Hi all,
I've put this in the General section as it's a woodworking tool, although all the fixing is going to be metalwork. Mods, please feel free to move the thread at your discretion.
A few months ago, Doris bought a bandsaw:
inca-205-bandsaw-what-s-missing-t103536.html
We knew it had bits missing (upper guides, mostly) so it was a bit of a gamble, but a more serious problem has presented itself. I set it up with a blade just to see how it runs. There was a lot of vibration and very quickly the blade ran off the wheels. The tracking adjustment was fine but the lower wheel had come loose on its shaft. We found that the washer holding the wheel onto the motor shaft had buckled because it was too thin. Therefore there was no tension on the screw. It doesn't help that Incas turn "backwards" (i.e. anti-clockwise) compared to a regular bandsaw.
This was replaced with a new stout washer around 3mm thick:
This stopped the wheel coming loose, but the vibration remained.
I tested the rim of the wheel with a dial gauge and found around 0.013" radial runout, and 0.035" axial runout (both measured with the tyre removed):
The motor shaft itself is dead on, and runs smooth when the wheel is removed. Suspecting a twisted wheel, I put it on a surface plate and gauged it again. It's not perfect, but it's fairly close:
In the process I discovered that my parallels aren't matched (one is 0.004" taller than the other) so I need to double check this.
The wheel also has some play on the shaft, rather than being a sliding fit. Apart from having a wonky shaped hole, it is also bell-mouthed towards the rear. Measurements to follow.
Now my plan is to mount the wheel onto a faceplate on the lathe, get the rim running true, bore out the wonky centre hole, plug it and re-bore it. Alternatively to plugging it, I could just bore it and turn an adapter sleeve.
Onwards and upwards.....
I've put this in the General section as it's a woodworking tool, although all the fixing is going to be metalwork. Mods, please feel free to move the thread at your discretion.
A few months ago, Doris bought a bandsaw:
inca-205-bandsaw-what-s-missing-t103536.html
We knew it had bits missing (upper guides, mostly) so it was a bit of a gamble, but a more serious problem has presented itself. I set it up with a blade just to see how it runs. There was a lot of vibration and very quickly the blade ran off the wheels. The tracking adjustment was fine but the lower wheel had come loose on its shaft. We found that the washer holding the wheel onto the motor shaft had buckled because it was too thin. Therefore there was no tension on the screw. It doesn't help that Incas turn "backwards" (i.e. anti-clockwise) compared to a regular bandsaw.
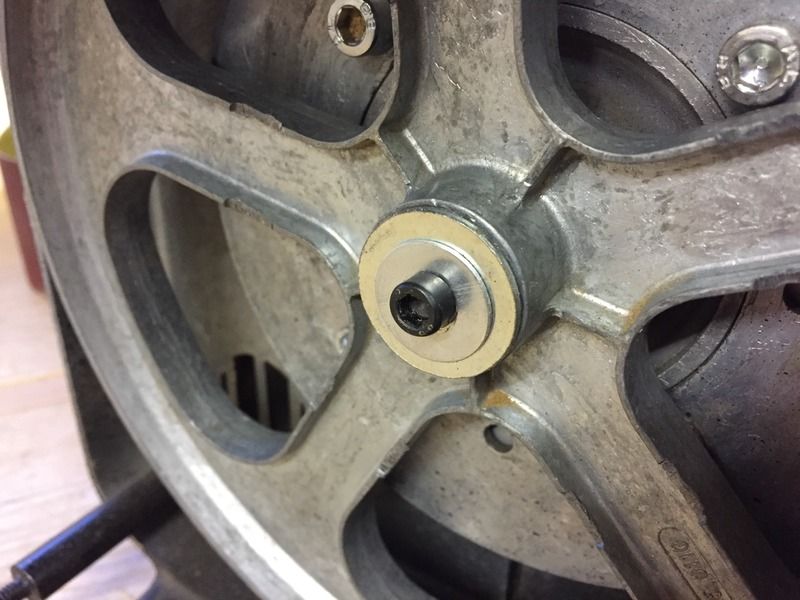
This was replaced with a new stout washer around 3mm thick:
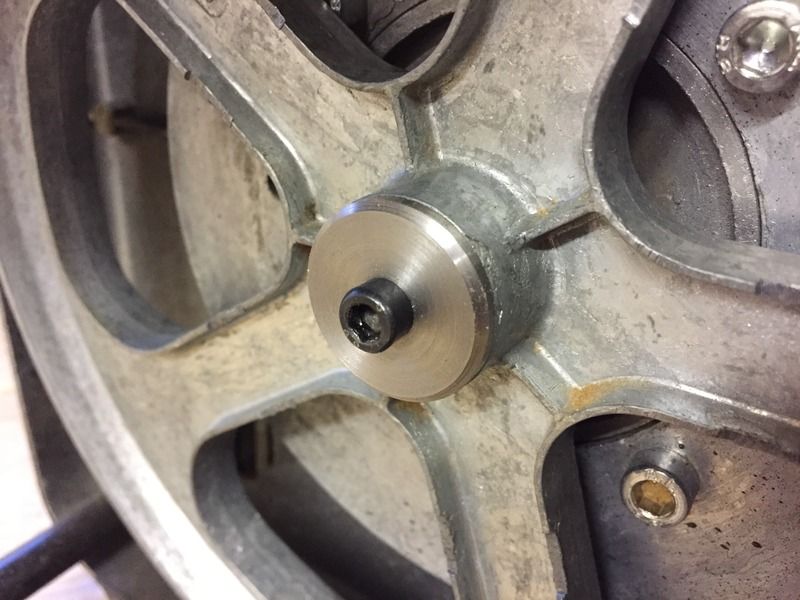
This stopped the wheel coming loose, but the vibration remained.
