Hi all.
I'm doing a few test cuts where I'm carving simple letter-forms into Ziricote using a 0.5mm end mill and cutting to a depth of 0.75mm before filling the resulting channels with glue/resin to make them legible.
Here's an example:
As luck would have it - that was a reasonably successful effort, but on smaller typography where there are tiny islands of wood (like the inside of the A) - or long sharp corners (M's N's etc.) there's a constant danger of tear-out, which is what happened here:
(Point of a cocktail stick for reference :lol: )
There's a brief video of the cutting process here:
YouTube link
If this were a one or two-off object I'd probably cut as normal (expecting a bit of tear-out) fill any resultant tear-out with a resin mixed with dust particles from the wood, and then re-cut the repaired sections relying on the resin to hold everything together.
The problem is that if the project goes ahead I'll need to make around 60 off, in batches, where I can't really afford the time to have my router sat doing nothing whilst I fill the problem areas and allow the resin to cure in situ before re-cutting.
So - Is there an elegant/clever way to stabilise the surface of the wood (up to a depth of 1mm) to eliminate this kind of tear-out? I've heard of Cactus Juice et al - but when I've seen it used in the past (from where I was standing) it appeared to be a waste of time - furthermore, it's not recommended for close-grained or oily woods - Ziricote falls into both of those categories..! - maybe it's close grained nature means that I'm asking the impossible and just need to bite the bullet when the time comes and repair what needs repairing...
Thanks for reading this far - any suggestions..?
Wal.
I'm doing a few test cuts where I'm carving simple letter-forms into Ziricote using a 0.5mm end mill and cutting to a depth of 0.75mm before filling the resulting channels with glue/resin to make them legible.
Here's an example:
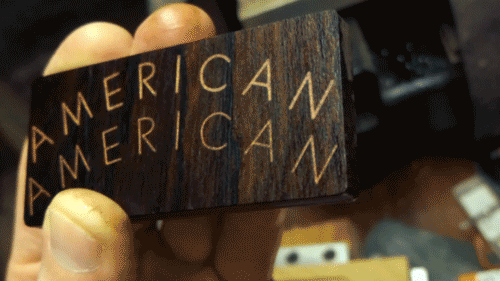
As luck would have it - that was a reasonably successful effort, but on smaller typography where there are tiny islands of wood (like the inside of the A) - or long sharp corners (M's N's etc.) there's a constant danger of tear-out, which is what happened here:
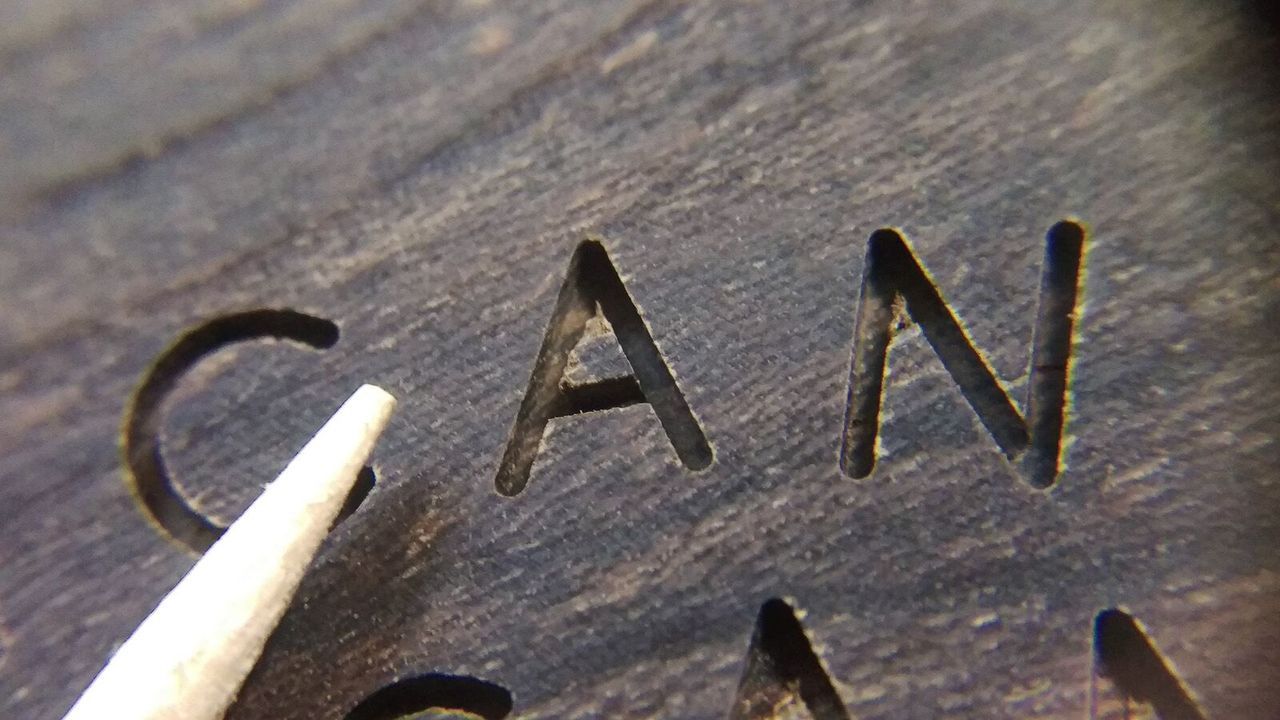
(Point of a cocktail stick for reference :lol: )
There's a brief video of the cutting process here:
YouTube link
If this were a one or two-off object I'd probably cut as normal (expecting a bit of tear-out) fill any resultant tear-out with a resin mixed with dust particles from the wood, and then re-cut the repaired sections relying on the resin to hold everything together.
The problem is that if the project goes ahead I'll need to make around 60 off, in batches, where I can't really afford the time to have my router sat doing nothing whilst I fill the problem areas and allow the resin to cure in situ before re-cutting.
So - Is there an elegant/clever way to stabilise the surface of the wood (up to a depth of 1mm) to eliminate this kind of tear-out? I've heard of Cactus Juice et al - but when I've seen it used in the past (from where I was standing) it appeared to be a waste of time - furthermore, it's not recommended for close-grained or oily woods - Ziricote falls into both of those categories..! - maybe it's close grained nature means that I'm asking the impossible and just need to bite the bullet when the time comes and repair what needs repairing...
Thanks for reading this far - any suggestions..?
Wal.