LocalOak
Established Member
Hi
Having played with my new but very old Myford ML8 for a bit I have tried my hand at making a bowl. This is my first proper attempt at it and I realise turning can become seriously addictive.
I did it with the set of carbon steel tools I inherited with the lathe, and grinding them sharp is still pretty hit and miss. I cut a round from a piece of 2 1/2 inch oak, glued it to a blank screwed to a faceplate. No chuck or turning it around or anything like that. Used mainly a round nosed scraper and bowl gouge, and a small bit of pointed scraper to produce the bit of beading at the top of the bowl.
Did everything by eye and finger, and I have discovered what is probably an ancient technique for getting the bowl walls thin. Apply the bowl gouge, lose concentration, dig in and have shave to everything back down to remove the deep groove. Did this a number of times and you eventually get an acceptably thin wall
I struggle to part well, and find the parting tools bounces around a lot and much to my frustration managed to pop the bowl off before I was ready, had sanded but not coated. Had to pare off the remaining spigot. Coated by by hand and couldn't get the same lustre, and having no vacuum chuck, or anything chuck like at all, have had to accept that. [Edited this para to make sense, previous version didn't]
I have loads of questions but the main one is about finishing. I use refined beeswax for the oak things I've made before but when I applied it to this bowl what was a 400 grit smooth finish raised up instantly and the whole bowl is now rough. I've never had this problem before so my question is what could I use for turned oak and in what order should I apply it?
Here are some pics, not great but they show the shape. Its about 4 inches across and is based on nothing except what came out of my hands and gouges as I went at it.
Thanks
Toby
Having played with my new but very old Myford ML8 for a bit I have tried my hand at making a bowl. This is my first proper attempt at it and I realise turning can become seriously addictive.
I did it with the set of carbon steel tools I inherited with the lathe, and grinding them sharp is still pretty hit and miss. I cut a round from a piece of 2 1/2 inch oak, glued it to a blank screwed to a faceplate. No chuck or turning it around or anything like that. Used mainly a round nosed scraper and bowl gouge, and a small bit of pointed scraper to produce the bit of beading at the top of the bowl.
Did everything by eye and finger, and I have discovered what is probably an ancient technique for getting the bowl walls thin. Apply the bowl gouge, lose concentration, dig in and have shave to everything back down to remove the deep groove. Did this a number of times and you eventually get an acceptably thin wall
I struggle to part well, and find the parting tools bounces around a lot and much to my frustration managed to pop the bowl off before I was ready, had sanded but not coated. Had to pare off the remaining spigot. Coated by by hand and couldn't get the same lustre, and having no vacuum chuck, or anything chuck like at all, have had to accept that. [Edited this para to make sense, previous version didn't]
I have loads of questions but the main one is about finishing. I use refined beeswax for the oak things I've made before but when I applied it to this bowl what was a 400 grit smooth finish raised up instantly and the whole bowl is now rough. I've never had this problem before so my question is what could I use for turned oak and in what order should I apply it?
Here are some pics, not great but they show the shape. Its about 4 inches across and is based on nothing except what came out of my hands and gouges as I went at it.