I tested the rim of the wheel with a dial gauge and found around 0.013" radial runout, and 0.035" axial runout (both measured with the tyre removed):
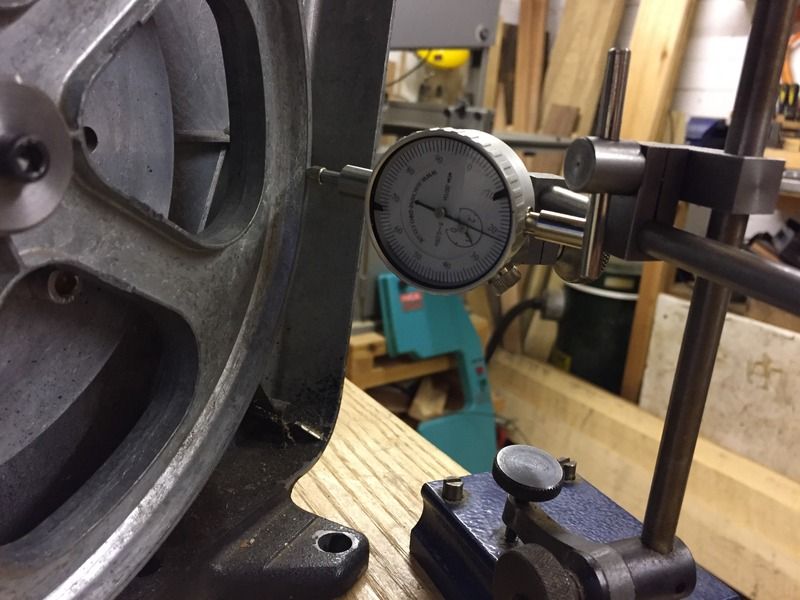
The motor shaft itself is dead on, and runs smooth when the wheel is removed. Suspecting a twisted wheel, I put it on a surface plate and gauged it again. It's not perfect, but it's fairly close:
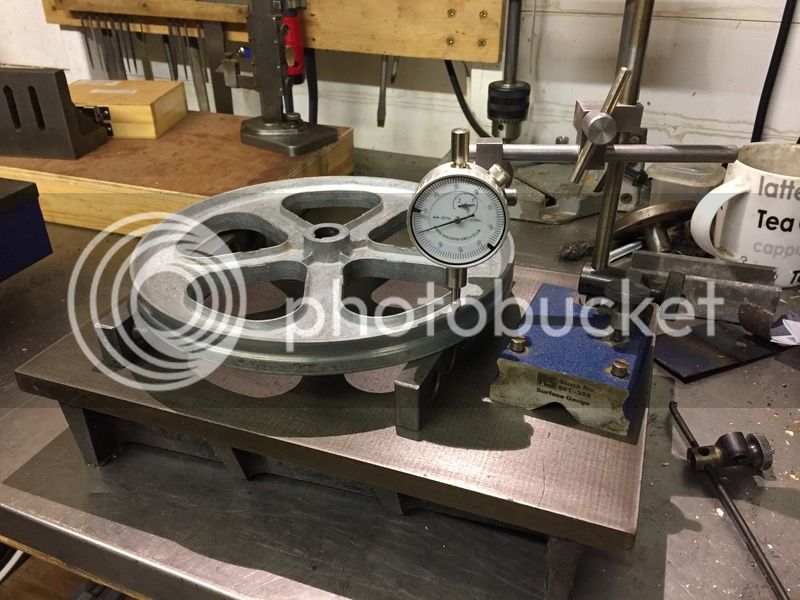
In the process I discovered that my parallels aren't matched (one is 0.004" taller than the other) so I need to double check this.
The wheel also has some play on the shaft, rather than being a sliding fit. Apart from having a wonky shaped hole, it is also bell-mouthed towards the rear. Measurements to follow.
Now my plan is to mount the wheel onto a faceplate on the lathe, get the rim running true, bore out the wonky centre hole, plug it and re-bore it. Alternatively to plugging it, I could just bore it and turn an adapter sleeve.
Onwards and upwards.....