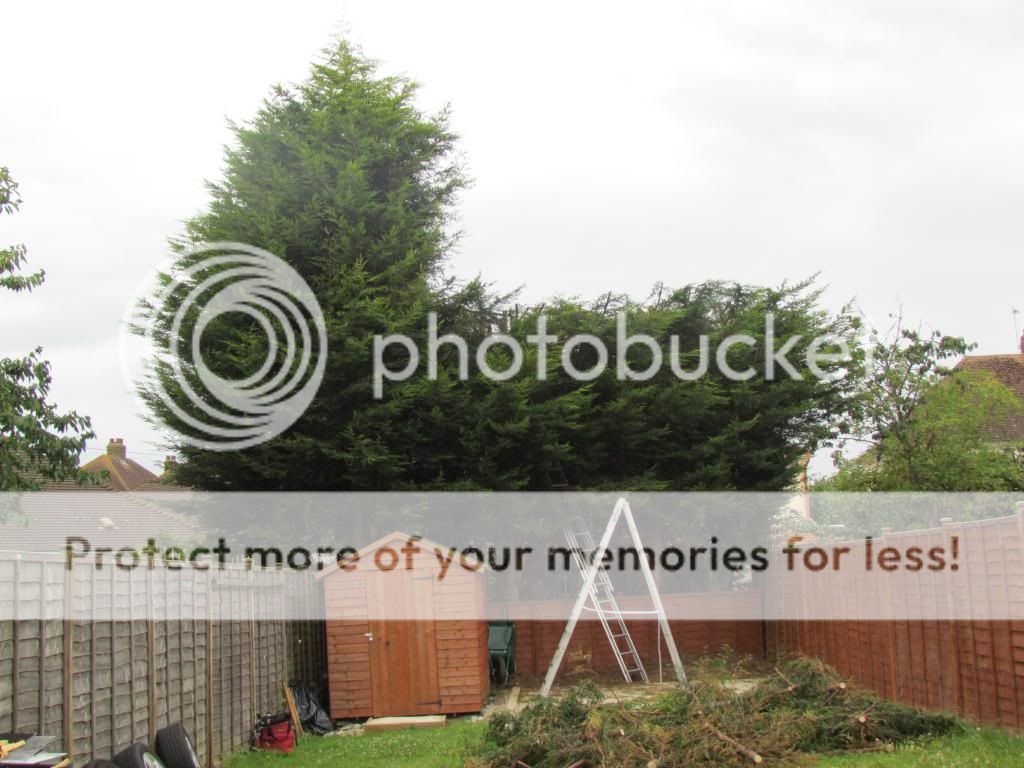
Then voila!

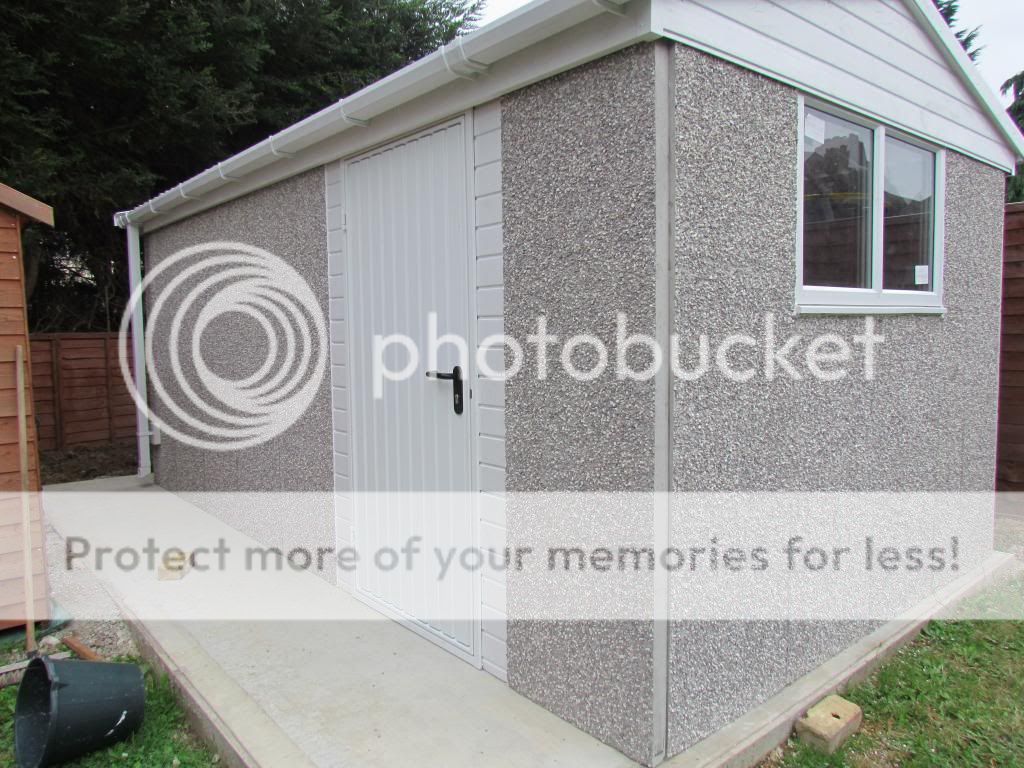
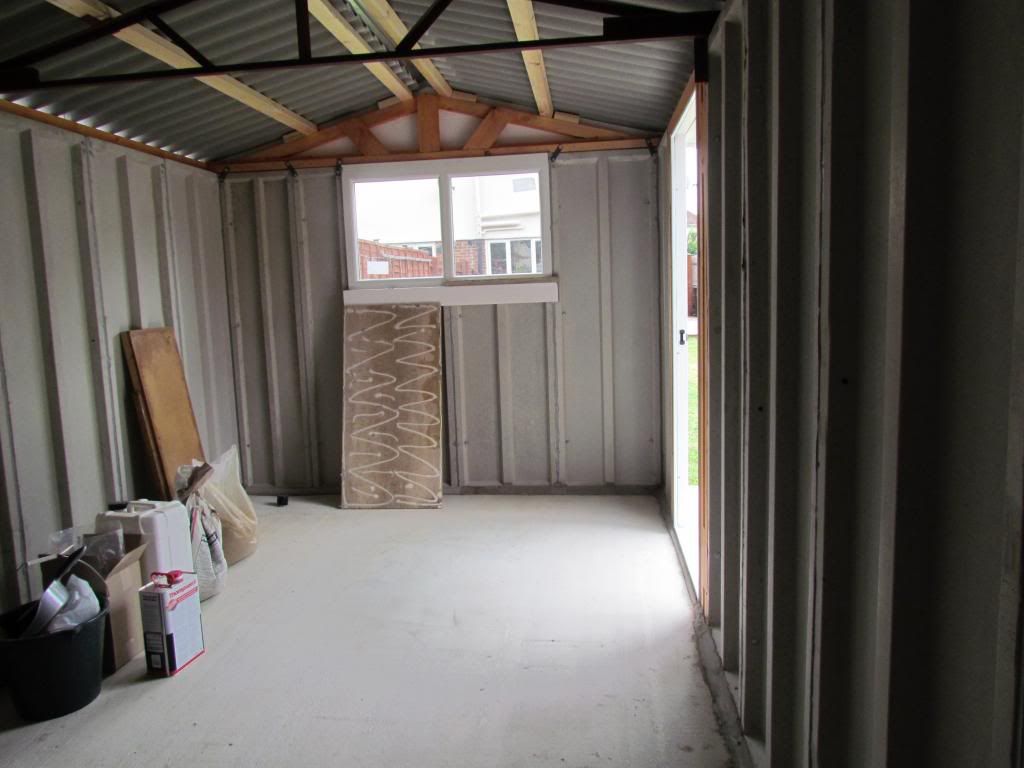

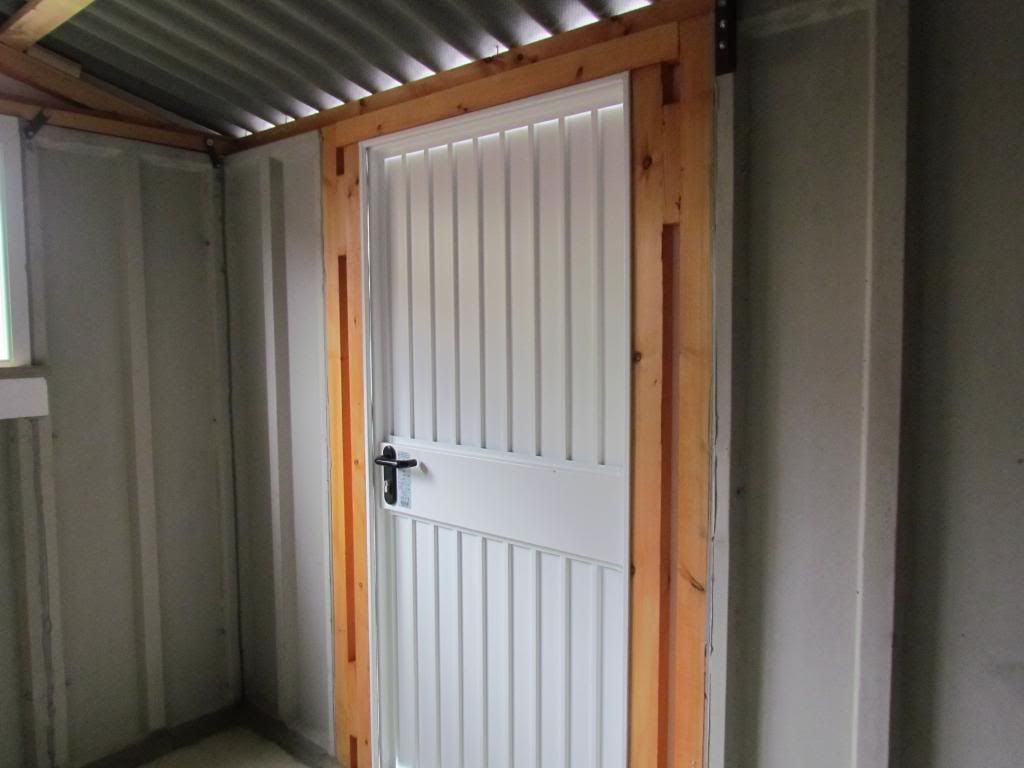
It's a 16'6"x9' with 30" steel door and UPVC throughout, I wanted minimal upkeep so didn't want to need to treat wood regularly.
Insulation wise I was planning on a basic stud work wall around the inside with 2x2 as to not take too much space, the most I'll have directly on the wall are hand tool hangers and those plastic box racks. Then fill the void with sheet polystyrene.
Much the same on the roof aswell, just using a thinner ply to board it out.
My main question is what kind of ventilation should I leave into the insulation space?
I'm using Thomson water seal on the outside and was going to coat the inside too to reduce ingress damp(?)
I was originally thinking of using celotex/kingspan originally but unless some comes up dirt cheap then it's too expensive.
Comments and advice much appreciated!