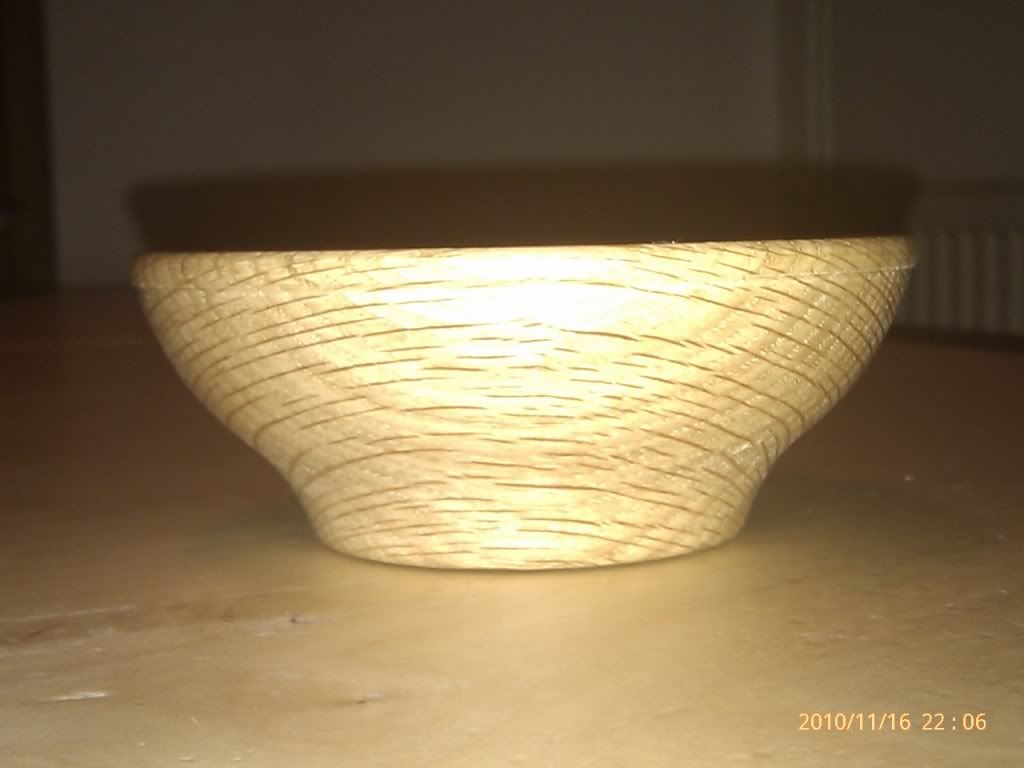
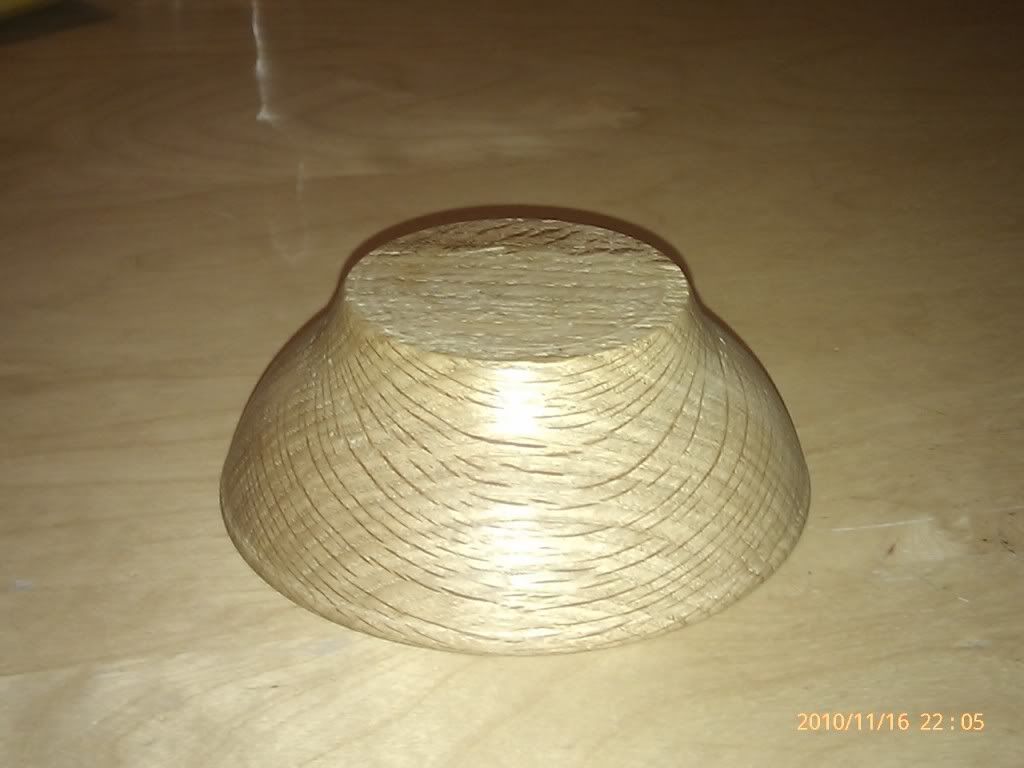

