- Joined
- 19 Mar 2007
- Messages
- 5,290
- Reaction score
- 377
I decided to have a try at Technomadges thread cutting idea. I don't have the X/Y table so I decided to press an off-cut of a worktop I put in our laundry room. A bit rough and ready, but it seems to be going OK so far?
The slide is fitted with some ali angle that I had and I cut the slots in the base with my Ryobi One thin kurf circular saw. Even managed to get the cuts straight. Recessed the angle in the slide. The top surfaces are together so they are slippery.
Then a slot was routed in the base to take a screwed rod and 2 metal plates were made to hold it.
I made a carrier pin out of a wing nut and recessed a captive nut into the slide to take the wingnut 'pin'
And now I am waiting for some friends to bring me some 3/4 16 threaded rod and nuts for the chuck. That is the thread on my chuck fortunately.
I'll post again when it moves on!! It seems solid on the lathe and I keep my fingers crossed!
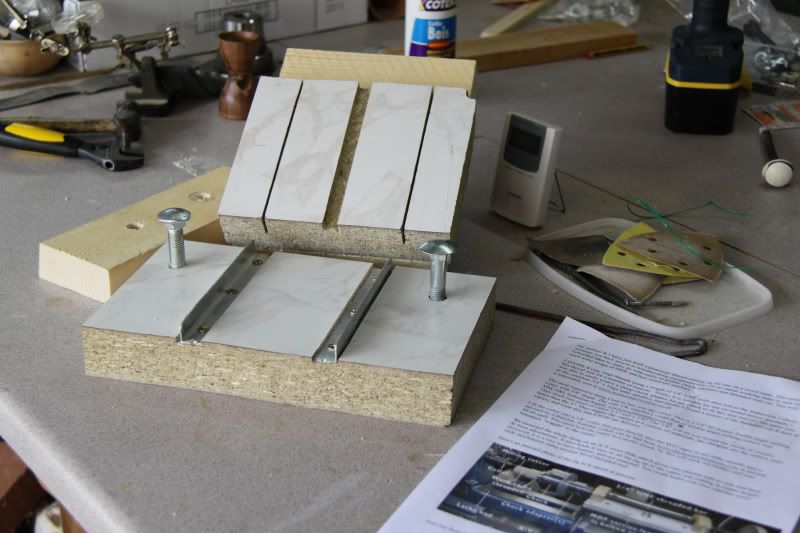
The slide is fitted with some ali angle that I had and I cut the slots in the base with my Ryobi One thin kurf circular saw. Even managed to get the cuts straight. Recessed the angle in the slide. The top surfaces are together so they are slippery.
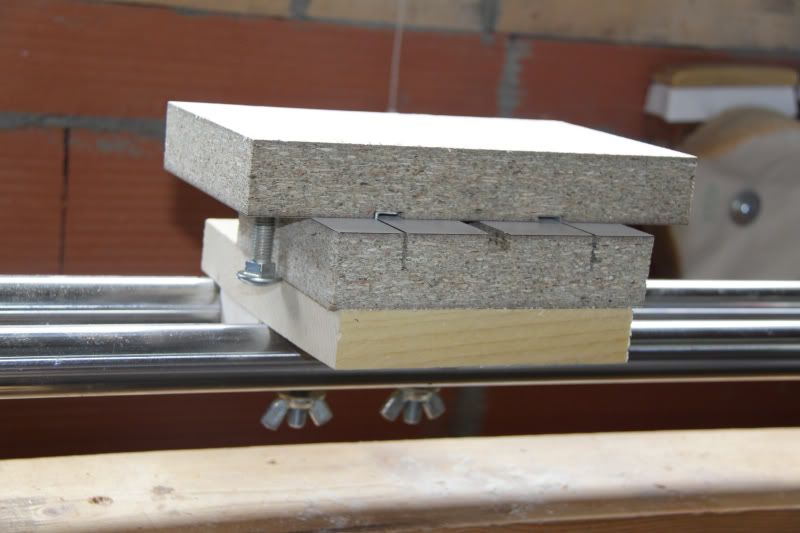
Then a slot was routed in the base to take a screwed rod and 2 metal plates were made to hold it.