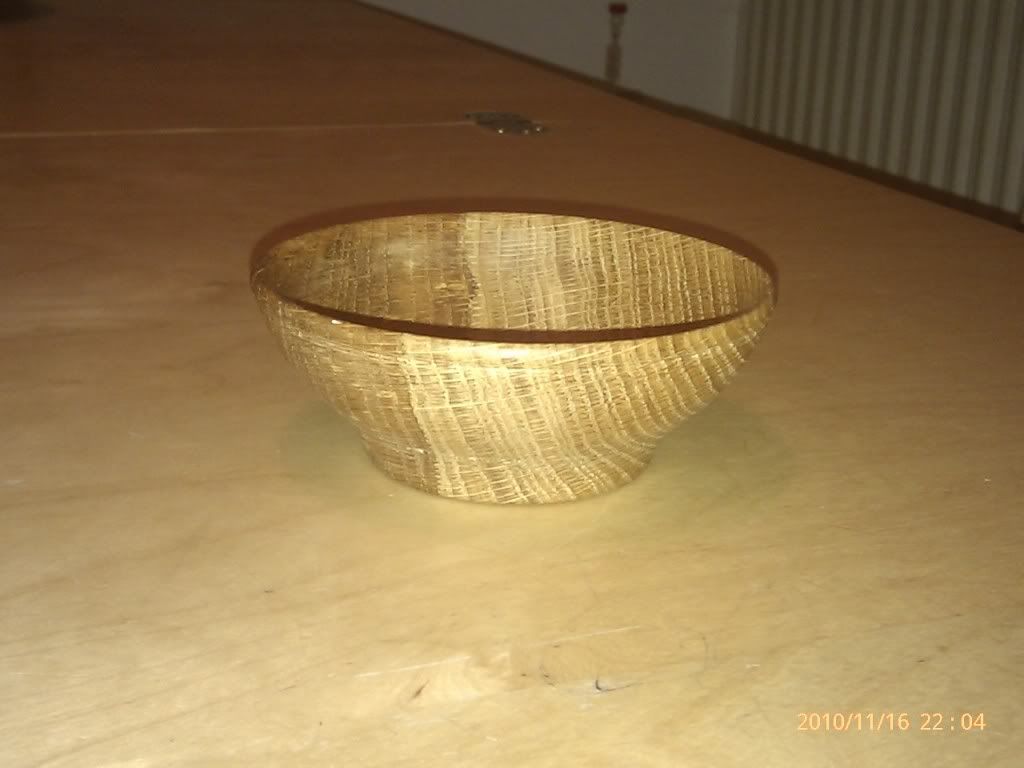
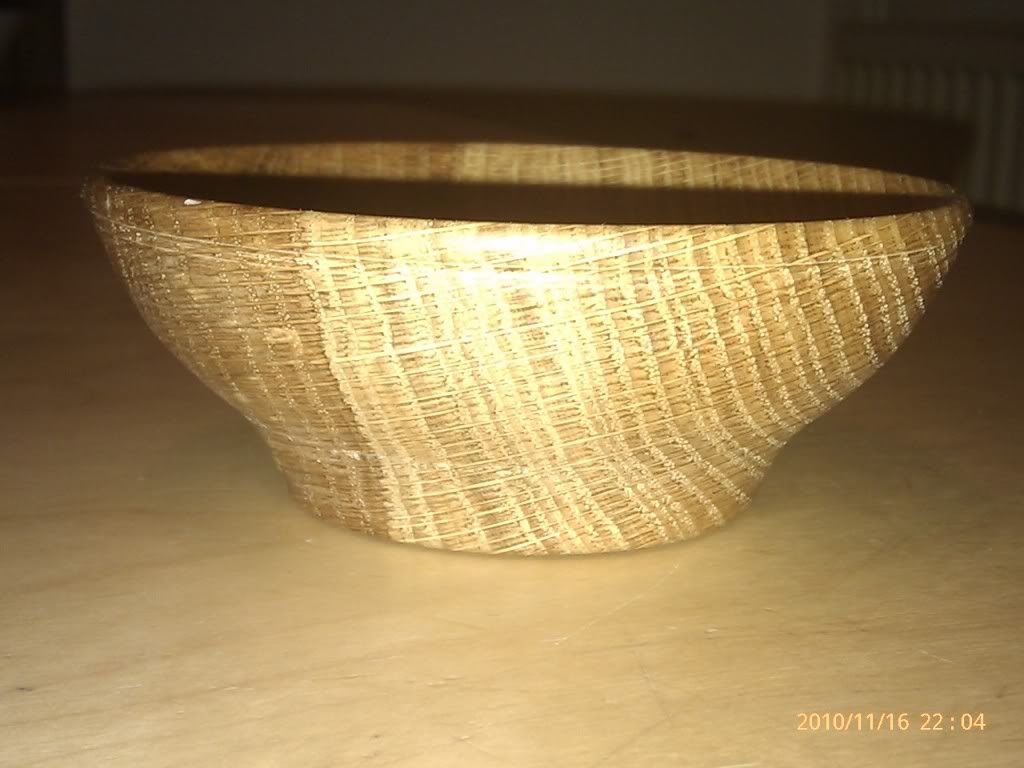
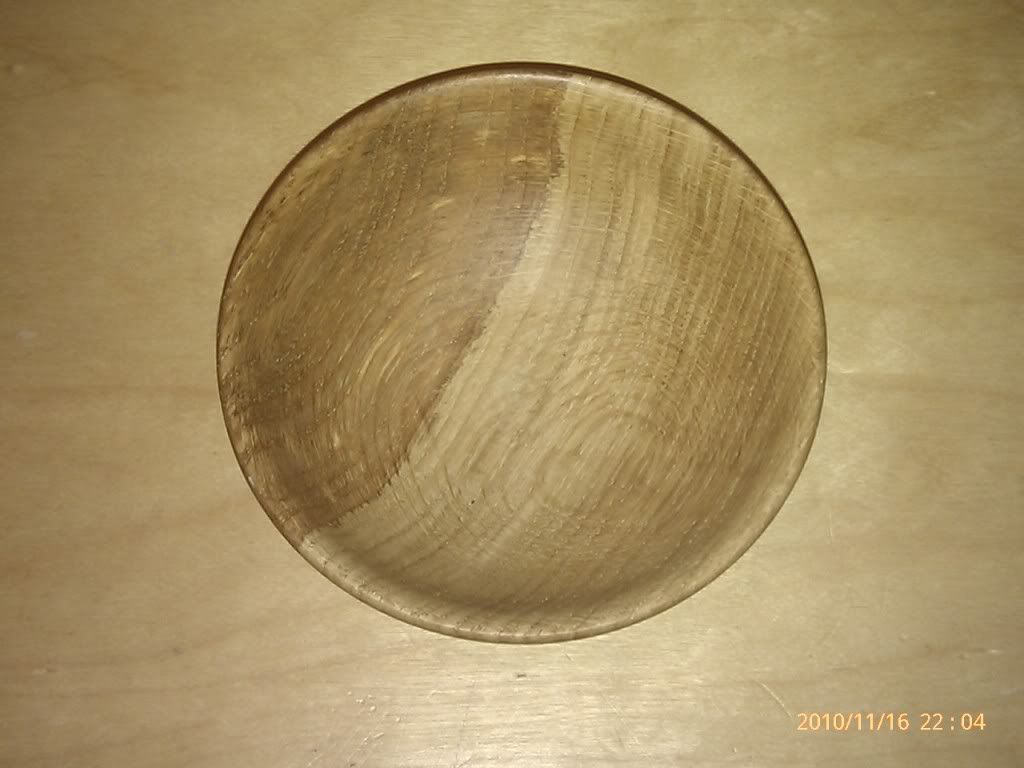
Thanks
Toby