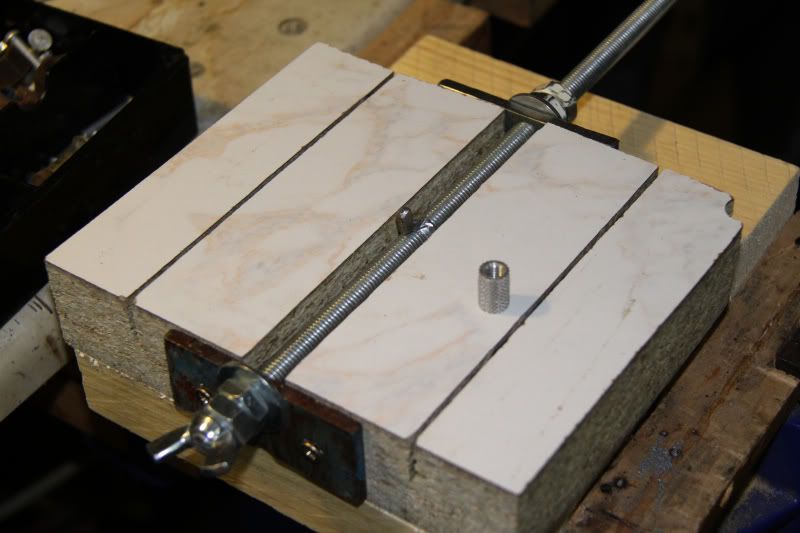
I made a carrier pin out of a wing nut and recessed a captive nut into the slide to take the wingnut 'pin'
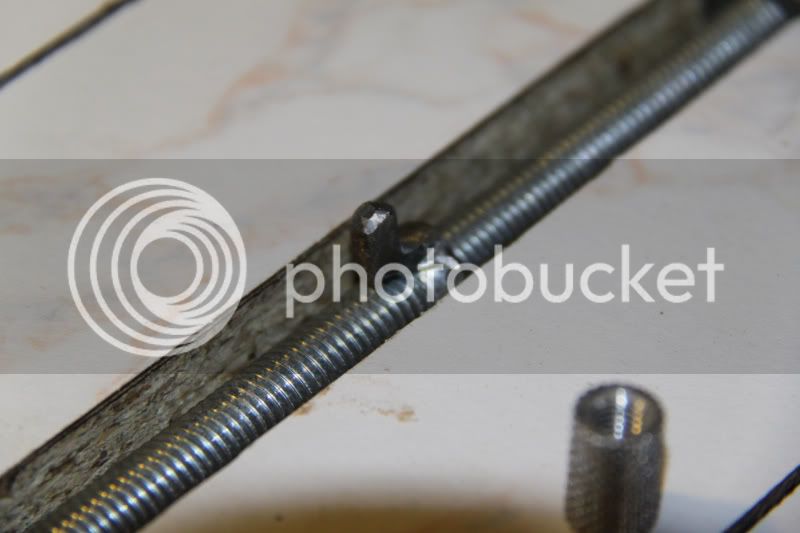
And now I am waiting for some friends to bring me some 3/4 16 threaded rod and nuts for the chuck. That is the thread on my chuck fortunately.
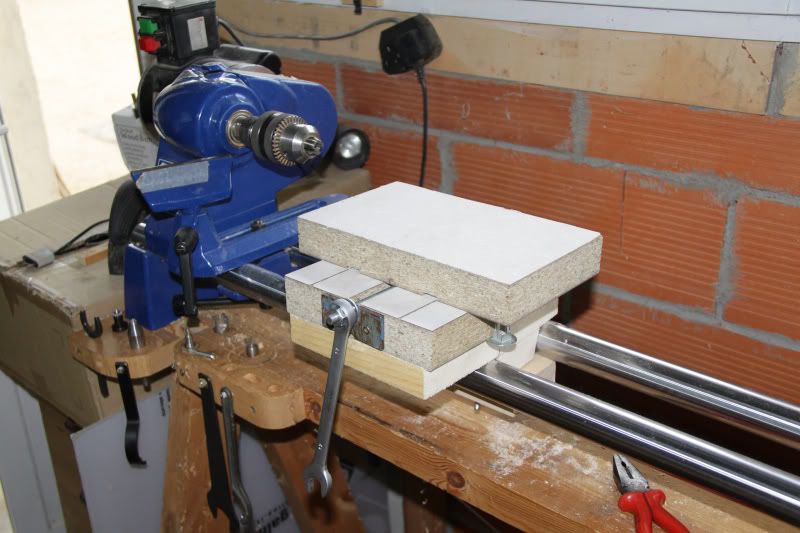
I'll post again when it moves on!! It seems solid on the lathe and I keep my fingers crossed!